Balancing Act
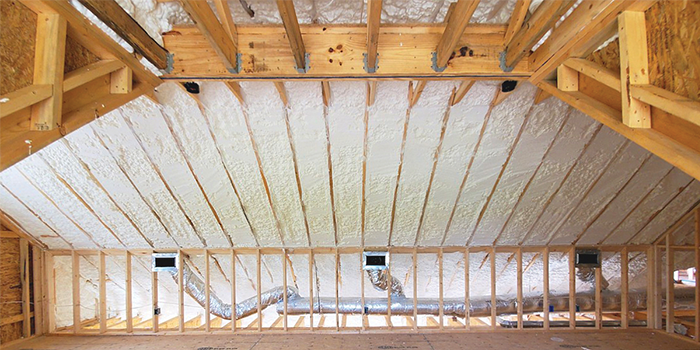
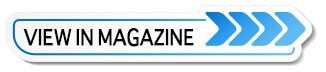
SPRAY FOAM MAGAZINE – In the world of building insulation, the concept of economic thickness plays a crucial role in determining the most cost-effective and energy-efficient solutions. Economic thickness refers to the optimal thickness at which the cost of adding more insulation is balanced with the resulting energy savings. This delicate balance between upfront costs and long-term benefits is pivotal in making informed decisions regarding insulation strategies.
The economic thickness of spray foam insulation is a dynamic parameter influenced by several factors, including the local climate, energy costs, building design, the specific type of spray foam used, and local building regulations. Here are key considerations when determining the economic thickness of spray foam insulation:
Energy Costs
An essential aspect of economic thickness, and its impact on a building’s energy performance, is understanding and comparing the total costs of both insulating and heating and cooling the building long-term. This will provide the most accurate understanding of return on investment (ROI) between spray foam and traditional fiberglass insulation.
Currently, spray foam insulation carries a higher upfront cost compared to fiberglass. However, fiberglass insulation’s lower R-value, lack of air sealing, and decreased energy efficiency result in higher long-term energy expenses than spray foam. Spray foam insulation offers superior thermal resistance (R-value) and airtight sealing, contributing to long-term energy savings, winning over fiberglass insulation as a long-term investment.
The use of spray foam also reduces the tonnage needed in the building’s HVAC systems, reducing upfront and replacement costs up to $2,000 per ton depending on the system.* In areas where energy costs are higher, there may be a stronger incentive to invest in spray foam insulation where there’s an even higher and faster return on investment through reduced energy costs.
Local Climate
The local climate has a significant impact on the heating and cooling requirements of a building. Different climates present varying heating and cooling demands, influencing the ideal thickness of insulation for energy efficiency.
In colder climates, where heating demands are prominent, a thicker layer of insulation is often required to minimize heat loss. The economic thickness tends to be higher in regions with cold winters to ensure that the building remains thermally efficient.
Conversely, in warmer climates, the emphasis is on reducing cooling costs. The economic thickness in these regions may be lower, as the primary goal is to limit heat gain and maintain a comfortable indoor climate.
Building Design and Usage
The design and purpose of the building influences the economic thickness. For example, commercial buildings with extended operating hours may benefit more from increased insulation than residential structures. The orientation of the building, the presence of large windows, and other architectural considerations affect its overall energy efficiency.
Type of Spray Foam Insulation
The choice between open-cell and closed-cell spray foam impacts economic thickness. Closed-cell foam generally has a higher upfront cost but requires less thickness to achieve the desired insulation level. In cold climates where condensation control is required, closed-cell foam can provide a more economical solution by providing 3 control layers in 1 step.
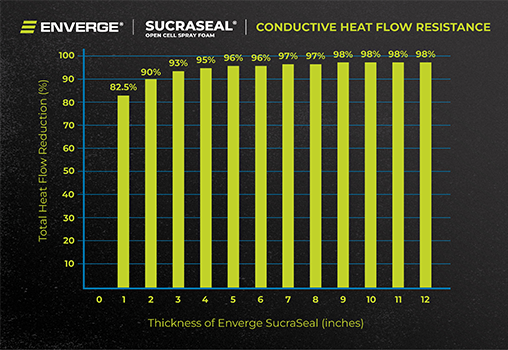
Design Considerations
Designers, builders, and homeowners need to consider the local climate, building codes, and appropriate ventilation strategies when implementing the economic thickness of insulation and airtightness measures. This includes selecting materials and systems that allow for moisture management and airflow control.
Regulatory Considerations
Building codes and energy efficiency standards can influence the required thickness of insulation. These codes specify minimum requirements for insulation levels based on the expected climate conditions, and compliance with these regulations is essential for both legal and economic reasons. Newer codes require thermal resistance based on total assembly performance, not cavity R-values. The 2021 IECC considers R-Value alternative compliance and requires 30% or more R-value when the total assembly is not calculated.
R-Value (Conductive) is important but it is the reduced air leakage (Convective) in conjunction that has the biggest impact on energy efficiency, indoor air quality, and comfort. While spray foam takes care of conductive, convective, and radiant heat flow, reduced R-value (Economic Thickness) does not meet Prescriptive Code Compliance. The Building Code allows for other pathways of Code Compliance where the R-Value can be less than Prescriptive, where the other systems in place will allow for a performance-based approach to Code Compliance. These include dramatically reduced air leakage, an unvented attic (HVAC in conditioned space), right-sized HVAC, and fresh air introduction. Performance based methods for Code Compliance are still misunderstood in the marketplace, and more education is needed.
The chart below illustrates heat flow reduction with insulation that has an average R-value of 3.6 per inch, which includes open-cell foam.** Once 6 inches of spray foam has been installed, 96% of conductive heat flow has been stopped. From 6 inches to 12 inches heat flow is only reduced 2% more, while doubling the insulation thickness (R-Value) and doubling the cost. It is very difficult to justify the additional cost of adding insulation beyond 5.5” R20.35 making this depth the “Sweet Spot” for Economic Thickness.
Benefits of Optimizing Economic Thickness
Optimizing economic thickness ensures the insulation is providing the maximum energy efficiency for the specific building and climate conditions. Investing in insulation beyond the point of diminishing returns may not result in significant additional energy savings. Achieving the right economic thickness also contributes to sustainability by reducing energy consumption and, consequently, the carbon footprint of a building.
Spray foam insulation, with its versatility and high-performance characteristics, offers a valuable solution in this context. Sustainability has become a cornerstone in modern construction practices, and spray foam insulation, with its ability to reduce energy consumption and greenhouse gas emissions, aligns with the growing global commitment to sustainable building solutions. The longevity of spray foam insulation and its minimal maintenance requirements contribute to a more sustainable life cycle for buildings, reducing the need for frequent renovations and material replacements.
Looking ahead, advancements in insulation technologies and a growing emphasis on eco-friendly construction methods will likely reshape the landscape of economic thickness considerations. Collaboration between industry stakeholders, researchers, and policymakers will play a pivotal role in establishing standards that promote both economic viability and environmental responsibility. As we continue to navigate the challenges of a rapidly changing world, the judicious application of economic thickness principles in spray foam insulation remains a cornerstone in constructing buildings that are efficient, cost-effective, and resilient to the evolving demands of a sustainable future.
By considering local climate, energy costs, building design, and regulatory requirements, stakeholders can make informed decisions to achieve optimal economic thickness, resulting in energy-efficient and cost-effective buildings. As the construction industry continues to prioritize sustainability, the role of economic thickness in insulation strategies will remain a key consideration in creating energy-efficient and environmentally conscious structures. Spray foam is the clear choice, and economic thickness plays a crucial role in maximizing these returns.
*Spray Foam Magazine does not take editorial positions on particular issues; individual contributions to the magazine express the opinions of discrete authors unless explicitly labeled or otherwise stated. The inclusion of a particular piece in the magazine does not mean that individual staff members or editors concur with the editorial positions represented therein.
For use by SprayFoamMagazine.com & Spray Foam Magazine
Disqus website name not provided.