Happy to Sea You
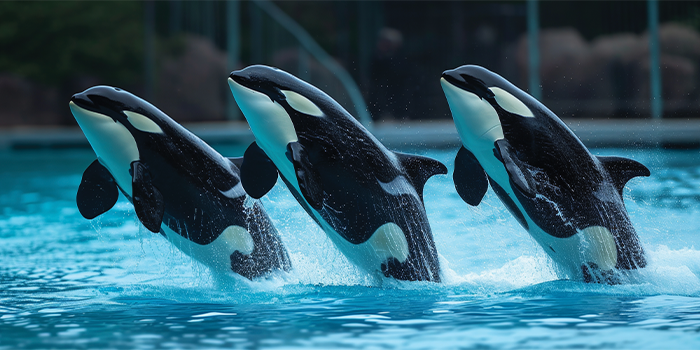
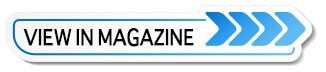
SPRAY FOAM MAGAZINE – Situated in southern California’s Mission Bay, SeaWorld San Diego is but a stone’s throw away from the idyllic beaches of the Pacific. SeaWorld San Diego entertains over three million park visitors a year, delighting guests of all ages with its 19 saltwater aquariums filled with an array of rescued and rehabilitated marine life, plus hair-raising thrill rides and breath-taking live shows. In March 2024, the park celebrated its 60th anniversary, and it remains as committed as ever to making sure its visitors have a whale of a time, every time.
SeaWorld San Diego’s latest project focuses on first impressions as it completely remodels its main entrance area for the first time since 2012. As part of the remodel, the park is building two brand-new canopies– one ticketing canopy, and one security bag-check canopy– which all guests will walk under on their way in and out of the park. The roofing experts at Cool-Roof Systems were enlisted to protect the canopies from Mission Bay’s humid, salty air by applying a specially designed spray foam system to the canopies’ metal roof decks.
Cool-Roof Systems is based in San Marcos, California, just a half an hour away from SeaWorld San Diego. The team at Cool-Roof specializes in applying spray foam systems to commercial and residential roofs. Cool-Roof is the premier spray foam contractor for Level 10 Construction, the general contractors who have completed a number of construction projects for SeaWorld since 2019.
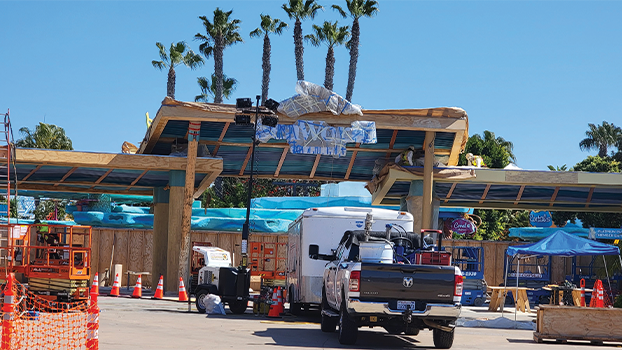
Cool-Roof workers cover parts of the canopy with paper and painters’ tape to protect from overspray. Plastic covers the SeaWorld signage on all sides
Level 10 approached Cool-Roof about foaming the SeaWorld San Diego entrance canopies, and Cool-Roof readily accepted.
Will Evans is the Senior Project Manager and Chief Operations Officer at Cool-Roof Systems, and he oversees a team of thirty field workers, four spray foam rigs, and a slew of projects all over California. For the SeaWorld job, Evans coordinated with Level 10 to nail down the project’s specifics, provide a takeoff estimate, and dispatch the best manpower and materials for the job.
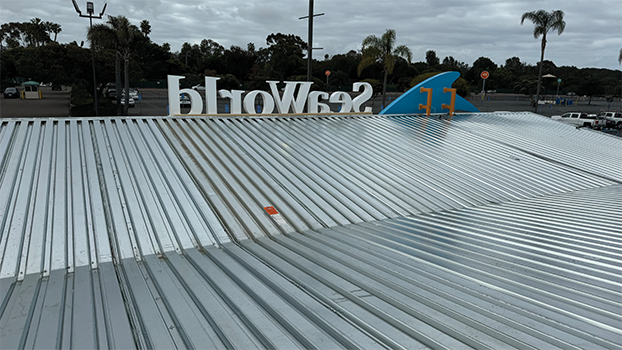
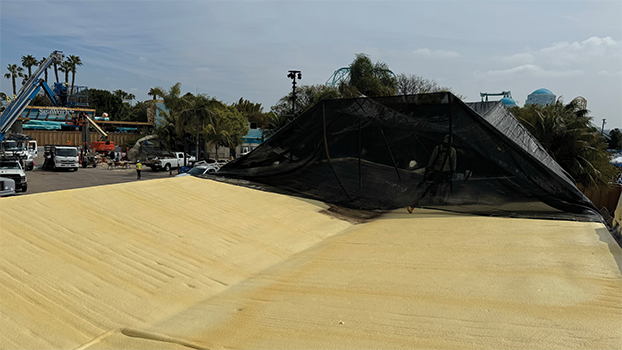
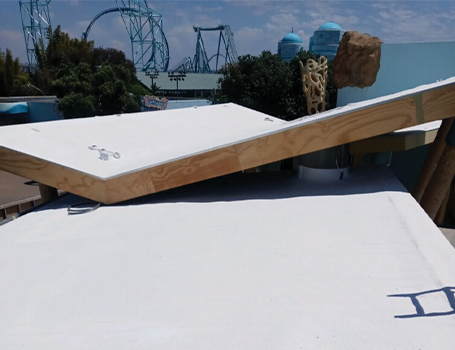
FROM TOP TO BOTTOM: A view of the new roof deck before surface prep and spraying; Workers move the spray tent from section to section before spraying. The second canopy is in the background having its signage installed; The finished roof deck looks bright white after applying the granules atop the foam layer
To provide an accurate estimate, Evans reviewed the plans sent over by the architect, and collaborated with both the architect and with Level 10 to address all SeaWorld’s expectations. All parties worked together to decide the most resilient foam system to use on the canopies, which required some consulting on Evan’s part.
“The architect wasn’t very familiar with spray foam, so we had to explain how a few funky details would work.” Evans explains, “We also consulted with the metal contractor about the custom-edge flashing they’d be building.”
Edge flashing is installed to the roof deck’s termination points and prevents roof leakage by diverting water off the edge of the roof and stopping water from dripping inward toward the roof deck. Used in tandem with the spray foam layer the canopies’ roof decks would be impenetrable to moisture.
Ordinarily, spray foam is used on the roof decks of buildings due to its insulating, sound-dampening, and air-sealing properties. Its purpose on the two entrance canopies at SeaWorld San Diego is a little different. The two wood-framed canopies are open on all sides, and have no walls– essentially, they’re all roof. The canopies’ lack of walls negates the need for spray foam’s insulative qualities, but the metal roof deck still needed a vapor barrier to protect it against rust and wear from the salty, moisture-laden air common in Mission Bay. Without the protective foam barrier, the canopies would slowly corrode over time, eventually becoming unsightly and unsafe. Cool-Roof Systems knew just the right spray foam system to guarantee the two canopies are built to last and are so confident in their expertise and craftsmanship they even provided SeaWorld with a No Dollar Limit (NDL) warranty on their roof system.
After Evans delivered the estimate and solidified the project’s plans, a team of four from Cool-Roof Systems headed to SeaWorld San Diego at the end of March 2024. The park remained open to the public despite construction, and visitors were simply funneled through a temporary entrance. The job site itself was quite busy and the Cool-Roof team worked alongside contractors from Level 10 and other tradespeople like framers and electricians, many of whom had already been hard at work on the project before Cool-Roof arrived.
Protecting the surrounding area from overspray was crucial to safeguard the progress other trades had already made. Though the canopies themselves were still under construction, the brand-new park decor had already been painted and set up. This included the SeaWorld signage secured to the entrance canopy’s roof. Before foaming, all decorative elements had to be completely covered and protected with plastic and paper to prevent any mess from errant foam.
Besides wrapping nearby decor in protective paper and plastic, Cool-Roof also sprayed the entire roof deck from under a massive, tented shelter. What’s more, being right near the coast meant the team had to time their sprays just right or else the excessive humidity could prevent the foam from properly adhering. The moisture in the air was a huge challenge every morning with high humidity occurring until 10 or 11 a.m. every day. The team had to stick to a spray window between 11a.m. and 3 p.m. every day for the best results. This spray window made an already tight schedule even more crunched. But true to the company namesake, the Cool-Roof Systems team kept calm and foamed on.
Before firing up the reactors, the team had to perform some surface preparation, even though the metal roof deck was new construction and in clean condition. They applied a primer to the metal to ensure the best foam adherence and made sure the roof was clean and free of dust and debris. Because they were working on top of the canopy’s roof, they took various fall protection measures, such as establishing a tie-off point and wearing harnesses and lanyards while working. They also wore long sleeves, pants, boots, hard hats, gloves, and reflective safety vests to comply with the construction site’s safety standards. While spraying, they wore eye protection and 3M respirators.
The two canopies’ roofing decks were each made with fluted metal, which requires skill and precision to ensure an even application on the non-flat surface. Using a Graco E30 Reactor and a Graco GX-7 spray gun, the sprayers filled each of the flutes with about two inches of General Coatings’ Ultra-thane 230, a 2.7 lb density polyurethane foam. After filling the flutes, they used a roof scarfer and Sawzalls to uniformly trim the excess foam down flat.
“Spraying fluted roofs are definitely more labor intensive than flat roofs due to the fact we have to fill the flutes and then go back and trim off all the excess foam,” Evans recalls, “If it was just a standard, corrugated metal roof, we could spray it flat without the extra trimming.”
After the foam was trimmed and dried, the team also added General Coating’s Ultra-Guard 5700 High Solids, a silicone coating over the top of the foam layer for extra protection and longevity. They also went a step further and embedded a layer of ceramic granules.
“The granules deflect water when it rains, and also add to the strength of the silicone topcoat.” Evans explains.
In total, they sprayed about 6,000 square feet between the two canopies. At the outset, the SeaWorld project seemed like a relatively straightforward and quick gig; it would only tie up four Cool-Roof employees and a single foam rig and wasn’t expected to take more than ten days. But however straightforward it had seemed at first, it quickly became clear the job was not without challenges–both logistical and meteorological.

A crane lifts the ticketing canopy’s frame into place
Several delays occurred due to other trades needing to do priority work on the canopies, such as the electrical work. The most frustrating and frequent delays were caused by the finicky coastal weather, like severe storms and high humidity all throughout March and April.
As a project manager, Evans is no stranger to rolling with the punches on project delays, and the SeaWorld job was no exception.
“If it hadn’t been for the delays, we realistically could have been finished in seven to 10 days,” said Evans, “SeaWorld was really pushing to have everything open in time for spring break.”
Unavoidable delays may have pushed back the two canopies’ big reveals by a few weeks, but as any craftsman knows, perfection can’t be rushed. SeaWorld San Diego now expects to make waves with its newly rebuilt and foam-fortified main entrance canopies by Summer of 2024.
For use by SprayFoamMagazine.com & Spray Foam Magazine
Disqus website name not provided.