High Performance with a New Look
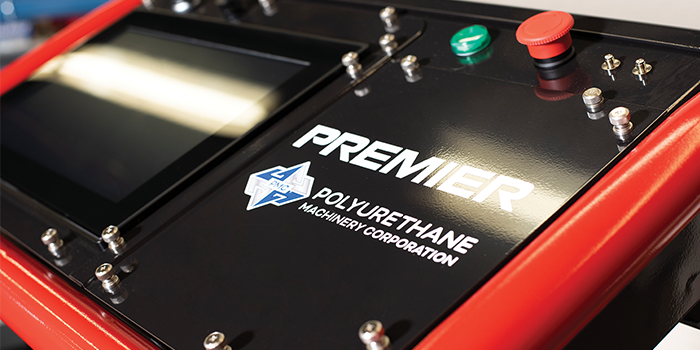
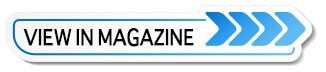
Spray Foam Magazine – Polyurethane Machinery Corporation (PMC) recently released two innovative machines, the PK-25 and the Premier machine. Both newly engineered machines are exciting news for contractors as they have the potential to make applications increasingly efficient and functional. PMC also introduces its exciting new branding – with a newly designed logo and a sleeker powder coated finish, which incorporates a new black and red color scheme. On the cutting edge in terms of technology and design, their new air machine has a vertical pump layout and air motor to reduce the footprint and minimize CFM required to operate the unit.
The Premier is equipped with the latest programmable logic controller (PLC) technology and electronic flow meters to introduce and release this unit as one of the top configurations on the market. These units were configured by PMC’s topnotch engineering department.
Eager to find out more information, the Spray Foam Magazine team (SFMT), spoke to James Shevlino, Director of Operations at PMC.
Spray Foam Magazine: Is there anything unique about the PK-25 proportioner compared to other foam and coating proportioners?
James Shevlino: The PK-25 has been designed to be utilized for concrete lifting and in the bedliner industry, this unit is aggressively priced and is a no frills, lightweight, small footprint, low consumption, high output solution for plural component applications. Made in America and pumping up to 25lbs per minute at 20 CFM, with a negligible amp draw, this machine stands out in terms of efficiency, quality, and price point.
SFM: Have you received any feedback from contractors regarding the PK-25?
JS: The PK-25 has gone through extensive field testing, and feedback from contractors has been essential in refining its design. The common theme in the feedback we’ve received from contractors is, the equipment is straight forward, resilient, and reliable.
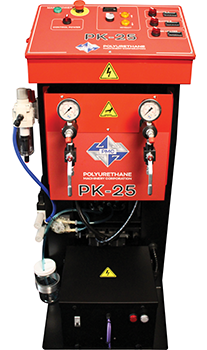
SFM: How can the PK-25 positively impact a contractor’s performance on the job?
JS: With the PK-25, contractors will have the benefit of PMC quality, reliability, and ease of repair wrapped in a compact and efficient footprint. Whether it’s in the back of a van with a single set of material, a trailer, a box truck, or on a shop floor, the PK-25’s streamlined design lends itself to many types of application scenarios.
SFM: PMC has also just launched their brand-new Premier machine, a digital machine with remote capabilities. Can you please expand on these qualities and how they will positively impact the contractor?
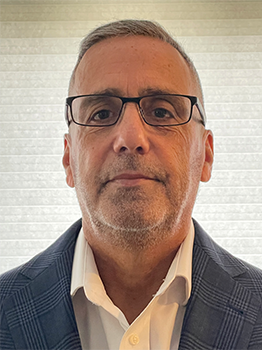
James Shevlino, Director of Operations, PMC
JS: With the Premier, contractors assume complete control of their equipment on the fly. Manage a fleet with remote access available on any internet capable device, or change the hose heat setting with a phone. The Premier offers a clean presentation of information at the home screen, straight forward controls for heaters and hose heat, upper and lower limits on outgoing and incoming material pressures, accurate flow meters that have no wear parts, and fully in depth and searchable graph reporting.
With the Premier, contractors can guarantee quality jobs – and prove as much at the touch of a button. For the customer-facing side, reports have been redesigned to highlight pertinent information, and can be printed to USB, or sent to any given email address with one tap. On the technical side, a comprehensive list of alarms is easily sortable and accessible remotely; troubleshooting is simple and direct. The primary power side of the console is made up of our familiar point to point components, with the secondary side handled by easily accessible and replaceable PLC cards – the Premier holds true to PMC’s design themes, passing value to end-users without the need for proprietary parts, making complex functionality clear and concise.
SFM: Why did PMC feel a need to make this machine?
JS: We made the Premier machine to offer contractors a high-end piece of equipment with intricate capabilities presented simply and directly. For example, the touch screen features an intuitive and uncluttered user interface, with sensible direction to each control option; complicated functions are displayed and controlled plainly, removing burden from end-users.
Ultimately, we wanted to offer a full suite of functionality to contractors that didn’t include expensive motherboard replacements.
SFM: Why is innovation so important to PMC?
JS: This industry is uniquely nuanced and complicated. Innovating creative ways to deliver simple solutions to the complex and distinct issues that contractors in this industry face, has always been at the core of PMC’s designs. Innovation is essential to the end-user, and the end-user is essential to PMC.
SFM: When first deciding on designing a new piece of equipment, what factors do you take into consideration?
JS: The first and most important factor considered when designing a new piece of equipment is efficacy for our end-users: how well does this product solve an issue for them? How can we simplify this solution? Is this part going to get lost in a rig and what can we do about it? Breaking down end-users’ day to day experiences gives us insight into the needs of the industry and serves as a guide for PMC designs.
SFM: Why do you think it’s important to have your equipment Made in the U.S.A?
JS: Having our equipment made in America affords us direct oversight on every part of each process involved in the making and assembling of our products. Machine serial numbers are associated with a Quality Report, reflecting the exhaustive testing conducted on each unit during assembly. “Made in the U.S.A.” is not just a catch phrase, it is a philosophy – one to which PMC is fully committed.
SFM: In one sentence please tell our readers what makes PMC a company that can be relied on?
JS: As a leader in equipment manufacturing in this industry, PMC is committed to our products and to our customers; we stand behind our products, ‘Made in America,’ and our devotion to this industry is unwavering.
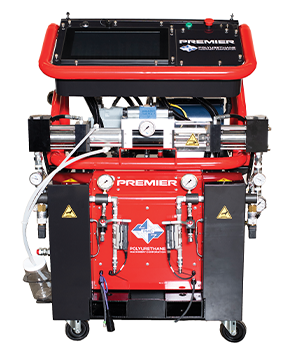
PMC’s new Premier machine, a digital machine with remote capabilities, allows contractors to assume complete control of their equipment on the fly
PMC’s world of high-functioning and responsive spray foam machinery offers great quality and reliability to the contractor. Helping them keep their projects on track with no down time. They can rest assure that their customers will also benefit by receiving efficient homes and buildings to protect their wealth and provide a better life for their families.
ABOUT POLYURETHANE MACHINERY CORPORATION (PMC)
PMC is a division of PMC Global Inc, a privately held management company with more than 20 subsidiaries in 10 U.S states spanning 17 countries worldwide. They are supported by this billion-dollar company whose roots were in the early stages of the plastics polymer modification industry. Today PMC Global dominates select markets in plastics/chemical manufacturing, packaging, finance and more.
For use by SprayFoamMagazine.com & Spray Foam Magazine
Disqus website name not provided.