Roof Detective
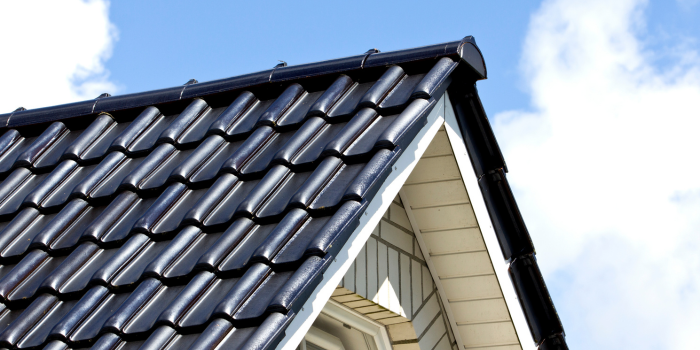
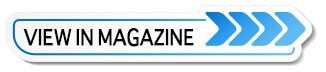
SPRAY FOAM MAGAZINE – SPF roofing is a jobsite-manufactured product that requires expertise in installation. It will perform well over its service life if you, as the manufacturer of the product, follow all the necessary steps to ensure a quality installation. With that in mind, it is imperative that a pre-bid inspection is carried out before even entering a bid. This is particularly useful in re-roof situations. A pre-bid roof inspection for an owner of either a new construction or a re-roof can be daunting. It’s therefore additionally important to document all evidence when conducting your pre-bid inspection.
BE METICULOUS This pre-bid inspection must identify several factors that will impact cost, affect service life, and your overall success. Such factors may include special architectural details (skylights, vents, and mechanical equipment), jobsite conditions and locations, overspray risks, and most importantly, the condition of the existing roofing membrane you will spray your SPF over.
While many technologies provide information on existing conditions, such as infrared scanning, they should be used to augment a destructive coring process. Coring existing roofs gives you a snapshot of that location and potential issues that may affect your successful application such as moisture and adhesion.
PLAN ACCORDINGLY There are many coring tools available in the industry, but my preferred tool is a two-inch hole saw on a cordless drill. The process involves boring through all layers of roofing down to the substrate. As this is done the core should be removed and laid out on the roof in order, and identify the number of roofs, moisture, and adhesion at that location. The core should be photographed at the minimum and in some cases removed and saved as forensic evidence of existing conditions.
CORING Destructive coring requires repair and replacement. Plan accordingly. Notify the contractor/ owner you will require destructive coring as part of your pre-bid inspection. Ask if the existing roof is leaking and the locations of the leaks. Core these areas and other “ugly” areas of the roof. The SPFA establishes minimum standards only, so core at least that number of times. In addition to destructive coring, and infrared scanning for moisture presence, a pre-bid inspection provides an opportunity to visually inspect other aspects of the job, such as issues like embedded wires, piping, and any embedded wood products.
Creating a drawing of the roof is recommended. This allows for verification of dimensions, noting architectural detailing needing correction, and the location of cores. Thinking like a contractor will help with the analysis of the roof before the bid is even entered. However, thinking like the owner of the roof will ensure that extra care and attention is taken when gathering this evidence. Remember, a roof is the first line of defense against extreme weather conditions. Pre-bids are a great way to present evidence of your findings, including normal wear and tear, and could even help the potential customer with a premature failure of your roofing system.
Think of yourself as a roofing detective, gather the information which will help provide the most accurate, competitive bid possible. This in turn, will give you a greater chance of winning a bid and solving another roofing case.
About the Author: JAMES ESTES is the owner of Sustainable Polymer Products, a SPF materials distributor. With 30 years of experience in the field of construction focusing on SPF roofing and insulation projects, James provides some common sense approaches to successful SPF applications.
For use by SprayFoamMagazine.com & Spray Foam Magazine
Disqus website name not provided.