Skin, Eyes, Hands & Lungs
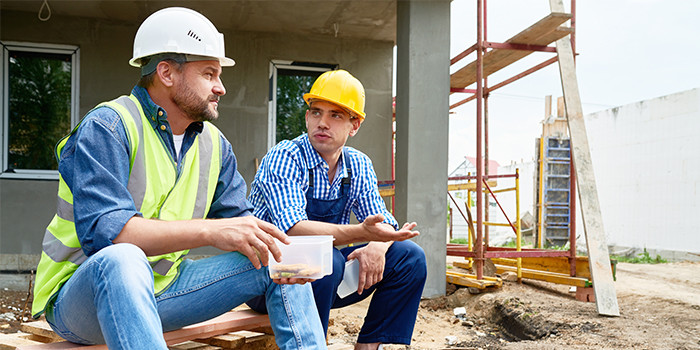
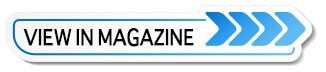
Spray Foam Magazine – Winter 2021 – There are several job responsibilities spray foam contractors undertake that do not involve direct spraying. It’s essential to remind employees, co-workers, and anyone in the immediate area, not to let their guard down when undertaking these tasks and to have proper documentation and visual aids on hand as a clear reminder.
Training: The first line of hazard defense is training. It is imperative that employees understand the importance of PPE. Making sure all workers have completed the appropriate training for health and safety, equipment, and installation before beginning any work on site, or even back at the shop, will prevent potential hazards. The training should include how to operate, fit, and put on and remove PPE. In addition to maintenance processes and how to safely dispose of protective clothing and equipment.
SPF training is provided by the Spray Polyurethane Foam Association (SPFA) Professional Certification Program, the Center for Polyurethanes Industry (CPI), Air Barrier Association of America (ABAA), Building Performance Institute (BPI), and individual SPF manufacturers to name a few.
Safety plan: Keep an up-to-date safety plan accessible for all contractors. Meet all OSHA, state, and local safety requirements for installers and for other workers.
Before spraying commences: PPE is probable for all spraying jobs; therefore, a PPE assessment is essential before starting every job. Incorporating eye and face protection, protective clothing and chemical-resistant gloves, respiratory protection and fall protection. Highlighting these safety requirements for all employees is essential. There should also be an additional level of safety in case of incident. For example, a fire extinguisher, first-aid kit, eyewash station filled with fresh water, and any additional safety equipment.
Who needs to be protected? Spray foam applicators and their assistants need PPE but who else? Basically, anyone that is in the vicinity, or will be entering the work area before the foam is cured. Confining the workplace with signs or tape until it is safe to re-enter without PPE will help protect those not wearing the required PPE from entering the work area.
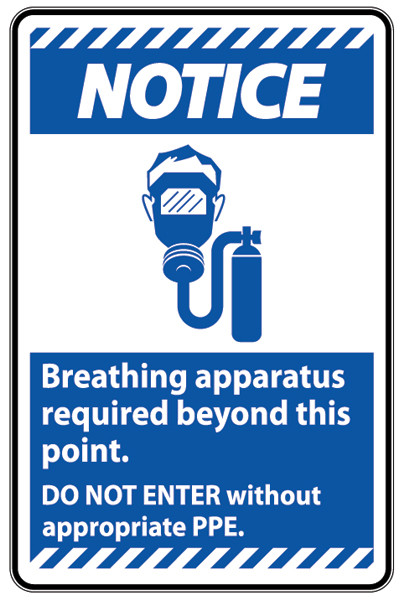
After spraying, when is it safe to enter the workplace without PPE? The manufacturer or supplier has specific guidance on their products which include recommended re-entry time, ventilation time, and re-occupy time.
Do not eat or drink near chemicals: Workers should not smoke, eat, or drink near any chemicals. This could result in potentially ingesting chemicals. Workers should always wash their hands before eating, drinking, and smoking should be banned from the area. If possible, provide workers with a portable foot-pedal-style hand-washing sink or disposable cleaning wipes if tap water is not accessible at the jobsite.
Cleaning equipment: The potential to have direct contact with MDI liquid (at room temperature) is possible. It is therefore still essential to wear PPE including:
- NIOSH-approved air purifying respirator with combination organic vapor / particulate (P100) cartridges, if handling heated SPF chemicals
- Safety shoes or boots
- MDI-resistant clothing like coveralls or an apron or
- MDI-resistant chemical gloves
- Chemical safety glasses or goggles
- Keep records of equipment maintenance including material names, system numbers, lot numbers, settings used and recurrent preparations.
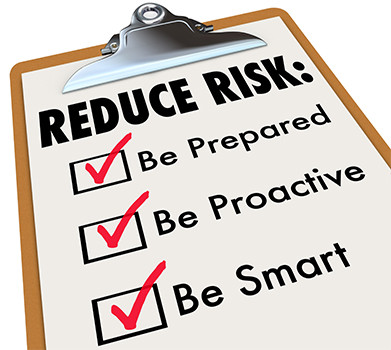
Once tanks are empty still wear PPE: Tanks and hoses will still be under pressure, therefore protective glasses or goggles, chemical resistant gloves, clothing that protects against dermal exposure and a certified respirator is recommended during this procedure. Remember, empty tanks could still contain potential vapor hazards.
In short, protecting skin, eyes, hands, and lungs is still essential when dealing with any pre and post chemical handling, equipment and or tank maintenance and cleaning up of the site where the work was completed.
Disqus website name not provided.