Spray Foam Shores Up Historical Gloucester Building
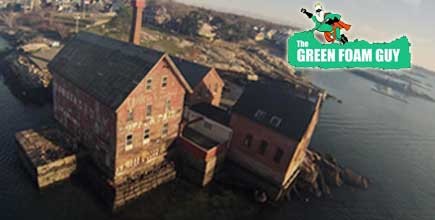
GLOUCESTER, MA – April 16, 2014 – The Gloucester Harbor, which is located in the Massachusetts-based town of the same name, is a vast and colorful staple for the fishing industry and summer vacationers. Aside from its popular wharfs or fishing boats entering the harbor, triumphantly bringing in fresh catch, the Gloucester Harbor is home to many historical buildings.
Among these buildings is the former Tarr and Wonson Paint Manufactory building, or simply The Paint Factory. This waterfront building was formerly used for the manufacturing of copper paint that was applied to the bottom of boats to protect against the buildup of barnacles. The building was abandoned sometime in the 80's. Years later, the building's exterior was briefly featured in the movie "The Perfect Storm." Over the years, the Paint Factory succumbed to leaks and floorboard damage, to the point that it became dangerous for tourists and town folk to visit.
Then, Dr. Ian Kerr, a renowned oceanographer, came into the picture with a mission for the Paint Factory: transforming it into an oceanographic institute. In order to bring the building into a new century, Dr. Kerr contracted The Green Foam Guy (GFG) to install spray polyurethane foam to improve the structural integrity to the building.
"The Paint Factory is an icon in Gloucester," said GFG's Keith Roberts. "Everybody knows it, and you can't miss it when you come out to the harbor. The fact that we were going to take part in restoring the building was both rewarding and exciting."
One of the major problems that the GFG crew noticed when they arrived on site was that there were sizable cracks between the floorboards, which left the building exposed. Roberts explained that there was a foundation wall around these cracks, but that didn't prevent wind from funneling into the building.
"The building was in pretty rough condition when we got there," said Roberts. "Water infiltration had rendered the floorboards weak, to the point that they could have given way at any time, so it was dangerous for people to walk around inside. Since the building was situated right on the mouth of the harbor, there was a significant wind factor. We knew we had to seal those open spaces before we did anything else so the building could perform better, and we knew spray foam was the best material to use to create an air and moisture barrier."
During the application, GFG crewmembers wore Tyvek suits, 3M 6300 Half-Face respirators, and gloves. They utilized Bayseal CC, a 2 lb. closed-cell spray foam made by Bayer MaterialScience, during the entire project.
Then, the crew applied six inches of foam to the wooden substrate of the underside of the floor to seal off all the open spaces. Roberts noted that his crew was standing on rusted crushed paint cans as they applied the foam, a snippet of nostalgia that was the only remnant of the Paint Factory's past life.
"Applying spray foam to the underside of the floor didn't only tighten up the building from air and moisture infiltration, but it stiffened up the floor," said Roberts. "It solidified the floorboards, making it safe to walk around the first floor once again. After the SPF application, the floor felt like it was made out of concrete."
The second phase of the SPF application entailed the installation of SPF to the exterior walls of the second floor. These walls had been previously gutted specifically for the spray foam application, whereas the walls of the first floor had been left untouched. According to Roberts, the walls of the first floor had a double-wall, which meant significant prep work to take down the double-layered plaster. This was a project that the institute's strict budget would not permit for the time being, so there was no foam installed on the first floor.
The crew applied three inches of foam to the exterior walls of the second floor. In addition to the exterior walls, the GFG crew applied a one-inch lift of spray foam to the underside of the roof, which had been fitted with foam board, in order to keep the seams sealed. Overall, the crew installed three sets of foam throughout the project, totalling a spray area of 13,200 board feet.
GFG's rig was equipped with a GlasCraft MH II proportioner and a GlasCraft P2 Probler spray gun. Working around the tide and the New England cold, the crew completed the project in a week. Upon completion of the job, Roberts mentioned that the wind infiltration subsided and that the building consistently retained heat.
Roberts and his crew were left with a feeling of fulfillment, having taken part in Dr. Kerr's vision, which was on the final stages of coming to fruition.
"He deserves to be commended," said Roberts. "We helped out and gave him a good start in patching up the Paint Factory, but it is he who rallied the people of Gloucester together in order to restore this historical building and occupy it for a good cause, all the while knowing how much work it would take to accomplish that feat."
A few months after the application, Dr. Kerr's dream was realized, as the site of the formerly abandoned and run-down Paint Factory hosted a ribbon-cutting ceremony that proclaimed the building as the new headquarters of Ocean Alliance, an institute dedicated to the study and preservation of whales.
About The Green Foam Guy: The Green Foam Guy is based in Rockport, Massachusetts and services the state of Massachusetts with quality spray polyurethane foam applications. Their reference list ranges from residences sprayed with open-cell foam to ship holds sprayed with closed-cell foam, marinas to multi-condominium complexes. For more information, please use the contact information and links provided below.
*Photos courtesy of Dr. Ian Kerr, Ocean Alliance.
Disqus website name not provided.