Spraying Profitably in Cold Weather
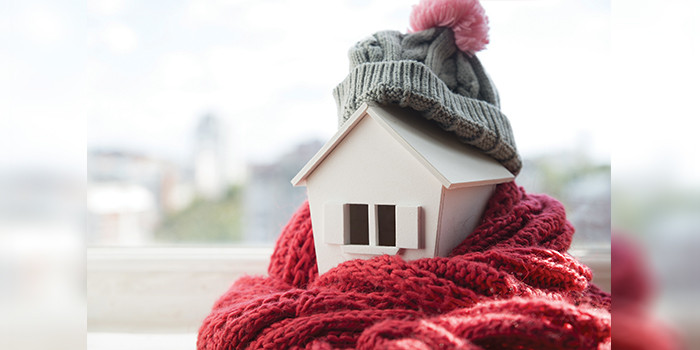
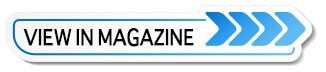
Spray Foam Magazine – Show Issue 2022 – Temperature, pressure and cleanliness are arguably the most important factors in producing great foam. We have some very reliable equipment available today able to keep pressures balanced and chemical temperature more consistent than in the past, and those who keep their A and B-sides clean can spray nice foam under most conditions. Winter, however, is not our friend! Spraying good foam when it’s cold is a challenge, but with some additional steps, it can be done.
There are some serious choices to make before accepting the job and sending a crew to the jobsite. The first decision is whether to even sell the job. If you have experience spraying in cold weather and you’re well prepared for it, and if you’ve charged enough to spray profitably, knowing your cost could be substantially higher. You can spray good foam regardless of the temperature outside and still make money. If you have any doubts, you might consider the following:
- Postpone until the weather warms
- Buy winter-blend foam for the project
- Move the building to a different climate zone (don’t laugh, we’ll explain)
- Heat the drums, heat the hose, heat the house and heat the crew
Most contractors have done projects they wish they had never agreed to. The job might have been contracted at a margin high enough to be profitable under different conditions, but cold weather problems create call-backs and rework, both of which are profit killers! The best thing you might do for your bottom line is turn down a project that’s likely to be problematic. Let your competition struggle with it while you pull maintenance on your rig and have it running smoothly when the weather breaks.
If it's below about 50°F you’re better off to spray a winter blend of closed-cell foam. Winter foam costs more to produce and will therefore affect your margin, but it might be the only change needed when it’s still chilly but not really cold. Using a proven winter formula is important to reduce processing problems and avoid call-backs due to shrinking, cracking and delamination. SES Foam’s NexSeal Winter was tested over an entire winter season in Fairbanks, Alaska and is certified as “Arctic Tested, Alaska Tough!” SES could have just sprayed and tested in a cold chamber, but real-world experience is better than simulations.
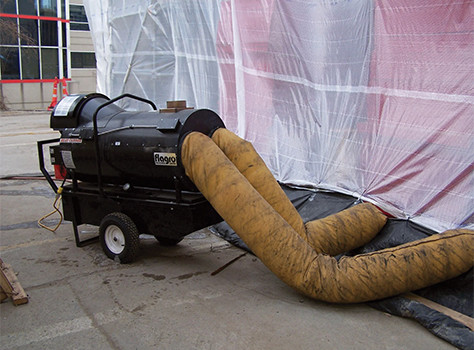
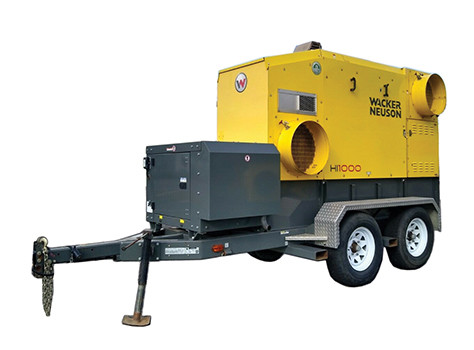
If you’re determined to spray the job and it’s very cold out, you can effectively “move the job to a warmer climate.” Regardless of where you live and work, it gets too cold to spray the way you’re accustomed to at least occasionally. You might live in DOE Climate Zone-4, but your area got a polar river dropping the temperature far below normal. Or you might live in Climate Zone-6, 7 or even 8 and you still need to work through the winter. If you add enough heat for long enough to saturate the substrate, it will be as if you’re spraying in a lower climate zone. It takes a while, but you can create Zone-4 ambient conditions when it’s ridiculously cold outside.
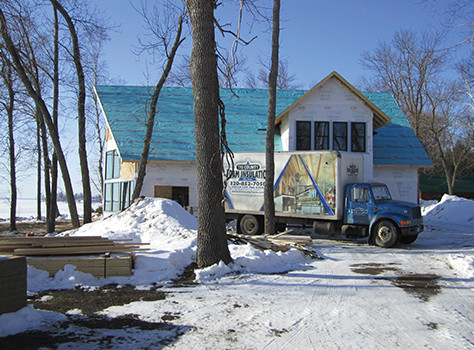
Adding heat must start in advance of your rig showing up on the job, and could cost several hundred dollars, depending on how it’s done. It must also be done correctly to avoid complications. An indirect-fired heater is essential. The flue must not be vented into the building since one of the products of combustion is water vapor for both propane and kerosene. There’s also carbon monoxide produced in combustion and as the building is tightened by the foam, the exhaust gasses could become dangerous for the crew and others who enter even hours after the foam is sprayed and heat is removed.
Indirect-fired heaters can be rented in many markets, but this is such an important piece of equipment, most contractors should own one or more so they’re ready for plummeting temperatures. These heaters come in many sizes, and this is a case where bigger is better. A 390,000 BTU/Hr capacity indirect-fired heater costs $4500 - $5000 new. While researching for this article I noted several trailer-mount indirect heaters on eBay and elsewhere that could be towed to the job the day before spray foam to thoroughly heat the space and structure.
There’s a notable exception to heating structures so foam will stick and stay stuck. Metal buildings in very cold weather are sometimes impossible to adequately heat due to the high thermal conductivity of steel. In severe climates, contractors sometimes tarp the outside of steel buildings then heat the air between the tarp and the steel to raise the inner surface temperature high enough to spray foam. Try heating and spraying small sections at a time to make sure the foam is processing well. It’s also critical to the application to keep heat applied to the outside until the foam is fully cured then gradually reduce the temperature so as not to shock-cool the metal and foam. This method works but is often painfully slow and unforgiving if the outside doesn’t get enough heat to penetrate, or the metal is cooled too fast or too soon.
SPF contractors know that Spray foam is the most effective insulation and air seal on the planet! Using foam to keep our chemicals warm before and during processing only makes sense. First, insulate a storage room for your drums. This could be a foam-insulated shipping container, or a foamed storage room in your shop. Keeping your drums warm in winter and cool in the summer is arguably the most important thing you can do to enhance profitability.
Keep your rig warm too. Many contractors in the north pull their rigs into heated shops at night and everything works better. The chemical is easier to keep warm if it’s left onboard, and your expensive foam equipment is easier to get going in the morning and lasts longer. Heating the inside of the rig is the next best thing, and again, works best when the rig is well insulated, especially the floor. We pull chemical from the bottom of the drum so providing a low-watt-density heat source under the drum then insulating the underside of the floor is extremely important.
Once on the jobsite, savvy contractors will support their hose on pads of foam, so it doesn’t lie directly on the ground, snow or in puddles of water. Scraps from prior jobs or piers of foam sprayed while the proportioner, hose and gun are being set-up in the morning will more than pay for itself by keeping the crew more efficient throughout the day.
Properly functioning hose heat is imperative. Many contractors struggle to keep the delicate hose heat components intact and working. The fluid temperature sensor and the connections at each section of hose must be protected. The hose can’t be dragged around, and the hose heat expected to work long-term.
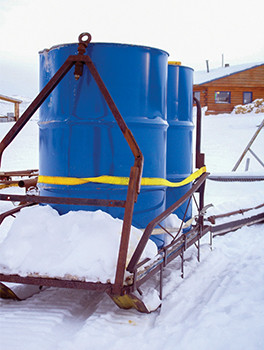
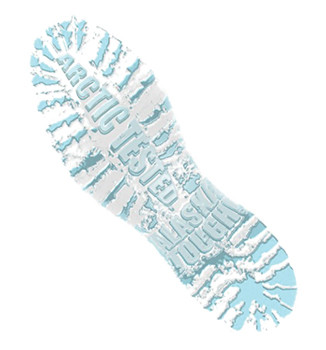
Taking a few extra minutes to roll the hose into the house or building then lifting the hose to move it will pay big dividends by reducing repair and maintenance time and parts cost. If the hose heat is ever put in “Amp Mode'' due to failure of the automatic hose heat control it will provide heat continuously until it’s repaired. This means too little or too much heat in the hose, and both are bad for the chemical. If continuous heat is applied in the hose while the trigger is not being pulled, the chemical can overheat, causing trouble at the gun or on the wall.
Heat is our friend. Heat the drums so the chemical is ready to spray in the morning and throughout the day. Heat the substrate to an acceptable temperature without adding moisture to the room. Heat the rig to keep everything moving. Heat your crew to keep them agile, safe and efficient. Use a high-quality winter formula and charge enough to offset the cost of the chemical and diesel needed to do the job properly.
*Spray Foam Magazine does not take editorial positions on promotional or sponsored; individual contributions to the magazine express the opinions of discrete authors unless explicitly labeled or otherwise stated. The inclusion of a particular piece in the magazine does not mean that individual staff members or editors concur with the editorial positions represented therein.
Disqus website name not provided.