Aging Industrial Park Rescued By Spray Foam Insulation and Polyurea Coating
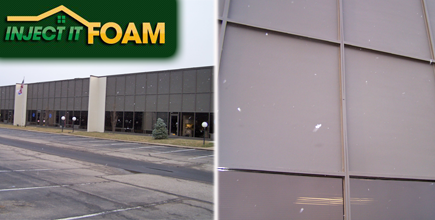
LOUISVILLE, KY – March 4, 2013 – What better way to determine the integrity of your product than to test it out on your own business? A 1970s-era complex called Blue Grass Industrial Park, was suffering from continued water issues due to lack of weather sealing around the façade windows in their office buildings. There were also areas in the back of the buildings that did not have insulation, causing heat to escape. Green-Tech Industries LLC, whose companies include Inject-It Foam and Diamond Tuff Coatings, was one of the businesses located in the industrial park. Green-Tech decided to apply polyurea and spray foam to their own building to see if it would successfully alleviate the problems and be an option for the rest of the complex.
According to Kathy DeGraaff, CEO of Inject-It Foam, there are nearly 400 businesses located at Blue Grass Industrial Park. Along with Green-Tech, the complex houses such businesses as an eyeglass frame manufacturer and a teamster’s union.
The building where Green-Tech is located is two stories high. The first floor façade consists mostly of windows framed with aluminum panels. Over the years, the aluminum began to shrink and oxidize, causing deterioration. As a result, water was entering the building through the window’s aluminum upright frames. Another concern was lack of insulation in the building’s rear exterior walls. Since there was nothing to prevent heat from escaping the structure, businesses were seeing a rise in their heating costs.
“If it rained hard enough and there was wind,” said DeGraaff, “it would literally blow in around the windows.”
One of the options the property owner had considered was to replace all of the failing aluminum panels on the building, but that would have been very costly.
Green-Tech had another idea. They decided to test a polyurea application on their own building in an effort to solve the water problem. Since Inject-It Foam also applies spray foam, they decided to install SPF insulation to the aluminum panels in the back of the building.
Diamond Tuff, Green-Tech’s coatings division, was called in to conduct the polyurea application. Before they could get started, crewmembers had to protect the windows on the building’s façade from overspray. They lined about an eighth of an inch of tape around each aluminum window frame.
Although they started off using plastic to protect the glass, they soon began coating the windows with wax instead. The wax was applied similarly to the way one would rub wax on a car (the company has also tried using soap for this purpose, but found it more difficult to remove).
“When overspray gets on the wax, it comes right off,” said DeGraaff. “You rub the glass down afterwards and get a nice, clean, shiny window.”
Crewmembers then applied VersaFlex polyurea to the outer frames of the façade windows at a 50-mil thickness, creating what would prove to be an adequate sealant to prevent water from permeating the structure.
Workers needed a 14-ft. boom lift to reach some of the higher areas of the building. Since overspray was a concern due to vehicles in the parking lot, the company had an upholsterer sew a canvas tarp to fit over an 8-ft. frame on the lift, fully enclosing it to prevent overspray. Some of the vehicles in close proximity during application were covered with tarps for added protection. The crew wore safety harnesses and full-face masks at all times while working in the lift.
To insulate the aluminum panels at the rear of the building, Green-Tech’s Inject-It Foam division applied Dow Styrofoam RS 2030 2.5 pcf closed-cell spray foam from the interior of the building at a nominal two inches to help stop heat loss.
Once the project was complete, the results indicated that Green-Tech’s applications were successful, so the company proposed conducting the same applications for the rest of the buildings in the industrial park.
“Once we started spraying and found we no longer had water issues, I told the property manager we could fix the problem for all of their buildings at about a quarter of the cost of replacing the panels,” said DeGraaff.
Upon the property owner’s approval, Green-Tech began the first phase of the large project in August of 2012. Up to ten crewmembers used two rigs with Graco Reactors H-XP2 to conduct the application. Since polyurea could not be sprayed when there was a lot of moisture present, or if there was frost on the substrate, the crew’s progress was often bound by the weather. The total spray area of the building fronts was over a quarter million square feet.
According to DeGraaff, the property owners are very pleased with the results of the polyurea and spray foam applications. Green-Tech’s work has saved them a considerable amount of money and has resolved the water and heating problems that were plaguing their buildings and frustrating their tenants.
Green-Tech is slated to work on a project at Quantum Center, a new center located at the same industrial park, this spring.
About Green-Tech Industries LLC: Green-Tech is a Kentucky-based residential and commercial company that has earned a reputation as one of the BBB's Accredited Premiere Contractors. The company specializes in injection foam and spray foam insulation as well as polyurea and poly blended coatings. The company’s businesses include Inject-It Foam™ and Diamond Tuff Coatings™. For more information about Inject-It Foam and Green-Tech, please use the contact details and links provided below.
Disqus website name not provided.