Arch Support
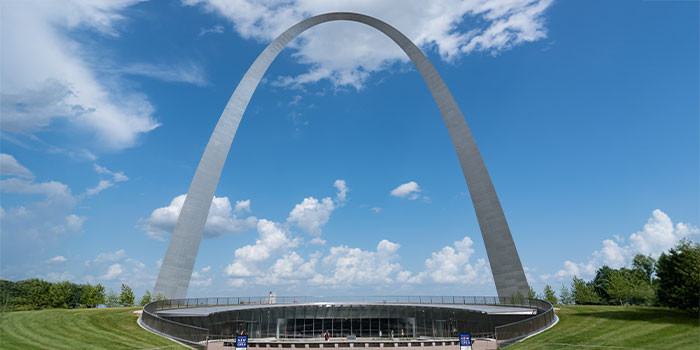
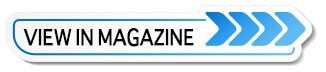
Spray Foam Magazine – Winter Issue 2024 – The following projects are a tale of modern engineering meets timeless craftsmanship and a testament to the dedication of preserving the nation’s architectural heritage. Spray Foam Magazine spoke with Marcus Tao, one of the owners of St. Louis, Missouri’s STL Polyjack, LLC to learn about their recent geotechnical work on two historical sites in the state.
Educated as a mechanical engineer, Marcus Tao spent 20 years working in building systems before sidestepping into general construction, which included commercial spray foam roof insulation. As time passed, Marcus identified a greater need in the area for groundwork and geotechnical foam. He met Wayne Ho, his now business partner, when Wayne was a client of Marcus. Wayne had a supply and distribution business and Marcus built him his distribution center. When the market was down, Marcus went back to engineering and then one day he got a call from Wayne asking if he would like to start a business in geotechnical foam. Marcus loved the idea of working in soil stabilization and the fact that he could utilize some of his spray foam equipment while working with geotechnical foam. STL Polyjack has been in business now for seven years and employs 20 people.
Gateway Arch Project
The Gateway Arch is a 630-ft-tall monument in St. Louis, Missouri. The steel form is one of the world’s tallest arches and Missouri’s tallest structure. Initially designed in 1947 and built from 1963 to 1965, the Gateway Arch’s immediate surroundings were redesigned in 2018. At the base of the monument are 10x10-ft. concrete slabs which continuously need maintenance due to the considerable amount of foot traffic visiting the monument each year.
STL Polyjack works directly with the grounds manager of the National Park Service who is responsible for maintaining the Gateway Arch and its surrounding area. The crew methodically stabilized the sidewalk slabs throughout the Gateway Arch’s National Park’s 91 acres, lifting between five to ten concrete slabs over roughly 1,500 sq. ft.
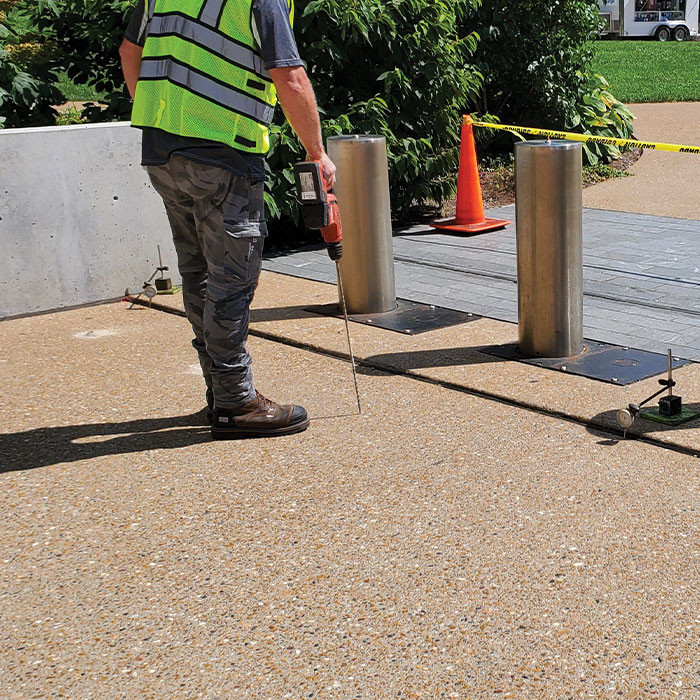
The STL Polyjack crew arrived with their PMC PH-2 fitted rig and began by drilling 3/8" diameter holes in the concrete.
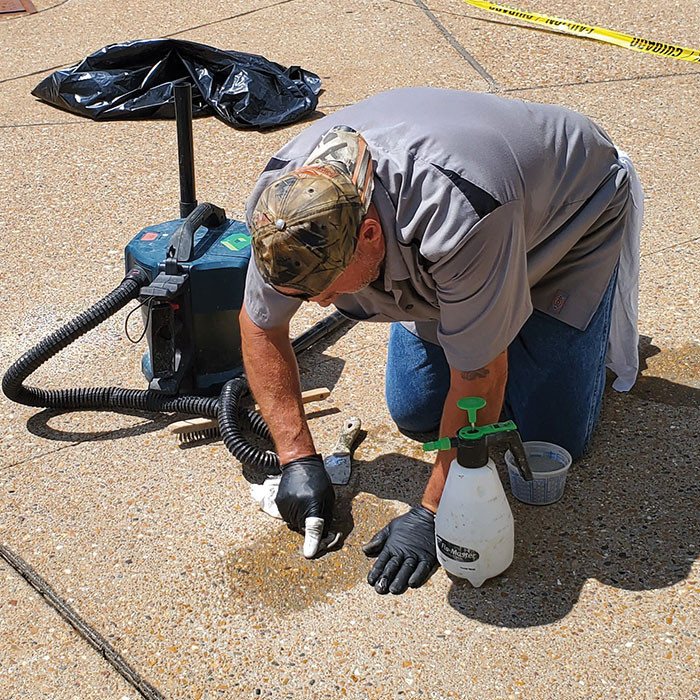
They applied a special liquid solution to prevent SPF from bonding to the surface
For this particular repair job, the STL Polyjack crew arrived on site in one of their six custom rigs featuring a PMC PH-2 proportioner. The four-person crew began by blocking off the area from the public. “This is a very busy area, but the public are usually respectful and often interested in what we are doing. However, we always make sure they don’t get too close in case of any overspray. We always have one injector, one person watching the pumps, and a couple of extra hands on these public projects,” said Marcus.
Pulling their 210-ft. hose from the rig, the crew got to work. To prepare the area, they applied a special liquid solution to prevent the polyurethane from bonding to the surface. They began by drilling 3/8-in. diameter holes in the concrete at strategic points to lift the slab to the desired level. Next, the crew carefully monitored the circulation, temperature, and pressure of the proportioner pumps to ensure the material was flowing correctly. Since the material is sensitive, it’s crucial that all factors work in harmony to achieve the proper cure curve and desired lift. Before proceeding, they performed a test burst of material to check its balance, ensuring the foam wasn’t too soft or porous.
The crew used Prime Resins Precision Lift 4.0# lifting foam injected with one of their Equalizer guns. They said that they love this liquid purging gun because of its ability to cleanly clear out the injection ports and manage back pressure when injecting the foam to lift the slabs.
Using quality polyurethane foam to stabilize and lift the commercial slabs back to their original position resulted in filling the voids, stabilizing the soil and closing cracks and gaps in the slabs. Polyurethane foam materials cure in minutes upon injection, which was important at this iconic arch to minimize downtime and allow the area to be completely available in just a few minutes, minimizing the disruption of traffic flow.
St. Louis Art Museum Project
The Grand Entrance Hall of the St. Louis Art Museum has been there since 1910, and under the hall’s 100-year-old marble tiles, there were voids varying from two inches to six inches. With the additional weight of the exhibits on top of the two inch tiles, roughly five tons across the exhibit floor, the floor started to sag and the situation became urgent.
Shannon & Wilson, one of the most respected geotechnical engineering firms in the U.S., had completed a thorough investigation using ground penetrating radar (GPR), which revealed the alarming voids beneath the 3,000 sq. ft. area at the heart of the grand hall. It was evident that the cracks and sagging were caused by settling soil beneath its surface and needed to be fixed.
The St. Louis Art Museum recognized the work that STL Polyjack had completed for the several historic projects in the area, including the Gateway Arch. Their general contractor liked what he saw on their website about their geotechnical foaming process, so he contacted them regarding the museum.
“They called us saying they did not trust anyone else with the project, and they needed to stabilize the floor without removing the delicate marble tiles, some of which were original to the building's construction. They told us just before we started that ‘there was no room for failure as they only had five spare tiles,” confirmed Marcus.
Originally the museum was going to remove all of the tiles, but they found out the quarry where the original tiles had come from a century ago had closed. Knowing that removing and replacing the tiles was no longer an option, they had to work with what they had. The crew’s state-of-the-art technology, including their laser-guided precision and electronic line-levels, helped monitor every millimeter of the lifting process, ensuring absolute accuracy. After two weeks of planning, the STL Polyjack crew used their borescope to scan the space under the tiles which varied between 2,000 sq. ft. to 4,000 sq. ft. per area. With every hole they drilled, they utilized the borescope to identify the exact location of each void. This was a lengthy process, but with this due diligence, they knew their success rate of saving the tiles would be increased.
Once the museum was closed for the day, the seven crew members of two leaders and five hands arrived on-site ready to work through the night. With lots of museum officials and security there, the crew was under immense pressure to perform.
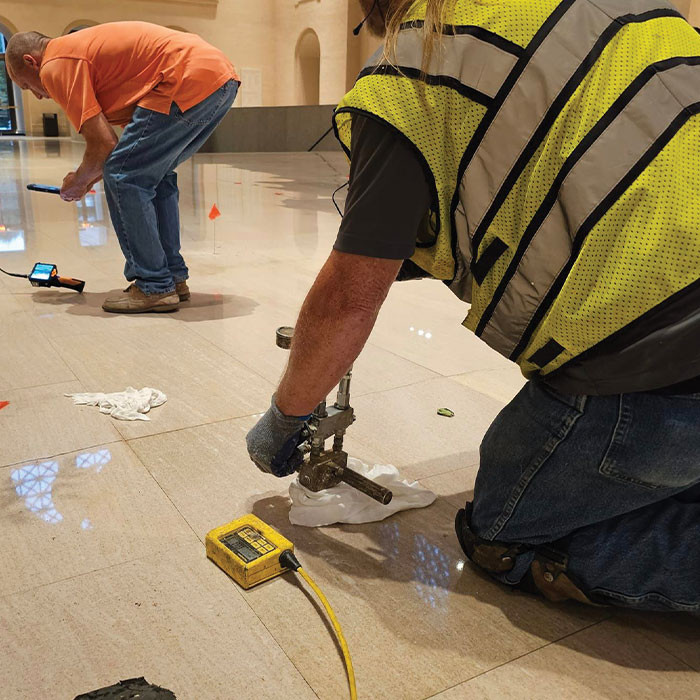
Using a borescope, STL Polyjack located the voids beneath the tiles. Using the pump and wait method, STL Polyjack carefully injected the foam very slowly.
Marcus explained the scene, “Arriving at the museum with two of our rigs fitted with PMC PH-2 Proportioner Pumps and Prime Resins Equalizer Guns, we were aware that there were exhibits surpassing $100 million and some weighing up to two tons, so we placed blankets under the hoses and tarps surrounding the exhibits. We had to be careful not to knock into any of the artifacts as we pulled our 210 ft. hose into the grand hall.”
The STL Polyjack crew had never drilled through marble before, so they proceeded very slowly with 300 injection holes. As they strategically drilled and meticulously scoped, the team knew they were embarking on a precision operation. Using their digital line level, they could see every time they injected Terrathane 4lb lifting foam from NCFI Geotechnical. With one of their Prime Resins Equalizer guns, they injected the foam using a pump and wait method, carefully ensuring each tile did not crack. As they injected beneath the marble tiles and through the mud slab, they checked that no material seeped into the delicate grout layer that could jeopardize the integrity of the tiles.
There were also release holes where the foam would travel under the floor and come out. Once the crew had that feedback of positive pressure, they knew the voids were being filled. Using the borescope, zip level, and the pump and wait technique, they only cracked one out of the 2,000 tiles.
In addition to making sure the tiles did not crack, the crew had to be aware of the museum’s tunnels, which run directly underneath the grand hall. “It was like the catacombs, and we had to hunch over as we walked through. There’s even a fountain down there. We had to be so careful when injecting the foam as there was an original drain that led down to the tunnels with a utility line. So, every so often, we had to send one of the crew down there to ensure no excess foam was going in there,” said Marcus.
The actual work took eight nights to complete, however from start to finish, the entire project took one year. The crew used six sets of foam to fully stabilize the grand hallway to prevent further settlement and preserve the marble floors. The museum was elated, as the crew exceeded their expectations.
This project is a true representation of the skills and research the STL Polyjack crew applied, the quality of the geotechnical foam installed, the superiority of equipment, and the determination to preserve a historical treasure.
Disqus website name not provided.