Are You Ready for a Big Change?
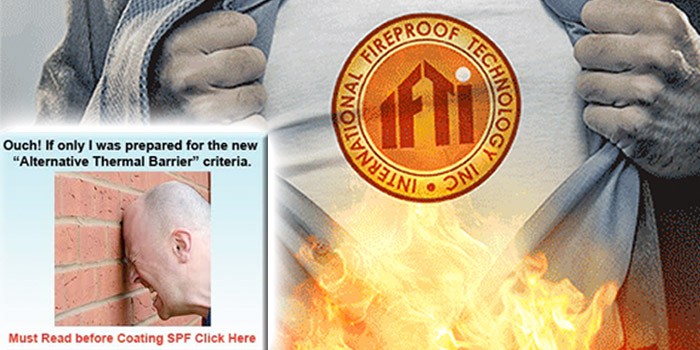
IRVINE, CA – January 3, 2016 – After a series of tests and hearings, explorations, and even exhaustive fire testing, ICC-ES unanimously voted to implement AC456 and modify AC377, the code that establishes the requirements for spray-applied polyurethane foam plastic insulation. The new ICC-ES code, AC456, which will be effective in 2017, establishes a criteria for Coatings over SPF ensuring that the product tested is the same product that is used on the jobsite. As we move forward, all assembly testing that the SPF and the Coating, that has not been performed in accordance with AC85 Section 3.1 will be removed from ALL SPF evaluation reports and will leave you, the contractor, potentially liable for a “Bad Install that does not meet the codes“.
- There is only one way to know the coating you are using and the assembly you are protecting meets AC456. Ask your coating supplier to provide you with an evaluation report on their coating, clearly stating that the coating meets the requirements of AC377 and AC456. Having an Evaluation Report stating AC456 compliance is NOT AN OPTION it is a requirement. Do not be confused by Evaluation Reports of coating companies that DO NOT clearly state AC456 criteria has been met.
- Insist that the coating companies Evaluation Report clearly list ALL SPF BRANDS OR ASSEMBLIES, and that at the time of testing met the AC377, AC456 Compliance Criteria.
- NOTE: Another option is to supply your code official with an SPF Manufacture Evaluation Report or IAS certified full scale test, clearly listing your coating of choice as a tested Alternative Thermal Barrier solution. Make sure the coating company supplies you with a signed letter from the accredited testing facility where the assembledCOATING COMPANY SUPPLIES YOU WITH A SIGNED LETTER FROM THE ACCREDITED TESTING FACILITY WHERE THE ASSEMBLY WAS TESTED, STATING THAT AT THE TIME OF TESTING THE COATING MET AC456.
Please do not hesitate to contact IFTI DC315 regarding this new Acceptance Criteria. IFTI has hired additional staff to assist, educate, and train you on the new criteria, offer you all the documentation needed and make a seamless transition to the next level of code compliance.
For the full story see the following Article published by Juan Sagarbarria of Spray Foam Magazine.
Reducing Liability Through Compliance
Applying the right code compliant thermal barrier coating reduces fire hazards and job burdens.
By Juan SagarbarriaSpray foam insulation is a highly effective insulation material, however it is also known to be combustible without careful adherence to fire codes. as a foam system manufacturer or an installer, no good deed goes unpunished. You better be sure the foam is properly protected so as not to cause a potential fire hazard to the home or building in which it is installed.
Thankfully, members of the SPF industry heeded the lessons of the past pertaining to fire safety and as the SPF market grew, manufacturers and contractors utilized thermal barriers in conjunction with SPF insulation. They also kept a close watch on fire codes and regulations as they too evolved and became stricter. Make no mistake: The SPF materials are highly tested and regulated and installing it is a profitable business, however there are significant liability issues of concern when code compliance is in doubt. Choosing and using a thermal barrier has previously been one of these issues.
It’s not just about applying any thermal barrier solution that mitigates liability while on the job. It’s about choosing the right one that helps all parts of the SPF industry stay ahead of the game. As of late, that exemplary thermal barrier is none other than DC315, an intumescent thermal barrier coating formulated by International Fireproof Technology, Inc. (IFTI). After developing their DC315 to pass UL1715 and NFPA 286 room corner burn tests, IFTI engaged third party Quality Assurance provider, Intertek, to put in place a program to ensure the DC315 is inspected, validated and audited for manufacturing consistency and performance since its first test in 2009. Since then, DC315 went on to pass over 200 full-scale fire tests over spray polyurethane foam worldwide- Including ISO standard 9705, one of the most extreme full scale room tests in the industry and is currently the ONLY intumescent to have passed this testing over SPF. DC315 is now arguably the most tested industry leading intumescent coating available to the SPF industry.
“SPF has come light years over the last decade in reducing flame spread and smoke,” says Gary Wolfe, IFTI’s Executive Vice President. “All SPF sold and under an evaluation report pass testing to validate this. In high fire situations, the SPF is still vulnerable to an intense fire. Coatings like DC 315 are tested to stringent room corner burns offering protection and reducing liability.”
But IFTI did not stop there when trying to make the industry safer. They personally spearheaded the adoption of AC456 by the ICC-ES, raising the bar a notch higher for fire safety and code compliance across the board. A code by which later on this year, everyone in the SPF industry will be required to abide.
STICK TO THE CODE
AC456 was added to AC377 and republished in April of 2016, which is the existing code criteria that establishes the requirements of spray-applied polyurethane foam plastic insulation. It is no longer a strongly suggested movement for fire safety. AC456 has been implemented as a new ICC-ES code criteria and compliance is mandatory. AC456 establishes unprecedented criteria for intumescent coatings applied over SPF, ensuring that the product tested is the same product that is used on the jobsite. Come October 2017, all testing that has not been performed in accordance with AC85 Section 3.1 will be required to be removed from every single SPF evaluation report.
As you probably know, DC315 is fully AC456-compliant to be installed over the majority foams on the market today and a report is readily available for each. Point in fact: DC315 has a Code Compliance Research Report (CCRR) that lists AC456-compliance across multiple testing (with specific spray foam systems as assemblies), listing, and evaluation services.
According to Wolfe, “many Authority’s Having Jurisdiction (AHJ’s) and Code Officials are demanding AC456 evaluation reports today. Clearly, AHJ’s have NO TIMELINE for life safety”. SPF contractors should not wait or risk losing jobs, by not having an Evaluation Report confirming your coatings compliance to the new codes. “The proof is in the testing,” states Wolfe. “The simple way to ensure compliance is to be able to produce an Evaluation Report saying that you are, so contractors need to demand an Evaluation Report for AC456 compliance from the coating company. IFTI authored and led the charge to ICC-ES to develop AC 456, and have set the highest standards of manufacturing and testing in the industry.”LIABILITY MINIMIZED, FASTER APPROVAL
So, now that the SPF contractor knows that there’s a code to be aware of and that there’s a coating they can use that is backed to be 100 percent in compliance with that code, it would be a sensible decision to opt for that product on their next SPF insulation job.
This is a revolutionary step forward for the industry as compliance means reducing contractor liability and further positioning spray foam as the leading insulating material in the world by mitigating fire hazards.
“IFTI does not stop or settle at just ensuring code compliance. What we have done is not good enough.” Wolfe references IFTI’s mantra: “We believe our job starts – not ends – when we pass a test” when referring to their strenuous, exhaustive testing methods with DC315 with the ultimate goal of protecting SPF applicators and the industry as a whole.
“Think of this scenario: You used a coating – the correct coating – and you have an evaluation report and it meets AC456. Good, now a fire or a similar issue occurs, the evaluation report protects them,” articulates Wolfe. “But what if fire is not the issue? What if it’s something else; like a Code Official asking about lifespan, or a homeowner asking about VOC or toxicity? We have spent hundreds of thousands of dollars on impact and durability testing, 50-year performance life testing, VOC during and after curing, toxicity while burning, mold resistance, adhesion testing, humidity and condensation exposure and much, much more! Why all this additional testing? Simple, to protect the SPF industry stakeholders today and in the future.”
Another benefit of using a product such as DC315 is that it provides ease of approval for an SPF contractor vying for a specific job. The reason for that being, again, the thorough testing that leads to the satisfaction of AC456 requirements.
“No coating company in the industry has gone to the depths of testing and compliance that DC 315 has, and this is recognized by the AHJ’s,” says Wolfe. “In November alone we tested, and passed, more rooms than most of our competition have listed in total. We work with inspectors and fire marshals on industry education, supply literature, and data for meetings, and have in excess of a thousand certified applicators trained to apply our coating, not to just paint it!”
CONTACT INTERNATIONAL FIREPROOF TECHNOLOGY, INC.Direct any questions that you might have about AC456, IFTI’s CCRR Report, or liability in the SPF market to IFTI.
Phone: 949-975-8588
Website: www.painttoprotect.com
Disqus website name not provided.