Block-Solid Living
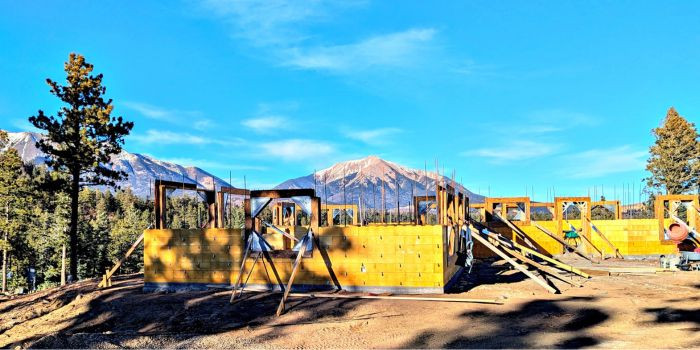
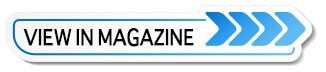
Spray Foam Magazine – Show Issue 2025 – Insulated Concrete Forms (ICF) are rapidly gaining traction among architects, builders, and homeowners, thanks to their unmatched benefits. Reflecting this growing trend, Spray Foam Magazine recently collaborated with ThermoBlock, LLC—a trailblazer in the ICF industry—to highlight two remarkable projects that showcase the transformative potential of their innovative ICF approach.
Established in 2005 in Phoenix, Arizona, ThermoBlock has grown into a leader in this construction space. With its primary manufacturing facility located in El Paso, Texas, the company now serves clients across the United States, Canada, and beyond. Boasting a portfolio of over 100 successful projects, ranging from residential to commercial structures, ThermoBlock has also taken part in vital government builds for the Department of the Interior in Arizona. Renowned for its innovation and reliability, ThermoBlock sets the standard for excellence in construction.
Currently, a Thermoblock crew is in the breathtaking Spanish Peaks region of southeastern Colorado, undertaking two awe-inspiring projects along the Highway of Legends. This area boasts stunning landscapes, from the majestic heights of the Sangre de Cristos and Spanish Peaks to the striking red rock formations of the Dakota Wall and the Devil’s Stairsteps. Situated at elevations of around 9,000 feet, these projects exemplify the beauty and challenge of building in harmony with nature.
Lovato Concrete is ThermoBlock’s local contractor on these projects, certified as an installer and distributor for future endeavors.
ICF offers numerous benefits, garnering admiration from contractors and architects alike. Its innovative methods improve construction efficiency, reduce storage requirements, minimize heavy machinery use, significantly cut waste, and shorten build times due to the speed of installation. With outstanding energy efficiency, superior R-value of R-38, resistance to thermal bridging, patented internal bracing system, and exceptional durability, ICF stands out as a choice that inspires builders and property owners to think big and build bigger.
ThermoBlock’s solid wall post and beam construction method suits a wide array of commercial and residential projects. This approach uniquely combines the advantages of closed-cell polyurethane insulation blocks with the robust strength of steel reinforced concrete. Unlike conventional ICF products, ThermoBlock’s installation process is straightforward, minimizing the cumbersome scaffolding and bracing often required. Its patented internal bracing system allows for easy assembly, ensuring a straight, strong wall structure that interlocks like Lego pieces. Vertical seams are notched and secured to form an impenetrable air barrier, while the steel reinforced concrete and steel studs provide stability.
The combination of concrete’s strength and the energy efficiency of closed-cell foam is revolutionizing the industry, driven by a growing need for resilience against natural disasters and a focus on energy conservation. ThermoBlock’s innovative design enhances protection against flooding, with its concrete layer ensuring water-resistant insulation. In cold climates, these structures retain and release heat energy, providing warmth even during power outages—making them an ideal solution for projects in Colorado.
ThermoBlock is also engineered to endure extreme events like hurricanes and seismic activity. In regions such as Puerto Rico and the Caribbean, the transformative impact of insulated concrete forms (ICFs) is evident. These quick-to-assemble, sustainable, and durable buildings are rising to meet the challenges posed by tropical storms and hurricanes, exemplifying modern advancements in construction technology.
The elevated nature of ThermoBlock’s recent projects underscores the ease of transporting ICF materials compared to traditional alternatives, making them a beacon of innovation in construction logistics. The projects are owned by two different, unrelated clients, and are approximately 35 miles apart with about 20 miles of dirt roads to traverse.
One of these projects, a residential build, was initiated by a certified installer. The building consists of a one bedroom with en suite bath, living room, kitchen, powder room, laundry room, a bonus room for grandkids bunkbeds, and a game room.
The other project is a hybrid residential/commercial structure and emerged through the vision of a ThermoBlock representative. It’s a unique space that will house an antique motorcycle restoration specialist and has a residential area, shop, parts, and showroom. Both projects were chosen for ICF construction by building owners inspired by ICF’s numerous advantages.
Diverse in their construction methodologies, these projects share a common inspiration: neither was originally intended to build with ICF. The residential project employs a structural "B" type slab on grade for its foundation, while the hybrid project utilizes a spread footing, demonstrating versatility and strength as ThermoBlock serves as the stem wall, merging below grade stem walls with above grade wall system that continues to roof bearing height. This ensures continuous insulation from footing to roof. ThermoBlock provides an exceptional R-38 thermal envelope with resilient concrete construction. When utilized in concert with SPF, the R-value is second to none. ThermoBlock was selected for these builds over other ICF products for its insulation value in eight inch wall systems vs. other products with thicker wall systems.
The projects commenced in early winter, a season when southeastern Colorado experiences cold temperatures and snowfall. Fortunately, the job site had not been significantly impacted by severe weather, allowing concrete pouring to proceed without major issues. However, true challenges lay in the site’s remoteness and its elevation of 9,000 feet, which limit access for concrete trucks and pumping vehicles. Therefore, transporting concrete to the site could be both complex and costly. But, despite these obstacles, ThermoBlock’s insulated forms provide reliable freeze protection during the curing process, minimizing the weather-related concerns.
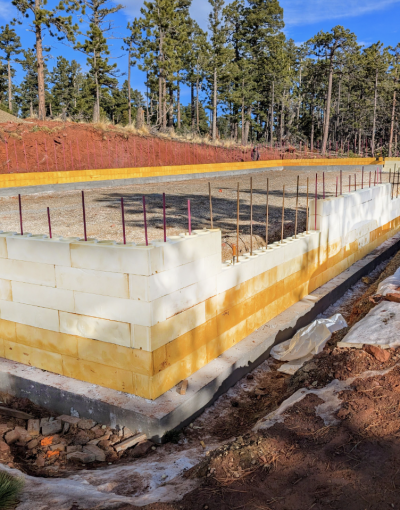
Utilizing block as a stem wall on spread footing of the hybrid use project.
Additionally, their post-and-beam system uses approximately 30% less concrete than typical infill ICF projects. As a result, fewer truck trips were necessary, offering the added benefit of improving scheduling efficiency.
“There are several types of ICF products offering different types of wall systems, from solid infill, waffle grid, and post and beam but ThermoBlock differs from other systems due to the use of closed-cell polyurethane pour foam to cast our block versus extruded polystyrene. We offer superior form strength, higher R-value than EPS, class one fire ratings, and most importantly, regional manufacturing opportunities, reducing the carbon footprint by minimizing shipping. Both projects are the lifelong dreams of high-profile clients and we are extremely honored to be selected as the ICF product for these projects.” stated James Estes, owner of ThermoBlock.
Spray Foam Magazine will reconnect with James and ThermoBlock in the spring of 2025 to share updates on the completion of these two projects. We’ll dive into the results and explore how ThermoBlock’s innovative methods contribute to building efficient, functional structures perfectly suited for embracing the Rocky Mountain Highlife.
Disqus website name not provided.