Cabins in the Snow
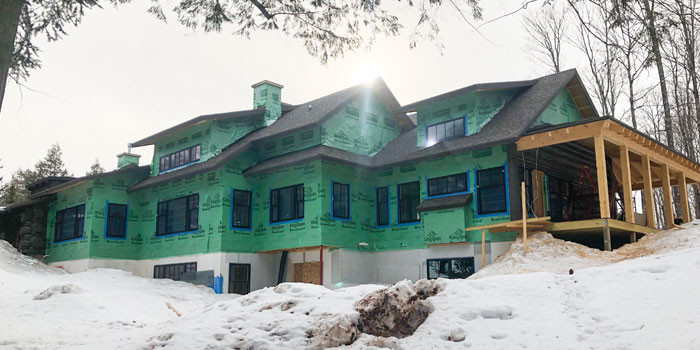
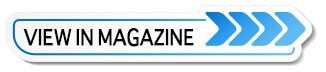
LATE SUMMER 2020 – Spray Foam Magazine – Eric Gladson is the owner and head sprayer of Integrity Plus Insulation LLC, based out of Northern Wisconsin. They service all of Northern Wisconsin and even travel to the Upper Peninsula of Michigan to complete projects. Gladson and a team of sprayers have worked on numerous cabins preparing them for the harsh winter months of the North by installing spray foam insulation. He recently worked on a couple of new cabin constructions: the Hanney Project in Manitowish Waters, WI and the White Project in Land O’Lakes, WI.
At the start of the first project, Gladson was by himself for a couple of weeks, until Payless Insulation’s Jeremy Lomax arrived with his two helpers and his foam rig to assist him. Other contributors included Ron Fetzer and the crew from Spray-All Spray Foam Insulation. Bill Bilben from Atticus Insulation and Joe Hinderks from Apex Insulation also were able to lend a week to help with the project—all brought together through the Facebook group, SFWW. These cabins were 30 minutes apart, so shuttling trailers, crews, and equipment back and forth wasn’t a huge undertaking. However, the crew was soon to discover there were other obstacles they would have to tackle.
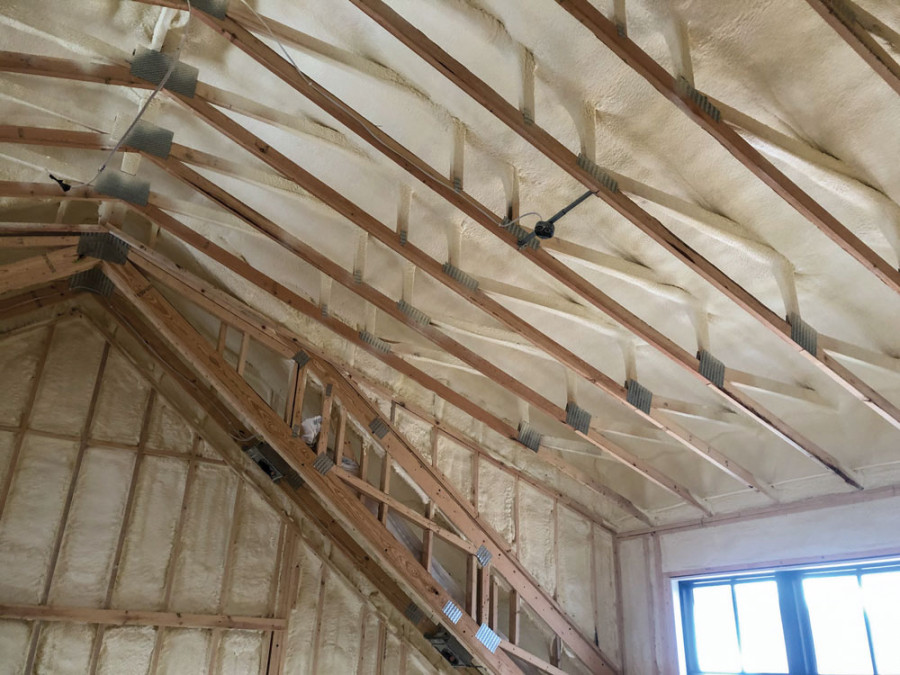
The White cabin project is completely off the grid, so it relies mainly on solar power. Foam was applied to all of the roof decks, walls and rim joists to seal the structure.
The Hanney Project
The Hanney cabin was specified by the architect who detailed the minimum R-38 (five and a half inches) for the ceilings, which was an increase from the energy model and initial bid of four inches. All the roof decks, which were cathedral ceilings, walls, basement walls, and rims were also sprayed. The main objective was to seal the building envelope to prevent unwanted moisture problems in both cabin projects. SPF was chosen for its extreme insulation abilities, added structural strength, and moisture control abilities. SPF was perfect for these cabins due to its high thermal insulating values, reducing radiant heat from entering the structure through the roof deck. It also has vapor migration reduction properties with its natural ability to seal all gaps and crevices.
Gladson had an energy model completed for the Hanney project to officially satisfy the code. Both cabins had Lapolla FL-2000-4G applied with the Hanney cabin having one to three inches on the walls and rims, over four inches on basement walls above grade and garage walls, two inches on basement walls below grade, five and a half inches for all ceilings/roof decks. Overall, the coverage was 2,890 square feet for the roof deck and 6,466 square feet of walls.
The foam was applied to Oriented Strand Board (OSB), concrete basement walls and cardboard vent chutes for all roof decks. There was no special coating applied as the foam was getting either drywall or tongue and groove paneling.
The owner of the cabin was from Milwaukee, WI, a four to five hour trip one-way, but he came up as often as he could. Gladson and his crew ran four Val-6 radiant heaters during the daytime to heat each area they were going to be spraying. The owner wasn’t comfortable with keeping the heaters running all night, so sometimes it was a short day of spraying by the time the crew got things warmed up enough. In the mornings it was often 15 degrees below zero with the wind chill and between firing up the heaters to warm up the house and plugging in the block heater on their generator for a couple of hours before starting, it was almost noon before they could begin to spray.
Another challenge the crew faced was the owner’s request to vent the whole roof. In the main roof section, there were several valleys that came together, so standard vent chutes in between each truss were not an option. Gladson had to use cardboard vent chutes for most of the roof system and install them five to six inches off of the roof deck to allow for cross ventilation of the roof deck. There were also a few skylights in the master suite and yoga room, which added to the challenge of correctly venting the entire roof deck.
Because it was so cold, heating up the concrete walls in the basement proved to be a challenge as well. One night the owner agreed to keep a few heaters going, checking on them often, to warm up the basement walls. This brought a ton of moisture out and completely flooded the basement, with the walls being soaked with moisture. Gladson recollects, “Thankfully, I had a large commercial dehumidifier on site along with a few large fans that we used to spot dry each wall section. After a couple of days, we were able to get the basement walls sprayed.”
A few weeks into the project the owner also decided that he wanted the remaining space in the ceiling system to be netted and blown with cellulose for some sound deadening and more R-value.
The White Project
This cabin was specified by code, Gladson recalls, “It was a large addition to a big cabin, located almost on the border of the Upper Peninsula of Michigan and Wisconsin. The house is completely off the grid and relies mainly on solar power, so the foam was more than the minimum needed.” The crew sprayed all of the roof decks, walls and rim joists, along with a couple of small cantilever floor sections.
The basement walls were a composite wall system that came already insulated. They sprayed four inches on the walls and rims and seven inches on the roof decks. There was 2,750 square feet of roof deck and 3,081 square feet of walls sprayed with the crew using about eight and a half sets of foam. There was 4,720 square feet of living space in the addition, bringing the total living space to 6,704 square feet. Like the Hanney cabin, the White project also sprayed to OSB for both walls and roof decks. Gladson’s rig has a Graco R2 E-30 with an Akurate Dynamics Deltalite hose and controller and CS gun. Jeremy Lomax from Payless Insulation runs a PMC PH2 with a PMC AP-2 Gun and Ron Fetzer from Spray-All Spray Foam Insulation runs a Graco R2 E-30 with a CS gun.
Getting to the job site was a challenge due to the icy road conditions, and that was just the start of the obstacles the crew had to deal with on this cabin project. The only power on site was from a generator because the cabin was powered by solar and the owners didn’t want any surges on their equipment from power tools. Keeping the foam trailer heated overnight was challenging for the crew. On one of the nights, Gladson kept warm by keeping his generator running.
The crew was aware that it was one of those typical SPF installs, where some things were not 100 percent ready to go, and with other materials in the way, the crew had to work around them so that they could reach their deadlines. The basement had in-floor heating and the main level was also having in-floor heating installed so there were tubes on the floor, then gypcrete over the tubes. The tubes were scheduled to be installed on a Wednesday, then the gypcrete on a Friday, which meant the crew had to have the entire main level walls and roof decking foamed and cleaned up before the day of install. Gladson states, “We finished that night at just after midnight, so it was ready for the crew to install tubes the next morning.”
The crew also ran into trouble heating this cabin, especially with no steady power overnight. To solve this issue, Jeremy Lomax from Payless Insulation brought up his Wacker Neuson indirect fire heater, which made heating up any spray areas a quick project, “The more we got foamed, the quicker it was to heat and hold heat,” states Gladson.
Yet another roadblock for both of these cabin projects was the fiberglass batting for sound. Both customers wanted R-30 in all the floors and R-13 in all the interior walls for sound absorption. This is something Gladson had subbed out to another local insulator he works with on combo projects like these. He was fully expecting him to do all of the batting for him on both projects. However, the contractor shut down his company and moved.
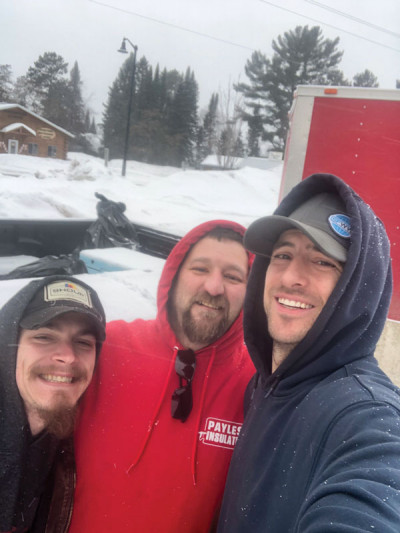
(From Right to Left) Eric Gladson, Jeremy Lomax, and one of Jeremy’s helpers, Dalton
“It pretty much left me high and dry for getting the batting work done. I’ve never done batting work before and don’t care to. Thankfully Lomax and his two workers, Dalton and Brandon and then Bilben and Hinderks, stepped up and handled all of the sound batting for both houses. The Spray Foam Brotherhood pulls together again to get this job done.”
The crew was also under pressure for road postings. In the winter, the frost drives into the ground where it isn’t insulated (roads, etc.) and in the springtime when it begins to warm up, the frost starts to come out of the ground which makes the road surface extremely soft. From mid-March until mid-May, counties and townships put weight limits on the roads to prevent damage from driving heavy vehicles on them. Most township roads are posted at five tons (10,000 pounds) and both of these projects were on town roads. Everything was warming up and limits were getting ready to be posted. The crew had to finish so the drywall could get delivered. Gladson states, “If it wasn’t for the guys that came and helped finish the cabins with me, it would’ve held up the entire building schedule for both projects.”
The customers were both happy with the finished results and now have long lasting, ultra-comfortable and energy efficient, high quality cabins they will be able to enjoy for many years to come. These cabin projects were the ultimate team effort, and it proves that when people come together in the spray foam industry, great things can and will happen.
Disqus website name not provided.