Cold Weather Spray Foam Applications
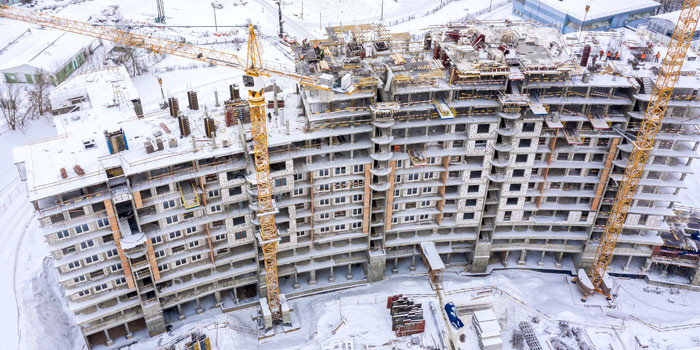
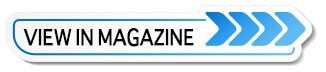
SPRAY FOAM MAGAZINE – Show Issue 2021 – The Spray Foam business is hard, and harsh winter weather makes it much harder. This is especially true in the far north, but even in mild and warm climates, a sudden drop in temperature can cause big problems that affect your bottom line.
Everything is more difficult in the winter; the logistics of getting your foam sets to your shop, warming and prepping your chemicals, getting the rig to the job, setting-up the jobsite, and prepping the substrate to spray. A savvy contractor will plan, prepare, and compensate for difficult winter conditions in order to keep the crews working as efficiently as possible. »
The most important changes needed to maintain profitability in the winter are:
- Order a few days in advance.
- Store material in a heated room.
- Warm the job structure starting the day before spraying.
- Heat your rigs.
Generally speaking, trucking companies do a pretty great job of getting our chemical from the factory or warehouse to your shop, but a weather event can stop or slow traffic making on-time delivery impossible. Weather delays might not be only in your region, trucks could be held-up hundreds of miles from you and there’s simply nothing you can do about it. Ordering a few days to a couple of weeks in advance can mean the difference in your jobs getting done and you getting paid or not.
Heat makes everything easier. Chemicals flow, foam sticks, yields remain acceptable and your crew will appreciate being warm. Store your sets in a warm room at your shop. This could be an insulated shipping container or a dedicated warm room in your warehouse. Spray foam in the walls and ceiling, and store your drums on pallets with fans to blow the heated air around and under your drums to get them warm and keep them warm. This can save hours on every job since the crew won’t have to warm the chemical enough to get it to spray. The primary heaters on your proportioner can only raise the fluid temperature so much and hose heat is less effective in the winter, so start with warm chemical every day. You’ll be glad you did and so will your crew.
One contractor in the Northwest built a 600 square foot warm room and installed a 1500-watt wall heater, which was enough to heat and maintain temperature for about 20 sets at a time. The cost to warm the room was about $75 per month. The heater didn’t actually run 24/7, but if it did the cost would only be about $108 / month (1KW x $0.10/KWH x 24 hours x 30 days = $108). The jobsite labor and opportunity cost saved by being able to roll the truck in, roll the hose out and start spraying is many times the small cost of heating the drums in advance.
Getting to the jobsite with heated chemical and a rig prepped and ready to spray solves half the winter challenge. The other half is heating the substrate you’re spraying. It’s important to apply heat without adding moisture to the building, which can condense and cause even more delays. This means you’ll need an indirect propane or diesel-fired heater. With an indirect heater, the heat of combustion is exchanged to the air in the building across a heat exchanger and the flue gas stays outside. The moisture in the flue gas does not go into the building so it can’t condense on your substrate. In some regions it’s necessary to use dehumidifiers in addition to heat to dry the framing members below 19% moisture content. Heating the building the day before spraying is often the only way to heat the substrate deeply enough to make the foam stick and so it doesn’t shrink or crack.
If you’re not familiar with indirect-fired heaters, ask your tech rep about them. Fast and thorough heating can make or break your profit on the job. Even if you had to spend $75 on fuel, operating in a warm environment and spraying warm surfaces can save hundreds or thousands of dollars and every dollar saved goes straight to your bottom line.
Similar to the warm room and heating the structure, keeping the rig warm pays big dividends. Mechanical equipment starts and runs better, chemical flows, and the crew members prepping the rig can move more quickly through their jobsite set-up checklist. Attitudes improve as well as your profit!
Beware of metal buildings in the winter. They can be nothing but trouble, especially for ocSPF. Metal does not allow any absorption into the substrate as OSB and plywood do. The small amount of absorption and attenuation common with wood substrates makes adhesion far more reliable than spraying on metal sheathing, and cold metal is the worst case for spray foam. One technique for spraying metal is to “prime” the sheathing with a thin coat of foam. Some call this a “flash coat”, and many manufacturers do not condone this practice. SES does recommend it with their foams so be sure to ask your SES tech rep for advice on how to do this effectively. Another necessary winter practice is to get closer with your spray gun and use a smaller tip.
If your foam is slow to react, sags on vertical surfaces or drips when sprayed overhead, then it’s too cold. You might have all the right settings on the proportioner, but it’s still too cold, probably due to lack of adequate hose heat. Make sure your hose is well insulated, especially around the Fluid Temperature Sensor (FTS) and lift your hose off the ground, when it’s cold, wet, or covered with snow. The hose can be supported by small bags of scrap foam or foam blocks made for this purpose. The hose will conduct heat to the ground or snow many times faster than to the air, so get it off the ground. Automatic hose heat control is very important. Yes, there is a by-pass method on most rigs to set specific amps if the FTS or sensor circuitry fails, but this is intended to be used only to get you through the day until you can repair the problem, not as a permanent operating procedure.
In the spectrum of polyurethane spray foam densities there are some sweet spots that have become industry standards. About ½ pound per cubic foot of open-cell foam is a sweet spot for low density, R-Value, yield and sprayability. Two-pounds per cubic foot density is the ideal closed-cell or medium-density foam based on R-Value, yield, sprayability and dimensional stability. Less than 2-pound closed-cell foams might have slightly higher yield, but they tend to lose dimensional stability in cold weather applications, and curiously don’t necessarily lose adhesion. This becomes a problem when the foam shrinks and cracks, but remains tenaciously adhered to the substrate, making it extremely difficult to remove to correct the defect.
Simply put, there are three basic solutions to cold foam problems; add heat, add heat and add heat. Add heat to the chemical in storage and transportation. Add heat to the chemical through properly functioning primary heaters and temperature-controlled hose heat. Add heat to the substrate. Call your cold weather expert for advice. SES tech reps have years of experience with cold weather spraying and they can help to maximize your crew’s productivity.
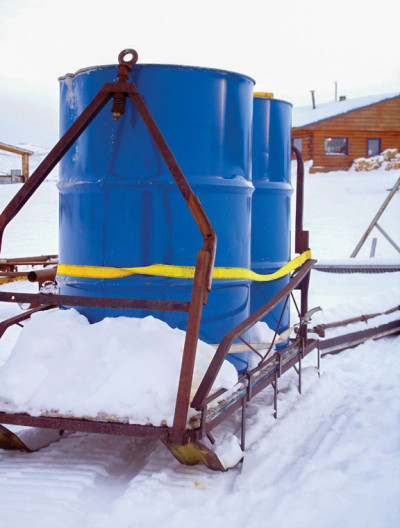
If you’ve chosen a proven formula like SES NexSeal® Winter, you should be able to spray most days of the winter as long as you heat your chemical, your rig and the substrate. To protect your profit, stick to true 2-pound foams designed for winter application such as SES NexSeal® Winter Formula.
SES NexSeal Winter was tested at the Cold Climate Housing Research Center in Fairbanks, Alaska over an entire winter season. Performance was judged for dimensional stability and R-Value retention through -40°F winter weather and NexSeal® passed with flying colors! Having passed this rigorous test, SES NexSeal® is certified “Arctic Tested - Alaska Tough”. SES NexSeal® Winter is a cold weather foam you can trust from a company you can trust. Call SES Foam to learn more about heating-up your winter profits.
Disqus website name not provided.