Desert Paradise
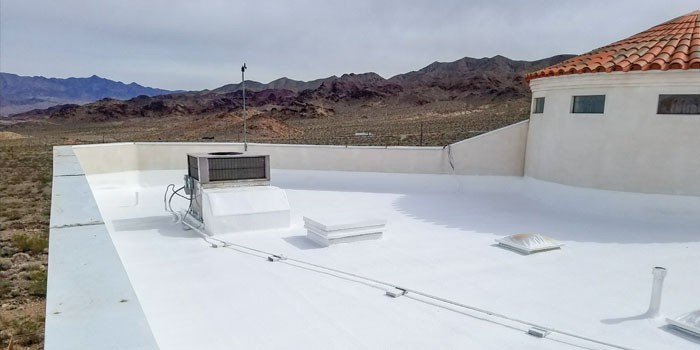
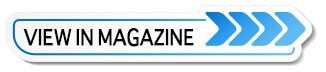
While tourists from around the globe drive or fly in to “America’s Playground”—Las Vegas—for unbridled entertainment and leisure, there are many who call this area in the state of Nevada home, but also prefer a quiet home life away from all the lights and ruckus coming from the Strip.
Such peace can be found some 32 miles southeast from the Strip in an area called Hemenway Valley Park, part of Boulder City, Nevada. Living around this area means being in close proximity to Lake Mead, a large lake in the Colorado River that traverses both Nevada and Arizona. Lake Mead is formed by the world-renowned Hoover Dam, and the lake itself is the largest reservoir in the United States in terms of water capacity. It is within close proximity of Lake Mead that a Las Vegas business owner wanted to hang his hat after a long day at the office. Therefore, he purchased a home located in a residential community on the side of a mountain that overlooks Lake Mead and all of its splendor, and where territorial bighorn sheep would visit from time to time. But peaceful as the location was, there were a few things that, if rectified, could make life a bit better for the indoor living aspect. The issues came from the cracks and leaks on the roof that had led to water finding itself through and posing problems for the entire structure and the high energy bills the owner had to pay due to lack of insulation. With consideration of the extreme temperature that dry desert weather can bring about, mainly its characteristic blistering sun throughout the day, it behooved him to fix these issues.
The home/business owner had previously commissioned Black Canyon Roofing (BCR), a roofing contracting company out of Boulder City, to install a spray foam system to the roof of his business’ building, which had been fraught with leaks as well. Since the system was able to stop the leaks and add R-value to that building, he figured “why not duplicate the effect in my home?” So, he once again called upon the services of BCR, led by father, Dennis, and sons, Dylan and Andrew Lawrence.
“After working on some commercial property for the owner in [Las] Vegas, he witnessed the performance of the foam firsthand, so it was a no-brainer for him when it came time to reroof his own home,” says Andrew. “Out here in the desert, a spray foam roof is the only roof that doesn’t ‘burn itself out.’”
Andrew elaborates on this statement by noting that, in this particular area, there are about 300 days of sunshine a year and over six months when it’s over 100°F nearly every day and three months where it’s over 110°F with evidently scorching summers. Because of this, commonly used roofing systems dry up, crack, and shrink, and separate from the drains and scuppers, causing leaks. With an SPF roofing system, that changes. The acrylic coating protecting the foam reflects the heat rays off the roof, which keeps the surface cool, and the foam underneath the coating insulates the home, creating a definite impact that keeps the home cool without overworking the air conditioning system, maintaining energy efficiency. In Andrew and his father’s experience, spray foam roofs have held up incredibly well against the desert sun.
“We have applied spray foam roofing systems to many homes around here that have remained in the same condition for 10 to 15 years as the day that we put them on,” says Andrew.
The BCR crew marked two days in their calendar dedicated to completing this project. The scope of the work included removing the existing torched down BUR roof system and then applying the new roofing system over a 2,000 square-foot area. To carry this out, BCR sent a four-man crew with a rig equipped with a Graco Foam Cat 400 Sprayer and a Graco GH 933 Big Rig hydraulic sprayer, a Graco Fusion AP spray gun, and 400 feet of hose out to the home.
The crew accessed the top of the roof by way of a 32-foot ladder and spent the first day removing the existing BUR system by hand to expose the roof’s half-inch plywood decking. They cleared off any debris that the demo process produced and left the substrate clean for the SPF roofing system installation, which took place on the second day.
Although the foam application took only a day, the BCR crew was extremely careful to not spray any materials when high winds were a threat. Andrew explained that the crew would stop what they were doing if high winds were present to reduce overspray damage, then resume the application accordingly. Furthermore, they masked off nearby cars for overspray protection. Then, the crew donned their coveralls, fresh-air respirators, gloves, and boots and began the roofing system application. The BCR crew also wore safety harnesses and tied off to roof anchors when working along the perimeter edges, and because they had parked their rig on the street in front of the home, they stretched their lengthy hose from their proportioner in their rig down the driveaway and onto the roof of the three-level home and attached it to their Fusion AP gun before carrying out the install.
The BCR crew utilized PremiSeal 300, a three pound closed-cell spray polyurethane foam system made by Carlisle Roof Foam and Coatings. The foam adhered to the plywood seamlessly as the BCR crew spray-applied to the roof surface one and a half inches of foam in two passes to the flat surface of the low-sloped roof. They also sprayed the knee walls into the flashing and around the penetrations of the roof with a one-and-a-half-inch pass.
After the foam had cured, the BCR crew coated the foam with 40 WTF mils of white AC100, an acrylic protective coating formulated by Armor Coat Roof Coatings. The coating was applied in two coats of white on white and used a wet film thickness gauge to make sure the specified thickness was applied. The white coating provided the roof with UV protection and reflectivity. The BCR crew completed the application within their stipulated time frame without setbacks.
The homeowner was decidedly pleased, according to Andrew, and for BCR this project was a notable example of a building owner that has complete faith in the benefits of a spray foam roof.
“It’s one thing to solve issues in one’s place of business, but nothing like experiencing comfort at home,” says Andrew. “I know that this is his dream home and he always wanted to be down by the lake, and now that these issues are out of the way, they will have a great indoor living situation with the help of bar-none the best roofing system in the market.”
With a robust, monolithic roofing system in place, this homeowner will be able to curb the effects of the desert weather for a long time to come. Andrew adds that this owner can kiss high energy bills in the summer goodbye and that his initial investment on this SPF roofing system for his home as well as his place of business will pay itself off in a few years. In summation, with a bit of spray foam in the mix, the desert might not be such a bad place to be and live in. •
Disqus website name not provided.