Fireproof Aeronautical Maintenance
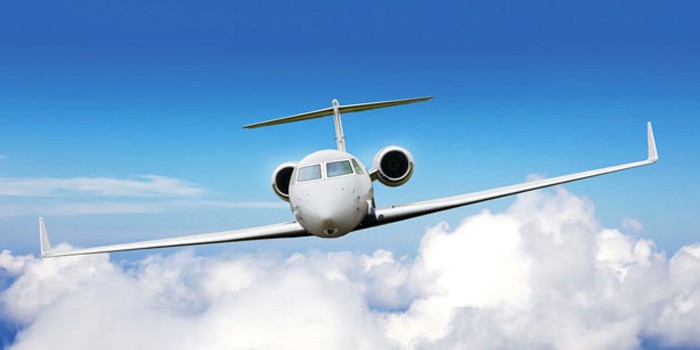
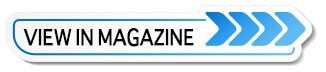

Envoy Airlines’ sizable hangars at Sawyer International Airport are used for jet engine maintenance.
JUPITER, FL – February 22, 2018 – If there’s one paramount component to aviation that stands above others, it is safety. Whether it is a small-engine Cessna or a commuter jet soaring through the open skies amidst photographic aerials views below, or a 747 commercial airliner carrying well over 400 passengers through the substratosphere from one country to another, the aircraft always needs to be in the best and safest condition possible. At Sawyer International Airport in Marquette County, Michigan, there is no exception to this rule.
Sawyer International currently operates a series of hangars leased to several airline tenants that are utilized as airline maintenance facilities and protective storage spaces for planes of different sizes. To give a deeper perspective, planes are literally disassembled, worked on mechanically, and put back together again inside these facilities. The planes are also stored here for lengthy periods of time, so a well-insulated, conditioned environment is important in maintaining them in optimal shape while they remain grounded.

The original fireproofing material delaminated over time and had fallen off in certain sections of the facility.
This latter factor was a determinant one when the County and their biggest tenant, Envoy Air Inc., a subsidiary company of the American Airlines Group, decided to have high-performance spray polyurethane foam (SPF) insulation installed inside their respective box hangars at Sawyer International—six in total. As it is typically the case with SPF applications, a thermal barrier was put in place to protect the foam, and considering the mechanical work taking place at these hangars, fire protection was key. Initially, the County went with a cementitious coating application, but in time, this material proved inefficient for it did not adhere to the foam properly and began falling off in large sections of the structure, which became troublesome since a clean, sterile environment is required while working on jet engines. To fix this issue, the County decided on a retrofit solution: A removal of the cementitious coating, a reapplication of a foam layer, and the application of International Fireproof Technology, Inc’s (IFTI) DC315 intumescent coating as a more effective thermal barrier.

Re-Foam and Re-Fireproof: The crew re-installed Icynene Classic plus open-cell foam, followed by a 20 WFT-mil application of DC315 intumescent coating as the new thermal barrier.
To apply the spray foam and the intumescent coating to the first hangar, the County brought in MAG Insulation, a spray foam contractor based out of Auburn, Michigan.
“We went in there with one task in mind: To fireproof the maintenance facility so the tenant knew the insulation system would remain in place and not interfere with their operations,” remarks MAG Insulation’s Dan Murphy.
Prep work was significant during this project. Murphy explains that Envoy had kept their maintenance operations active while the insulation project made headway, so the MAG crew could only work in half of the 200-by-200-foot structure at a time. The crew encapsulated the area with large coated tarps tied together, sealing off their work area from Envoy’s work area. By having the large door of the facility opened and using exhaust fans, negative air pressure and ventilation were created to ensure that the SPF, paint, and diesel fumes were being pumped out of the work area. With the use of plastic sheeting, the MAG crew masked off mechanical units and lights for protection from cementitious debris and overspray damage. Throughout the three-part project, the crew worked off an articulating boom lift containing fall protection and they wore PPE consisting of Tyvek jumpsuits, full-face respirators, safety goggles, gloves, and boots.

TOP: The intumescent coating firmly adhered to the new spray foam insulation layer; BOTTOM: MAG Insulation applied the foam and intumescent paint from an articulating boom lift, which gave the crew access to the higher, hard-to-get to areas of the underside of the roof
The crew used a combination of hand tools and compressed air to scarify and remove the cementitious layer. Equipped with a portable cart containing a mounted Graco E-30 proportioner with 150 feet of hose attached to a Graco Probler P2 gun, the crew then spray-applied 2.5 inches of Icynene Classic Plus open-cell foam to the exterior walls and to the roof deck, which had varying heights of 40 and up to 60 feet at the slope. Then, using a Graco GH833, the MAG crew applied the DC315 at 20 WFT mils over the foam in a criss-cross pattern. From start to finish, it took the MAG team four months to complete the retrofit job.
Brad Glazier, IFTI’s North American Sales Manager was proud of their product’s participation in this project. He notes, “The DC315 provides fire protection to the SPF insulation and meets interior finish requirements for the occupied space.”
The crew’s work was well received by Envoy, and the County expects to use the same approach on the five remaining hangars and looks forward to working with MAG Insulation in the same manner.
“The intumescent coating adhered to the foam perfectly. There will be no falling debris now, and the system will be there for the lifetime of the building,” concludes Murphy.
Disqus website name not provided.