Going Farther and Faster with Foam
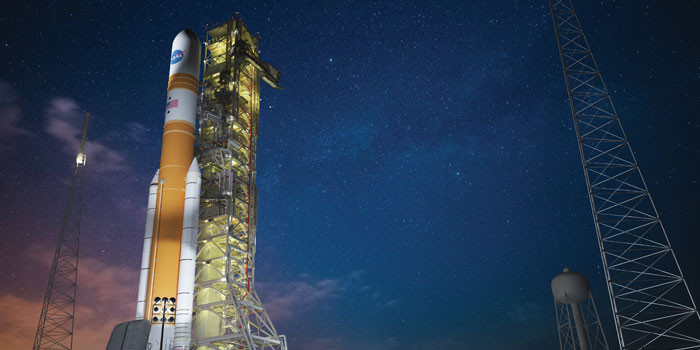
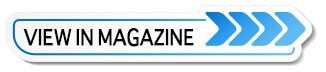
LATE SUMMER 2020 – Spray Foam Magazine – Spray Foam Magazine was once again excited to talk to NASA and how spray foam will be playing a role in the monumental launch of their Orion spacecraft.
We are honored to share the information that NASA provided to us in the following article.
Foaming the Core Stage of the Artemis I SLS Rocket
The National Aeronautics and Space Administration (NASA) is working diligently to land astronauts on the Moon by 2024 and spray foam is playing a big role in that mission. The Space Launch System (SLS) is part of NASA’s backbone for deep space exploration and will launch the Orion spacecraft farther into space than ever before. The SLS will be virtually covered in spray foam using various modalities of application.
Many of us recall the Apollo Program that gave humanity its first experience traveling to a foreign world. NASA’s 135 space shuttle missions, 20 years building the International Space Station—the largest structure ever constructed in orbit, and 18 years of continuous human presence in space have helped us learn to live and work in space. Currently in the testing stages, NASA’s next adventure—the Artemis program—starts when SLS blasts off the launch pad, making way for a new era of human exploration and discovery.
The SLS Rocket Stage is the largest rocket stage ever built and will fuel Artemis I. The backbone of this rocket is the Core Stage.
About the Core Stage
The Core Stage is 212 feet tall and 27.6 feet in diameter holding 2.3 million pounds of propellant—the cryogenic material that will fuel four engines to produce two million pounds of thrust to launch the spacecraft into deep space at a speed of MACH 23 (faster than 17,000 mph in just 8.5 minutes). The Core Stage is comprised of five sections with tanks that hold 733,000 gallons of cryogenic materials, liquid hydrogen and liquid oxygen. Each Section is insulated with spray foam. As of writing, the Core Stage is in the first testing phase at Stennis Space Center in Mississippi with a team of engineers who are dedicated to the manufacturing, application, and testing of the foam.
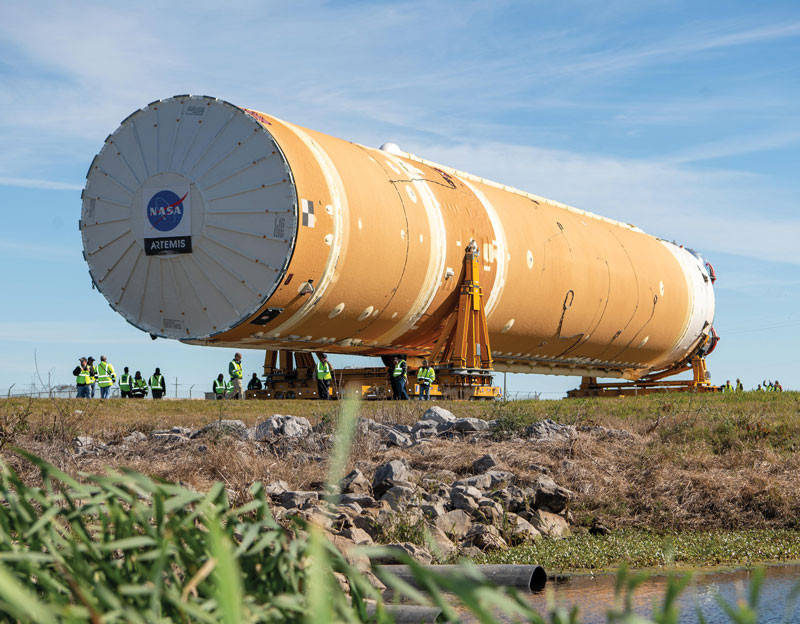
The Space Launch System (SLS) rocket’s core stage is transported from NASA’s Michoud Assembly Facility in New Orleans to the agency’s Pegasus barge. The entire core stage is sprayed with foam, which turns orange when exposed to UV rays.
Why Spray Foam?
Keeping the rocket’s propellant—the liquid hydrogen and liquid oxygen—cold enough to remain in a liquid state is vital to launching the rocket. The 537,000 gallons of liquid hydrogen has to be kept at -423° F and the 196,000 gallons of liquid oxygen has to be kept at -297° F. This is essential due to atmospheric friction occurring during ascent.
It is essential to keep the liquid hydrogen and liquid oxygen at these cold temperatures in order to provide the engines with properly conditioned propellants. Therefore, the entire outside of the Core Stage and all other intricate parts and pieces such as lines, valves, hoses, etc., must be insulated to the highest standards because on a project like this, there is absolutely no room for error. In certain smaller areas, cork that has been coated with a weather bearing coating is also used as an insulator.
Spray Foam Development
SPF was used to some degree in the Apollo missions; however, during the Space Shuttle Program is where NASA really took its use of spray foam to a whole other level. As NASA continued to look at the benefits of spray polyurethane foam insulation, they discovered what type of materials were best suited for the application, including the various ways to apply the foam and which method worked best on which parts. The Environmental Protection Agency (EPA) regulations have also driven changes in the foam. Improving results and meeting NASA’s unique demands, they are now using a third generation of foam development.
The foam is a light weight variation of closed-cell polyurethane that meets EPA regulations, and contains an HFC-245fa blowing agent that, so far, engineers say is performing very well. NASA works closely with trusted vendors on the formulation of their unique type(s) of foam, one that is lightweight, has good recession characteristics when exposed to launch and flight environments, and is flexible enough to limit cracks and debonds at extreme cold temperatures.
Over the years, NASA has developed a good rapport with a few key foam manufacturers whom engineers collaborate with to derive the perfect foam for their mission. NCFI, J6 Polymers, and Utah Foam Products work closely with NASA on spray foam development for each mission.
Meet the TPS – SPF Engineers
A new generation of engineers, who weren’t even born during the Apollo Moon landings and were children most of the Space Shuttle era, are leading NASA’s effort on SLS rocket thermal protection systems for the Artemis missions to the Moon. Each brings knowledge mixed with an exuberant passion and unparalleled excitement for their respective roles in building the SLS rocket.
Amy Buck is the Thermal Protection Systems Lead based in the materials and processes lab at the Marshall Space Flight Center (MSFC) in Huntsville, Alabama, interestingly where she also attended space camp in fifth grade. After high school, Amy went on to attend Auburn University where she enrolled in the engineering program and eventually interned at NASA. With a master’s degree in materials engineering, Amy was hired by NASA in 2014. Amy and her team are making sure the Thermal Protection System (TPS) is ready for launch when the heat from the atmospheric pressure collides with the extremely cold temperatures of the cryogenic tanks.
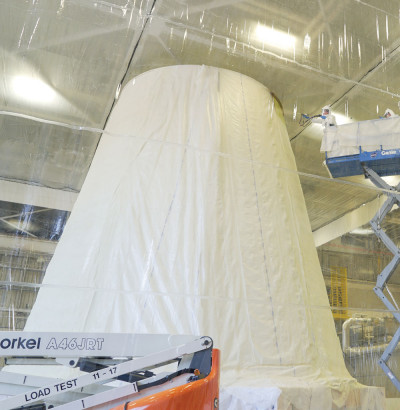
SPF is applied by hand to the Vehicle Stage Adapter at Marshall Space Flight Center in Huntsville, AL. It is the largest "by hand" application that NASA has ever applied at MSFC. The entire foam application process takes about three months, which mostly consists of prep work. The hand-spraying only takes about 30 minutes for each four-foot-wide section.
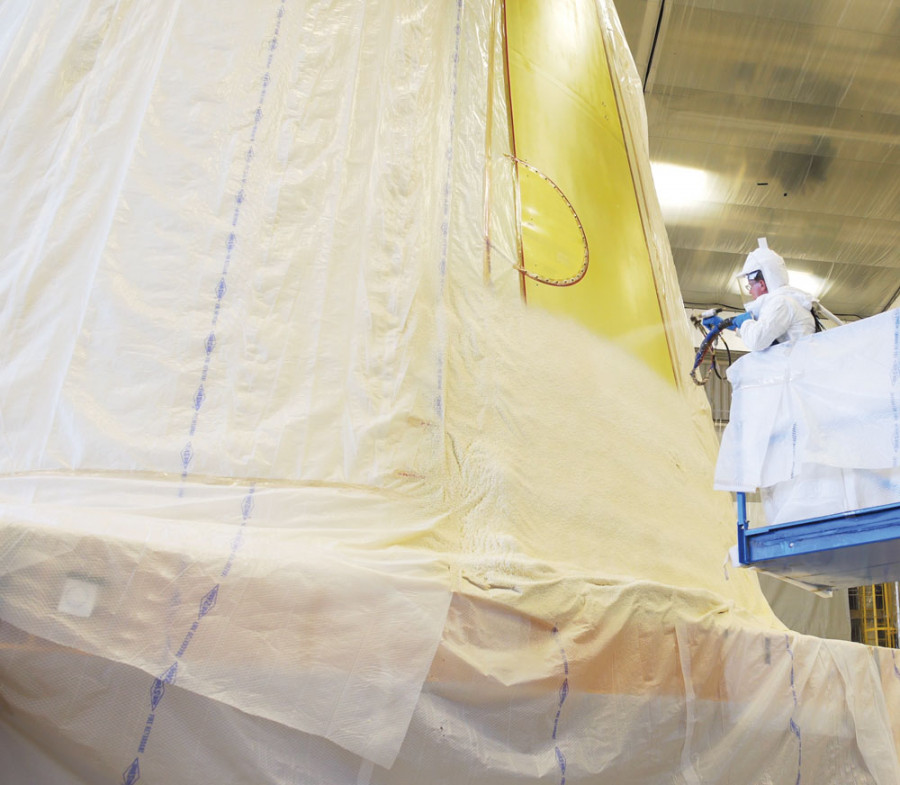
Jacqueline “Jay” Bourgeois is the TPS Manufacturing Operations Lead at The Michoud Assembly Facility (MAF), located in New Orleans, Louisiana. She leads the team of technicians and engineers whose primary function is applying spray foam insulation to the large propellant tanks and all of the small components used in the delivery of cryogenic propellants to the rocket’s four main engines. After graduating with a degree in Mechanical Engineering from LSU in 2015, Bourgeois spent five years as a government contractor developing the techniques, processes, and certifications used to apply spray foam to Core Stage flight hardware. She now oversees production TPS operations factory-wide.
Michael Alldredge is the SLS Stages Thermal Protection Systems Design Lead based at MSFC, with his territory extending all the way down to MAF and out to the Kennedy Space Center in Cape Canaveral, Florida. He is currently at the Stennis Space Center working Green Run testing and is primarily focused on helping the team complete TPS operations and prepare the first SLS Core Stage for live fire testing. Alldredge began working for NASA in 2008 after graduating from The University of Alabama in Huntsville. At NASA, he began his career in the materials & processes lab and transitioned into project management and leadership. Alldredge spent a great deal of time working hand-in-hand with the technicians and engineers at both MAF and MSFC to develop, scale-up, and implement the production processes used to apply spray foam to the first Core Stage rocket. He will follow the first rocket from production, through testing, and into final preparations for flight and launch from Kennedy Space Center.
Foam Application
On every part that needs foam applied, engineers look to three different application options depending on how large the part is, how intricate, and how complicated it is to get to. The three choices are hand spraying, robotic spraying, and pour foam. The entire outside of the large tanks holding the cryogenic propellant are sprayed robotically using the NCFI foam. It goes into a process cell and the robot sprays from one end to the other. The domes are sprayed by hand prior. Large acreages, the outside of the inner tank and the forward skirt are sprayed robotically while other portions are sprayed by hand. Smaller hardware such as internal fuel lines, valves, and brackets will be insulated with pour foam. The foam is mixed and poured into a mold before it expands to fill the shape it enters. NASA uses a unique 3-D printing process to make the customized molds. Alldredge states, “Some parts have unique geometries or are in locations in the rocket where it is difficult to cover them with spray foam. The 3-D printed molds allow us to shape insulation to protect specific parts.”
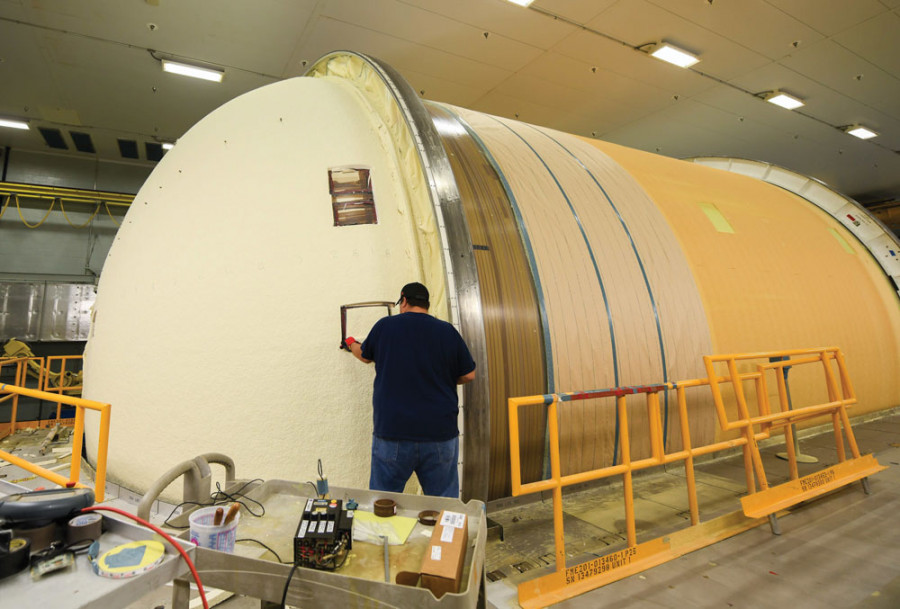
Robotic spraying of the front dome of the Core Stage.
Photos courtesy of NASA / Tyler MartinNASA’s expert team of technicians have a tremendous amount of experience in spraying foam. They take each piece that is receiving thermal protection, spray it, analyze it, and then, with the engineers, concur on the best way to apply the foam. During robotic material test sprays, they remove the human factor to achieve the desired material properties before introducing spray technicians to evaluate natural variability and ensure they have a robust material. There is a very high consequence of failure so the engineers evaluate materials very carefully to ensure accuracy. The demand on their work is very high and the technicians go through various intense levels of certification.
TPS Engineer, Michael Alldredge states simply and to the point, “We use spray foam all over everything.” The overall thermal protection system thickness for SLS ranges from a half-inch to two inches depending on the specific piece with some applications being a little higher in places. Michael humorously and yet seriously adds, “There is no room for inconsistencies with the application of the foam. It has to be perfect because when it leaves the stand on launch day, there’s no chasing it down to make changes.” Amy Buck wraps it up by stating, “It takes about three months for the entire foam application process, the prep work takes longer than the actual spraying. The hand-spraying only takes about 30 minutes for each four-foot-wide section.”
TPS – Spray Foam Testing
Back in January of this year, engineers at NASA’s Marshall Space Flight Center began activating the stage’s components one by one over several months through a series of initial tests and functional checks designed to identify any issues. Those tests and checks are collectively called Green Run, which is the final test before flight and will culminate in a test fire replicating the stage’s first flight.
This step-by-step testing and analysis was temporarily halted in March in response to COVID-19 cases in an area near Stennis; however at present, testing is back in full swing providing the mandatory testing that will reduce risk for, not only the first flight, but also for the Artemis mission that will land astronauts on the Moon in 2024. Green Run testing will bring the SLS rocket core stage to life for the first time, allowing engineers to evaluate the new complex stage that will launch the Artemis I lunar mission. In testing, engineers will evaluate the foam's performance and endurance under extreme pressures and operating environments. The two stages of testing that directly relate to the evaluation of the spray foam’s integrity is the “Wet” dress rehearsal and the Hot Fire stage.
During the “Wet” dress rehearsal stage, engineers will demonstrate loading, controlling and draining more than 700,000 gallons of cryogenic propellants into the two test stand run tanks and then returning the stage to a safe condition. From here the engineers evaluate how the foam reacts as the aluminum structure, the body of the vehicle, contracts.
As from other previous missions they expect to see frost growth and icing in certain areas. They will be looking at what happens during preflight conditions and in areas of transition from what Alldredge calls a “cold tank to an ambient temperature structure between the two tanks, and then we look at the areas of high compression and high bending moments to understand what the foam is going to do. This is a full scale test that will evaluate the thermal performance of the foam paying particular attention to any repairs to the foam that may be needed before flight.”
During the Green Run Hot Fire test, the core stage’s four RS-25 engines will operate for up to eight minutes, generating 1.6 million pounds of thrust, the amount of thrust needed on the launch pad at liftoff. In this test, NASA will load all the cryogenic propellants onto the vehicle, hold while the vehicle stabilizes, and fire all four engines for an eight minute burn. This is the same run time for the vehicle to ascend into space.
The engineers can then see not only the chill down, but the effects of the radiant heat and how the structure starts to expand and how the foam travels with it. They will be able to see all the different interactions of the foam within the vehicle. Alldredge says simply, “Essentially, Green Run testing is where they take a brand new rocket out, test it and make sure it’s ready to fly.”
After Hot Fire testing, the Core Stage will be sent via barge to Kennedy Space Center for final launch preparations. The Kennedy team will be responsible for stacking and integrating the vehicle and applying more foam as needed and then preparing for another “Wet” dress rehearsal and launch. The bulk of the work at Kennedy is preparation for flight with minimal repairs.
The next time the RS-25 engines fire, the SLS will launch in an epic debut of Artemis I—the first in a series of increasingly complex missions that will enable human exploration to the Moon and Mars. Many factors are involved; however at present, Artemis I is scheduled for lift off from Kennedy Space Center some time in 2021.
NASA engineers discuss the use of SPF in space
What is it like to work with spray foam that will be leaving Earth's atmosphere?
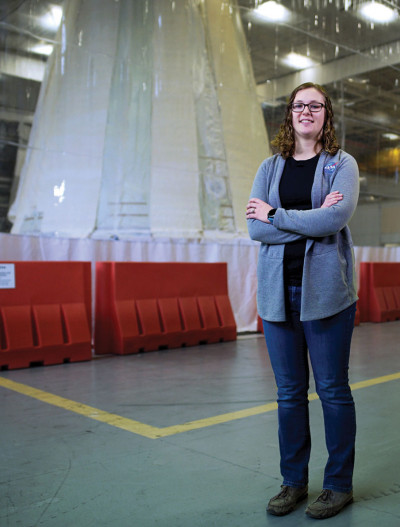
AMY BUCK
“The spray foam we work with is relatable to people. Yes, we've worked with vendors and developed a special formula that's a little different, but it's essentially the same stuff people put in the walls of their homes. Spray foam is something almost everyone knows about and it's just cool that we can take something that most people have some familiarity with and use it on something that's going to space. We use more on one tank than is used in a whole house!”

JAY BOURGEOIS & MICHAEL ALLDREDGE
Jay: “I agree with Amy. It is really amazing in regards to seeing something so common being used and we get to send it into space to help the astronauts with their mission.”
Michael: “Most people don't think of all the little things it takes to pull this off. It's more than just a few people getting together to solve complex problems. Foam is not for the weak at heart and it's certainly not when you're flying a mission into space. It takes everyone and everything involved to make this work and get us ready to fly.”
Disqus website name not provided.