Going the Distance
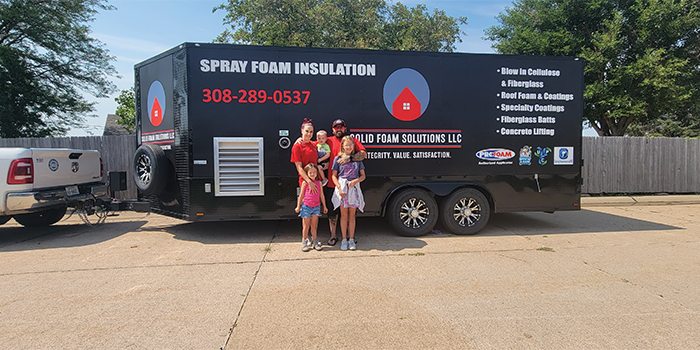
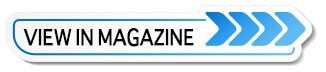
SPRAY FOAM MAGAZINE – Thomas Rizza is the Owner/Operator of Solid Foam Solutions (SFS) in Ogallala, Nebraska. Started just three years ago, SFS is a small operation, composed of himself, his wife Kayla, one sprayer, and two helpers. Despite their operation’s modest size, Thomas’s 14 years of experience in the spray foam industry combined with his reputation as a tenacious problem solver has reaped huge opportunities. One such opportunity brought him and his team over a thousand miles away to White City, Oregon, where they worked methodically over the course of seven weeks to clean up another spray foam company’s big mess.
White City Veteran Affairs Facility was in the midst of construction that had taken a disastrous turn. Another spray foam contractor had done a poor job applying SPF during a previous stage of the project. Unfortunately, that particular company was not around to fix their mistakes, having either gone out of business or otherwise ceased operations. The VA facility’s construction would not be complete until the shoddy foam job got fixed. They found that finding another spray foam contractor willing to take on the botched job was incredibly difficult.
Cornerstone Contracting, Inc. the company in charge of the build, consulted many different spray foam companies over the course of a year. After assessing the job and realizing the extent of the work involved, all the companies opted out– all but one. Cornerstone Contracting had previously worked with Rizza on a roofing consultation for another project, and recalled that he had been knowledgeable and professional. In August of 2023, they reached out and asked if Rizza would fly out to Oregon and take a look.
“There’s rarely a project that’s going to make me say no. So I flew out there and ended up saying yes.” Rizza said.
Agreeing to take on the job was an easy decision, but the SFS team had their work cut out for them. After taking samples of the botched foam, Rizza found it had been sprayed at inconsistent depths and was not up to code nor the manufacturer's specifications. Some areas were far too thick and other areas were about three inches short of the required six-inch depth. Before they could even start respraying, the team would need to remove over 4,000 sq. ft. of bad foam and start from scratch.
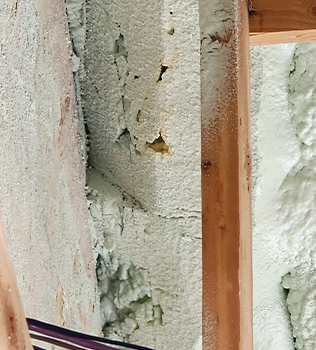
Rizza detailed what he found after taking foam samples: “I cut into the foam all the way to the roof deck to check its depth. It was supposed to be six inches total, but in some areas, it was only five. I also checked how many layers had originally been sprayed because the chemical is only rated for a certain depth per pass, so there always needs to be multiple passes.”
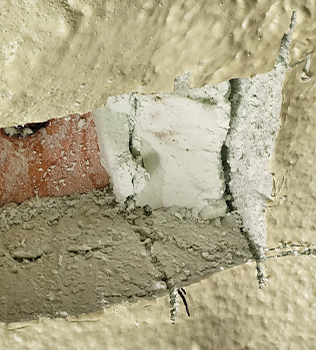
Many of the samples he took showed that the majority of the foam was sprayed appropriately, but the more problematic samples came from hard-to-reach areas like above stairwells. “Some of these spots had been sprayed up to nine inches thick, and when I cut into it, I could see the cell structure was burned.”
When SPF is applied too thick, it can have an exothermic reaction, which chars the foam and causes large holes. Rizza believes that the previous company had a difficult time reaching the areas on the stairs because they did not build the proper scaffolding, which resulted in the uneven application. “Because they couldn’t actually reach, they didn’t have enough control over how much was sprayed at once and sprayed it way too thick.” Rizza explains.
They spent the first four days of every work week almost entirely on preparing the work area. A lot of prep work involved meticulously covering everything in plastic to eliminate overspray and protect the freshly hung and painted drywall, as well as newly installed fixtures like HVAC platforms and fire sprinklers.
Prep work also involved tearing out the bad foam to prepare for respraying. The SFS team had to build a scaffolding platform to help them safely reach certain areas and sometimes had to block off the stairwell while they worked. After spending days prepping the area, they only had one day a week to spray.
Removing the foam took the longest and was the most labor-intensive part of the project. It was also the most likely reason why other spray foam companies had turned down the job. Rizza and his team worked tirelessly, taking the old foam out using pry bars and grinders, and smoothing it back down to the wood substrate using a wire wheel.
“We were pulling ten-hour days, four days a week, just on prep work where no spraying was even happening.” Rizza recalls. His sprayer Alex Smith and two helpers, Ethan Hunt and Quincy Randall were invaluable to getting the job done to a high standard, despite the hard work and numerous challenges they faced. “It wouldn’t have gotten done without those guys.”
Another challenge was that most of the spraying occurred in close quarters– like an attic space or a stairwell. While working, the SFS team wore protective coveralls and full-face respirators and pumped in fresh air through ventilation systems made from 12-inch air ducts coupled with fans in all doors and windows. Because the VA Facility was still going through construction, Rizza’s team had to coordinate with other trade crews. After spraying, people could not re-enter the building for 24-hours and the other tradespeople working in the building had to stop what they were doing and wait.
They also had to comply with OSHA regulations they were not previously familiar with. Rizza explains: “We normally operate in a very rural area without the same guidelines. It was a learning process for us.”
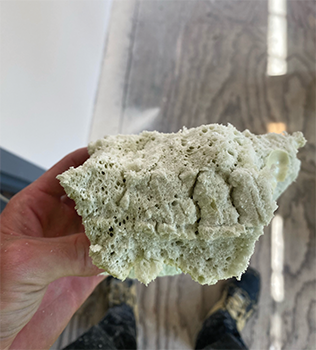
All in all, their conscientiousness ensured a proper foam application, in even layers totaling six inches as recommended by the manufacturer, for a total R-value of R38. For foam, the team used Huntsman Demilec HFO, topped off with a fireproof coating. They applied the foam using a PMC PH-40 machine equipped with a 360-foot-long high-pressure hose, T3 barrel pumps, and a Carlisle ST1 spray gun.
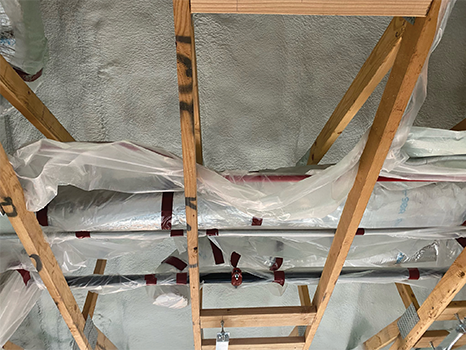
The spray foam machine ran off a 45-kilowatt Kubota generator. All of their equipment fit in their work truck and spray foam rig built by Profoam, which they easily towed 20-plus hours and 1300 miles from Ogallala, Nebraska to White City, Oregon and back again.
After seven weeks of non-stop sweat, elbow grease, and spraying, the Solid Foam Solutions team managed to bring the White City Veterans Affairs Facility back up to code. Rizza and his team came out on top after tackling a major job that other companies wouldn’t even touch with a 300-foot hose.
For use by SprayFoamMagazine.com & Spray Foam Magazine
Disqus website name not provided.