Golf Clubhouse Insulated With Open and Closed-Cell Spray Polyurethane Foam
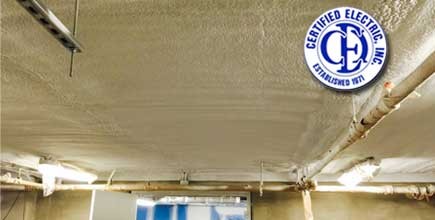
HILTON HEAD ISLAND, SC – February 20, 2015 – The boot-shaped South Carolina getaway known as Hilton Head Island offers a variety of activities that include beach days, boating, and above all, golf. With a series of golf courses set amongst a captivating oceanic backdrop, Hilton Head Island’s residents and vacationers certainly have high expectations when it comes to their golfing experience. With this notoriety comes the diligent responsibility of golf course operators to establish a equally pleasant clubhouse for their patrons.
A new clubhouse was recently constructed on the grounds of Harbour Town Golf Links, home of the RBC Heritage golf tournament. The course operators wanted to ensure that the clubhouse building had good insulation so that golf players and guests are comfortable before teeing off or while taking a break. Therefore, after the steel frame of the clubhouse building was built, the golf course operators contracted Georgia-based contractor Certified Electric (CEI) to install spray polyurethane foam inside the clubhouse.
“The best product for insulating a building is spray foam,” said CE’s Emory Young. “If the course operators wanted their building to perform well, then they selected the right product.”
The project consisted of applying SPF to all three levels of the building: two occupied floors and a basement. The spray area specifications consisted of 17,000 sq. ft. for the underside of the roof, 15,000 sq. ft. for the exterior walls, and 15,000 sq. ft. for the basement application. Additionally, the project included a sound-deadening SPF application between the first two floors that consisted of a 13,000 sq. ft. spray area.
The CEI crew brought onsite one rig, which was equipped with a Graco E-30 proportioner. Even though the SPF application entailed accessing several areas of the 45,000 sq. ft. building, the crew reached all areas without having to move their rig around by making full use of their 300 feet of hose. The crew strictly worked at night to ensure safety for clubhouse bystanders and to avoid daily foot traffic.
“We didn’t want anybody breathing in chemicals and causing damage,” said Young. “It was such a fast-paced project that even subcontractors wearing proper PPE working while we were there would have been a burden for us and vice versa. The night shift was easier all around.”
Before the application commenced, the CEI crew ensured that all the buildings’ openings were protected with plastic sheeting to reduce overspray damage. The CEI four-man crew, comprised of two sprayers and two helpers, wore PPE that included Tyvek suits, hard hats, and full-face hoods that attached to a Tennessee Chill Box air-conditioned respirator. The crew also set up two large exhaust fans on the doorways to ventilate the area. Since the roof underside had an 18-roof pitch from the attic, the crew utilized a scissor lift to apply the foam to the roof deck and the upper areas of the exterior walls. The crewmembers wore safety harnesses while working on the lift.
During the SPF application, the CEI crew used a PMC AP-2 spray gun, as well as open-cell and closed-cell products formulated by NCFI Polyurethanes. They installed a total of 53 sets of foam throughout the job. For the roof deck application, the crew installed 12 inches of Sealite, a 0.5 lb. open-cell spray foam. Sealite was also utilized for the SPF application between the floors, where the crew installed six inches of foam for soundproofing.
“The use of open-cell foam provided a cost-effective but equally compelling solution for the project overall,” said Young.
For the closed-cell foam applications, NCFI’s 2.0 lb. InsulStar was utilized. The CEI crew applied six inches to the exterior walls and three inches of foam to the basement’s ceiling and exterior walls. For the latter application, the CEI crew used Foamrite USA’s measuring pins while spraying to eliminate guesswork and for added precision.
“We wanted to keep everything in the basement as smooth as possible and the pins eliminated the need of having to constantly check the depth of foam,” said Young. “The pins helped maintain a nice even amount of material in the basement at the right thickness.”
The CEI crew completed the spray foam application in 27 days. After the crew left and the foam cured, a subcontractor applied to the roofline and basement 22 wet mils of DC-315, a fire-protective coating made by IFTI. Young noted that the benefits provides by the application of SPF will surpass the golf course operators’ expectations.
“Spray foam gives the building a complete air seal,” said Young. “It will provide the building with optimal R-value that results in reduced energy costs and ideal indoor temperatures. Plus, the closed-cell on the exterior walls and the basement will give bolster the structural integrity of the building.”
About Certified Electric, Inc.: CEI has provided electrical service, electrical contracting, heating & air conditioning service, and HVAC contracting for over 41 years. The company also provides cellulose insulation, spray foam insulation, and duct cleaning. For more information about CEI please use the contact details and links provided below.
Disqus website name not provided.