Greater Than Gold
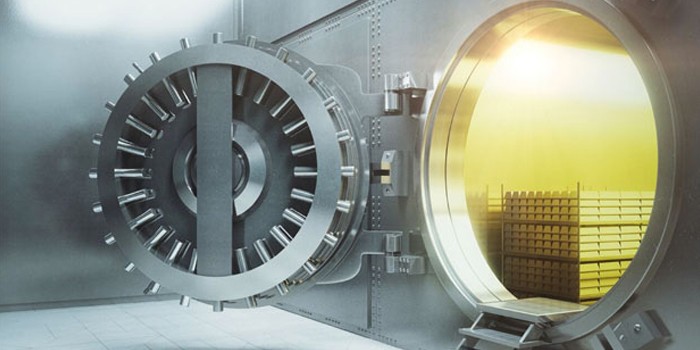
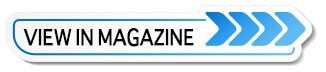
JUPITER, FL – February 16, 2018 – You’d think that Fort Knox Military Base—one of the most prestigious army posts in the United States and home of the United States Gold Bullion Depository—would not require extra protection in any way. After all, the United States Gold Bullion Depository is one of the largest gold reserves in the United States and the planet, and as of April 2016, Fort Knox is estimated to have gold holdings to the tune of 4,582 metric tons, which equates to 147.3 million oz. troy. At a rate of $1,226.60 an ounce, that roughly translates to $180 billion being held in one place. That in itself is synonymous to safekeeping.
But it’s not protecting the gold that recently sparked cause for concern; rest assured, the 109,000-acre base is well-guarded. It is the protection to one of the structures that lie within the compound that came to the attention of the operators at the base—an elementary school.
That’s right: Add four schools (two elementary schools, a middle school, and a high school) to a sizable gold vault, military training facilities, and other numerous structures inside Fort Knox. Then couple that with the fact that this base is one of only three Army posts that still have schools located on-post. An emphasis on exemplary education certainly reverberates within the confines of this compound, which is why the state of these structures was prioritized. But what was the nature of the problem?
About 20 years ago, a spray foam roofing system was installed to one of the elementary schools, which was a seemingly smart decision by the Fort Knox building ownership, except that a major flaw occurred during the install: The foam was not installed with enough depth in some areas of the roof to create the build necessary for optimal drainage. So, even though the roofing system itself was conducive to optimal building performance, significant ponding that added weight and pressure on the roof surface formed, which lead to cracks in the system over time. Incidentally, the best way to remedy this situation was not a tear-off, but a reinstallation of the SPF roofing system—the right way, this time around. Purefoam Roofing & Insulation, a Kentucky-based spray foam contractor, was tasked with the assignment.

Fort Knox is a United States Army post in Kentucky south of Louisville and north of Elizabethtown and is the site of The United States Bullion Depository, which houses a large portion of the country’s official gold reserves.
“The roof was holding a lot of water—about four to five inches in some areas,” notes Manuel Adler, owner of Purefoam. “It was not leaking though—that’s the great thing about spray foam, that even when ponding is a factor, it still provides a water barrier for a long period of time. It goes to show that, with the right build, this is the best performing roofing system. However, the weight that the roof was being subjected to was considerable and could have resulted in leaks and other problems in the long run.”
Adler and three other crewmembers partook on the reinstallation, which entailed four different phases: Scarification, foam application, silicone coating application, and granular embedment. According to Adler, the crew carried out the four phases of the project over a particular area each day over the course of the two-week job, and as the crew worked around the 35,000 square-foot roof, they were mindful of installing foam to a greater depth in certain areas to provide the adequate slope for drainage. He also confirms that the crew averaged 2,500 square feet per day of complete installation, from removal to granule application. Purefoam linked up with NCFI Polyurethanes, who supplied the materials for this roof installation. To execute the installation, the crew brought a 20-foot, self-contained trailer on site, which they parked in the front-center of the building, enabling the Purefoam crew to bring their equipment onto the roof and move around in all directions without needing to move their rig. Adler noted that because the trailer was thoroughly inspected daily at the security checkpoint, the Purefoam crew had a checklist of exactly everything they were going to need for the job each day of its duration.

The lack of build on the roof had caused water to pool and add weight to the roof system. Before the team from Purefoam could begin to fix the problem, perimeter flagging had to be installed throughout the work area to prevent falls.
“We needed to make sure everything was streamlined,” says Adler. “The rule of thumb was: Whatever we took in, we brought back out. That meant no loose tools or unnecessary pieces of equipment, regardless if they could have helped us a bit more on the job or not.”
Once through the checkpoint, the Purefoam crew made their way to the school. At one story that was 12 feet high from the ground, the crew easily accessed the top of the building by ladder.
First, while utilizing a West Roofing Systems roof scarfer machine, the Purefoam team removed from the roof surface the existing top layer consisting of an inch of foam and silicone coating. They then cleared the debris using a broom and backpack blowers.
Then, using a Graco H-40 hydraulic foam proportioner and a Graco Fusion AP spray gun attached to 400 feet of heated hose, the Purefoam crew applied to the roof surface EnduraTech 10-011, a 2.8 lb. closed-cell spray polyurethane foam formulated by NCFI. Adler noted that they applied three to four inches towards the middle of the roof where the main HVAC metal ductwork of the building was located. While building up the roof with foam, the crew also managed to encapsulate the HVAC ductwork. The crew then reduced their foam depth application to one inch as they got closer to the edges to create the appropriate drainage slope. In total, nine sets of closed-cell spray were installed to the roof.
“By encapsulating the ductwork with spray foam we were able to provide energy efficiency in that the building will not lose heated or cooled air through the metal units anymore,” remarks Adler.
Up next was the Momentive silicone coating application, which was completed with a Graco GH 833 Big Rig gas hydraulic sprayer. The dark gray base coat was applied at 12 mils, while the light grey top coat was applied at 18 mils. To finish off the roofing system, the crew broadcasted 3m granules into the wet top coat using a granule hopper.
To ensure safety, Purefoam and the operators at Fort Knox made sure that the time frame in which the project took place fell under the summer break, so there was no foot or vehicle traffic to be concerned of. They installed metal roofing stands with perimeter flags six feet from the roof edges to provide fall safety and two crewmembers held wind screens behind the sprayer while the materials were spray-applied. Crewmembers wore Tyvek suits, spray socks, safety glasses, gloves, and boots while installing the roofing system.

Foam to coating application The SPF was applied at varying depths to provide an optimal slope for drainage. The roof system encapsulated the HVAC ductwork on the roof, providing greater energy efficiency to the building.
“Upon completion, there was no water standing; it all flowed right down to the gutters,” notes Adler.
And because Fort Knox strives to add a layer of “protection” across the board whenever possible, Purefoam and NCFI provided a 15-year “No Leak” warranty for materials and labor.
“These warranties, in a way, let the effectivity of spray foam roofing systems speak for itself,” says Adler. “Now, since there was a case of a bad installation issue here in the past, a warranty that ensures that the building will perform in an excellent manner; without leaks—otherwise we cover it—definitely provides peace of mind.”
Water diverted; weight dissipated; cracking eliminated; a water and air barrier to a building inside one of America’s most safeguarded landmarks was generated; it all equals up to the flourishing and robust protection of something that is perhaps of greater value than gold: The education of young minds.
For more information, please visit www.purefoamroofing.com.
Disqus website name not provided.