How SES Spray Foam Complies With New Assembly Tests
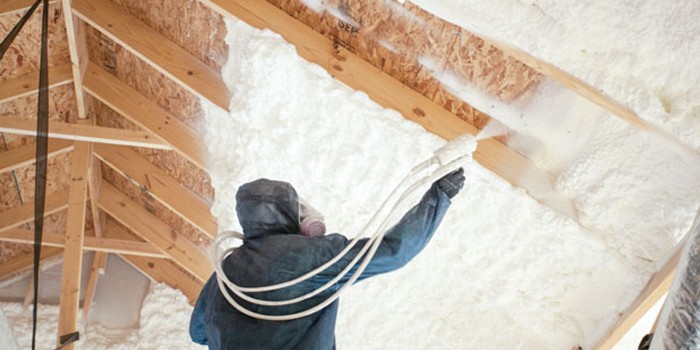
HOUSTON, TX – June 21, 2016 – If you think back to the last time you gathered with other spray foam contractors and discussed the business of spray foam, you no doubt heard things like:
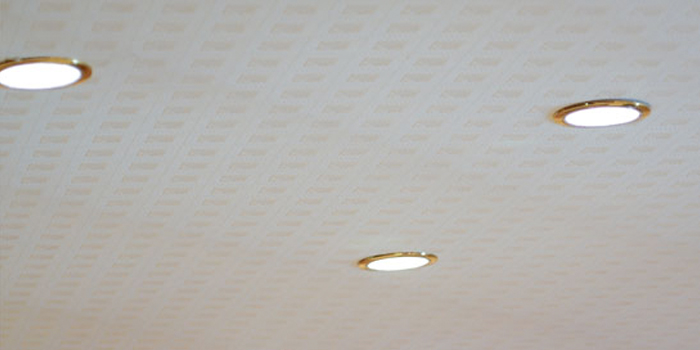
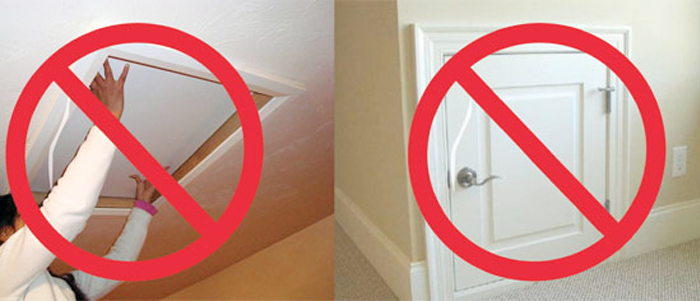
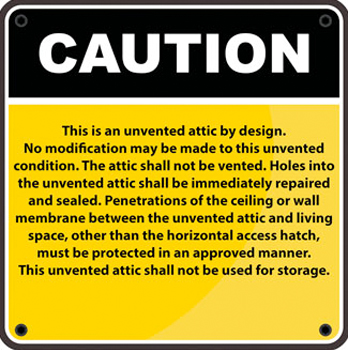
RELATED Are You Ready for a Big Change? , Tennessee Chill Box Launches Cool-Breeze Chill Suit, Flame Seal Products Reveals How to Expand Your Business Using Intumescent Thermal Barriers, OSHA Kicks Off ‘Hear and Now - Noise Safety Challenge’
CONCLUSION
Off-ratio foam can be a real problem.
We need fewer dealers in our marketplaces.
Finding and training good installers is a real challenge.
What you probably didn’t hear is, we really need to be careful to make sure our customers build their attics according to the requirements imposed by the fire test methodology for the spray foam we are using.
This new risk for contractors is most likely our biggest and deserves a tremendous amount of focus and communication to get it right for our customers, as according to Roger Morrison*, “The life safety of individuals is at stake. What happens in an attic fire when individuals try to access the attic, such as a homeowner from below or a firefighter from the roof? We just don’t know.”
This issue pertains to spray foam insulations which have been fire
tested in a simulated attic configuration where oxygen depletion has been the means of fire suppression (the so-called
“snuff test”).
LANGUAGE COMPARISON
In order to meet the current testing requirements for spray foam in attics used for mechanical access only, the industry is split between products that have been tested in accordance with AC377’s Appendix X and have achieved stand-alone product compliance with the following limitations:
“4.4.2 Application without a Prescriptive Ignition Barrier: Where the spray-applied insulation is installed in accordance with this section or Section 4.4.3, the following conditions apply:
a) Entry to the attic or crawl space is to service utilities and no storage is permitted.
b) There are no interconnected attic or crawl space areas.
c) Air in the attic or crawl space is not circulated to other parts of the building.
d) Attic ventilation is provided when required by IBC Section 1203.2 or IRC Section R806, except when air-impermeable insulation is permitted in unvented attics in accordance with 2012 IRC Section R806.5 or 2009 IRC Section R806.4. Under-floor (crawl space) ventilation is provided when required by IBC Section 1203.3 or IRC Section R408.1, as applicable.
e) Combustion air is provided in accordance with International Mechanical Code® Section 701. In attics, the insulation may be spray-applied to the underside of roof sheathing or roof rafters, and/or vertical surfaces, and in crawl spaces the insulation may be spray-applied to the underside of floors and/or vertical surfaces as described in this section. The thickness of the foam plastic applied to the underside of the top of the space must not exceed 12 inches (305 mm). The thickness of the foam plastic applied to vertical surfaces must not exceed 111/2 inches (292 mm). The foam plastic may be installed without a covering or coating. The insulation may be installed in unvented attics in accordance with 2012 IRC Section R806.5 (2009 IRC Section R806.4). The ignition barrier in accordance with IBC Section 2603.4.1.6 or IRC Section R316.5.3 may be omitted.”
And those that have not achieved the stand-alone criteria and have met the requirement through proprietary oxygen-depletion assembly tests and simulation requiring additional restrictions to conventional attic assemblies:
“4.4.2.1 Unvented Attics: The Manufacturer has conducted end use configuration testing (per IBC Section 2603.9 [2603.10] and IRC Section R316.6) and analysis to qualify the use of the insulation without a prescriptive ignition barrier or intumescent coating in unvented attics conforming with 2015 IBC Section 1203.3 or IRC Section R806.5 [2009 – R806.4]. (Note that unvented attics were not addressed in the 2012 and earlier versions of the IBC.) The testing and analysis is described in Priest & Associates … The conclusions of that evaluation (and associated Engineering Letters) are as follows: When the insulation is applied in unvented attics conforming to IBC Section 1203.3 or IRC Section R806.5[2009 – R806.4] the insulation may be applied to the underside of roof sheathing and/or rafters, and to vertical surfaces to a minimum thickness of three inches. Maximum thickness on the underside of roof sheathing or on vertical wall surfaces is 13 inches. The insulation may be left exposed to the attic without a prescriptive ignition barrier or an intumescent coating. The attic must have attic access complying with IRC Section R807, horizontally placed in the attic floor and opening outward toward the living space. For items penetrating the roof deck or walls, such as skylight wells or vents, the annular space must be covered with a minimum of three inches of the insulation.”
WHAT TO LOOK FOR
Manufacturers of spray foam products that rely on simulated attic tests often assume that an attic will be devoid of any penetrations or areas that could lead to air infiltration – throughout the life of the structure.
Items for a contractor to verify:
Annular areas around can lights, skylights, and dormer windows must be completely covered by the foam insulation.
When is the last time you saw the annular spaces of a window, skylight, can light, or other penetration such as an electrical wire through a ceiling covered with three inches of foam?
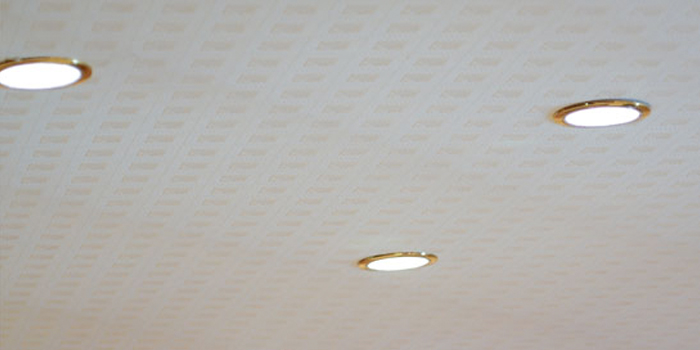
It is now your responsibility, if you choose to use a foam that has assembly testing as their primary means of use without ignition barrier, to spray the annular spaces of windows and skylights along with other potential penetrations.
Areas where assembly tested open-cell is used without an ignition barrier must have a downward facing attic hatch that will be displaced in a downward direction under pressure.
Have you seen attics accessed by scuttle holes or hinged doors?
It is your responsibility to communicate with your customers that these doors no longer meet the definitions as described in the assembly tested product documents.
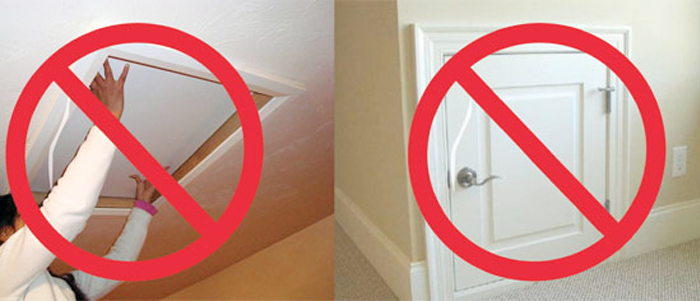
All spray foam products require that signage is posted in each attic area that describes the testing methodology that allowed it to remain uncovered.
Are you placing this, or similar signs in your attics to protect your builder and homeowner?
5.7.2 Signage shall be permanently affixed in the attic and shall be visible from all entry points into the attic. The sign shall state:
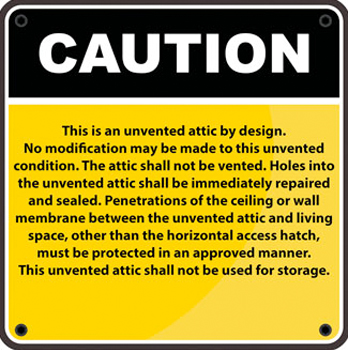
RELATED Are You Ready for a Big Change? , Tennessee Chill Box Launches Cool-Breeze Chill Suit, Flame Seal Products Reveals How to Expand Your Business Using Intumescent Thermal Barriers, OSHA Kicks Off ‘Hear and Now - Noise Safety Challenge’
CONCLUSION
These items along with others, place a tremendous amount of new responsibility on contractors and builders. Your liability as a contractor is significantly increased if you install these products without an ignition barrier and do not properly comply with the remaining requirements.
If all of this sounds a little scary, you as a contractor have options!
The first is to conventionally coat these spray foams with a prescriptive ignition barrier.
The second is to purchase and install open-cell foam products that have been tested in accordance with Appendix X and do not require these additional measures. One such product is SucraSeal by SES.
SucraSeal spray foam insulation passes the Appendix-X fire test uncoated, negating the need for an extra fireproof coating or unconventional attic assemblies. SucraSeal also provides consistently high yields and boasts the industry’s highest bio-content, making it the best all around open cell spray foam insulation available. Visit SESFoam.com to learn more about SucraSeal and all of SES’s innovative insulation products.
*Roger Morrison, P.E., R.R.C. is the President of Deer Ridge Consulting and an expert in building science, code compliance, and specializes in spray polyurethane foam roofing and insulation systems.
Contact SES FOAM
Direct any questions about managing the risks of oxygen-depletion fire tested attic assemblies to SES Foam:
Phone: 855-335-2440 / 713-239-0252
Website: www.sesfoam.com
Spray Foam Magazine does not take editorial positions on particular issues; individual contributions to the magazine express the opinions
of discrete authors unless explicitly labeled or otherwise stated. The inclusion of a particular piece in the magazine does not mean that individual staff members or editors concur with the editorial positions represented therein.
Disqus website name not provided.