How to Deal with a "Bad" Batch of Foam
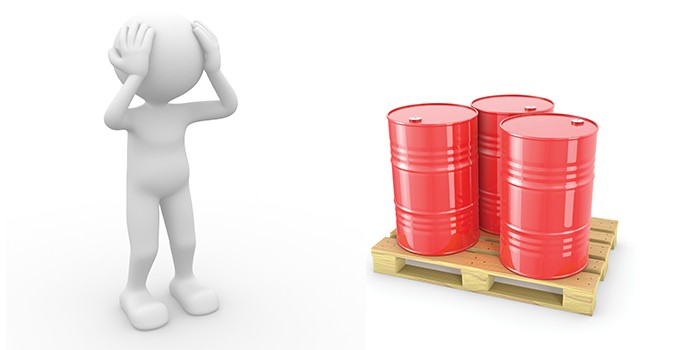
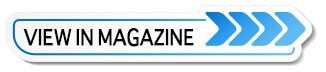
JUPITER, FL – May 3, 2018 – How do I deal with a “bad” batch of foam or coating?
Answer: Having been around the foam industry for more than 45 years, I have sprayed millions of pounds of foam and coating from more than 100 different suppliers. Any supplier can deliver a bad batch occasionally.
There are three ways a bad batch of material can be delivered to you:
1. The material was off spec from the factory.
2. The material was not stored or delivered properly (too high or low of temperatures, or extreme humidity).
3. The material was old and past the shelf life.
It is not very likely for a modern manufacturing plant to produce a bad batch of foam or coating. The equipment used to make the material is computerized to the extent that there is little opportunity for error. Plus, the quality control procedures from the major suppliers minimize the potential for off-spec materials coming from the factory. So that leaves shipping and storage issues as the most likely ways that a bad batch gets delivered to a contractor.
But before you contact your supplier about that bad material, investigate the possibility that it was not installed correctly. Make sure you have followed the manufacturer’s recommendations about substrate preparation, temperature, humidity, equipment settings and spray technique.
When your supplier asks for more information and documentation, remember that they have seen a lot of contractors blame the material for their own mistakes. It is up to you to convince your supplier that there is a real problem.
Bad spray pattern, slow rise & set, poor yield, and color variations are usually caused by equipment settings/ maintenance issues and/or applicator errors. But can also be caused by out of spec material.
Crystals can form in old A-side material. In this case A-side crystals from old material have clogged up the pump screen
When opening a new A-side drum, check the underside of the A-side bung lid for set up A
Realize also that your crew may not give you the total unvarnished truth about a material problem. Once, I had a good customer call me about a batch-mix polyurethane coating that didn’t set up right. He had good job records and a good track record of high performance. Our quality retain samples were fine. But since he was a good customer, we gave him the benefit of the doubt and replaced the material.
Some years later, I was talking to his main foreman who had since gone to work for another contractor. He told me that they forgot to put catalyst in the coating and that is why it didn’t set up. He was afraid of being fired and didn’t tell the owner. Keeping good job site records, weather, substrate conditions, equipment settings, maintenance and troubleshooting, application data, lot numbers, yield, spray pattern, storage and handling procedures, application data, lift thickness, and any anomalies during application helps show that you have done your best to follow their recommendations. With this type of documentation, our supplier is more likely to help you out.
What kind of help can you expect? The most common remedy is to replace the material that was bad and perhaps get a little extra. It is not common to pay for lost time and profits.
Disqus website name not provided.