Internal Innovation
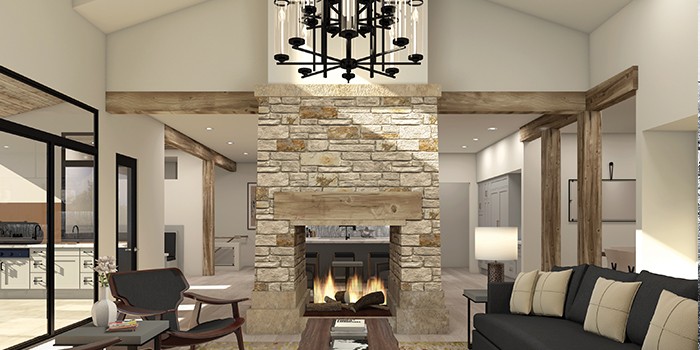
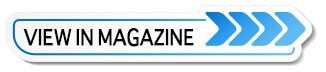
HOUSTON, TX – May 3, 2018 – Changes and innovation are always happening in the spray foam industry, and that’s what keeps it interesting, right? Recently, SES Foam and US GreenFiber® have created a fusion of their industry-leading products, SES Nexseal Spray Foam and GreenFiber® Blow-In Cellulose, in order to formulate a suite of services and solutions in an all-in-one product known as Custom Comfort Solutions.
A new custom luxury smart home in Austin, Texas built by elev8 Design + Builders, a local Austin-based home builder focused on innovative designs and superior materials, was chosen as one of the first projects for the installation groundbreaking product. Although the homeowners were aware of the benefits of spray foam and cellulose separately, the anticipation for the finished project was at an all-time high once they were educated on the many qualities that Custom Comfort Solutions would bring to their “Home of Tomorrow.”
Since the project is still underway, blueprints were provided to display the completed look of the “Home of Tomorrow"
The Custom Comfort Solutions program provides a minimum of 40 percent more energy efficiency¹, an airtight envelope, high-density sound abatement, equalized room temperature, fire-blocking benefits, and because Sucraseal Spray Foam has the capability to expand in tight spaces, it eliminates gaps in the attic where conditioned air can escape and unconditioned air can enter, therefore saving homeowners money on energy bills.
What is unique about the fire-blocking characteristic of the Custom Comfort Solutions System, is that Greenfiber provides a one-hour firewall that will give the homeowner more time to escape². Plus, SES Sucraseal passes the industry standard Appendix X fire test uncoated, which saves time and reduces costs of additional fire-proofing products.
“Confirming the well-known air sealing and insulation benefits of spray foam, and the ease of application when it comes to roof encapsulation, the Custom Comfort Solution adds to the sound and fire benefits that cellulose provides into the wall system. This fusion creates a valuable combination of two superior insulating materials,” states Charles Valentine, president and COO of SES Foam.
Due to the extreme density of GreenFiber, one of the exceptional benefits of the product includes its ability to break the path of sound providing reduction of noise transfer that temperature levels are equalized across multiple rooms and floor levels in the home, which may even extend the life of the HVAC system in the home.
The air sealing and insulation benefits of spray foam and the sound and fireproof benefits from the cellulose provides a valuable insulation solution for homeowners
“We have conducted sound testing and found that the rating is significantly better throughout the home. We guarantee that with the installation of this system, the temperature from the center of every room will remain plus or minus three degrees from the thermostat setting³,” says Laura Woodford, senior marketing manager of US GreenFiber. “When you install this hybrid system, you have the best of both worlds with the airtight seal characteristics of the foam, and the sound and fire resistance attributes of the cellulose.”
The timing couldn’t be more perfect to implement the latest spray foam innovation to the 7,100 square-foot custom Austin home since the entire residence is designed to be filled with advanced technology and appliances such as a whole house automated system, multi-zone security, solar panels, a golf simulator, and smart phone controlled lighting for the highest quality of living. In order to create an exceptional environment, elev8 Design + Builders brought in Garland Insulation Ltd. (GI) to insulate the two-story home.
“As a custom builder, all of our projects are site-specific. When we evaluated the performance of Custom Comfort Solutions and saw that it went hand-in-hand with the energy model of the Austin smart home, it couldn’t have been a better fit,” explains Chris Little, president of elev8 Design + Builders. “Now that a system has been developed by GreenFiber and SES under the same roof, we find a great benefit in having a single source manufacturer for this specialized type of insulating system.”
The GI team applied one inch of the SES Sucraseal closed-cell foam to the exterior walls and 7.5 inches to the roof rafters
Since the foam had to be applied as the construction of the structure of the home was underway, the application was done in two parts. The first portion, which consisted of insulating the exterior walls and the underside of the roofing, was efficiently completed in the span of three days.
Prior to the application, the three-man GI crew masked off the interior marble and wooden flooring, windows, doors, high-end finishes, and reclaimed wooden beams to mitigate overspray. First tackling the exterior walls, the sprayers applied one inch of the SES Sucraseal closed-cell foam with a Graco AP Fusion gun, two Graco E-30 reactors, and a IPM pump to the one-inch ZIP System Insulated R-sheathing boards. Moving onto the ceiling, the GI team applied 7.5 inches of the Sucraseal open-cell foam to the roof rafters/underside of roof deck.
For the second portion of the insulation job, which took two days to complete, a separate three-man crew from GI was brought onto the project to blow in 5.5 inches of the GreenFiber cellulose to the interior walls, 4.5 inches on top of the spray foam that was previously applied to the exterior walls, and 24 inches in between the flooring panels. Each of these areas of the home will benefit from the sound and thermal barriers the cellulose provides to mitigate the noise from the first to second floor, and to keep each of the rooms at the same temperature as the rest of the home. During both portions of the insulation process, the crews wore full-faced respirators, full-body cool air suits with a Tyvek suit underneath, and rubber gloves.
“The homeowner liked Custom Comfort Solutions as an eco-friendly, green product. With the foam insulation, the smart home will be very energy and monetarily efficient,” notes Jonathan Heathington, operations manager of Garland Insulation Ltd.
Although the project is in its last phase of completion as you are reading this, Little notes that even with construction going on outside of the home, once the owners stepped inside their freshly insulated home, they instantly noticed a difference in thermal comfort and sound depletion as a direct result of Comfort Home Solutions. And with such positive outcomes, SES and GreenFiber are now launching the product into select markets of the southern regions of the United States. Keep your eyes peeled and rigs ready for the new, all-in-one spray foam/cellulose innovation.
For more information on SES Foam, visit www.sesfoam.com. For more information on Custom Comfort Solutions, visit www.greenfiber.com/customfomfortsolutions, and for more information on Garland Insulation Ltd., visit www.garlandinsulating.com.
1. As compared to homes built to 2006 IECC code.
2. GreenFiber offers a full breadth of fire assemblies. Based on U305 assembly.
3. To participate in the Custom Comfort Solutions Program, the home must be built to an energy rating of 60 or below on the Home Energy Rating System (HERS) Index. When the program requirements are met, the home will be 40% more energy efficient as compared to a 2006 International Energy Conservation Code compliant home with a HERS Index score of 100. The builder must ensure compliance with applicable building codes and manufacturer requirements. When building in an area with no building code in effect, the builder must comply with the requirements of the current IECC for all items not addressed in the Custom Comfort Solutions Program. Guarantees are currently available to builders that meet program criteria in select markets only.
Disqus website name not provided.