Overhall
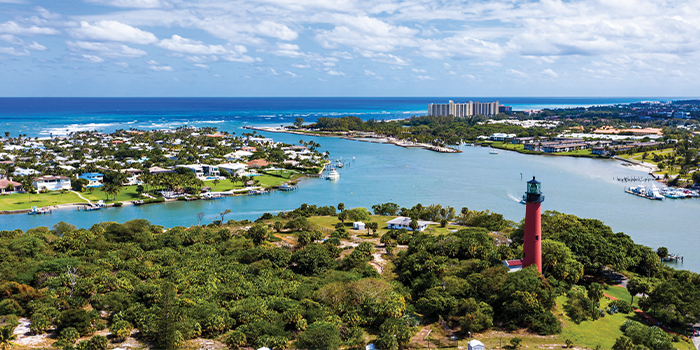
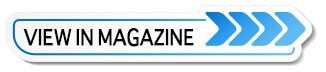
SPRAY FOAM MAGAZINE – The picturesque seaside town of Jupiter, FL is home to roughly sixty thousand people and a percentage of those are professional golfers, celebrities, and successful business owners. This affluent area also happens to be where Spray Foam Magazine’s headquarters resided for over 12 years. So, when the Spray Foam Magazine team (SFMT) heard about a Jupiter resident adding spray foam to his construction arsenal, we knew we needed to find out more. We were honored to spend a day and a half with Richard Hall, the owner of All In OverHall, LLC, and his crew, on a few concrete lifting projects, including a local celebrity’s driveway. After applying our sunscreen and with safety glasses on, we headed out to meet the team.
A Jupiter native, Richard Hall has a dry southern wit and describes his career so far as, “A little bit of everything.” Though very modest, Richard has years of experience in the construction industry, from working with concrete, to fifteen years in welding and fabrication in the marine industry. While working in construction, Richard came across projects where spray foam was installed. He was intrigued by it and wanted to be trained in both SPF insulation and concrete lifting. He heard that Profoam Corp. located in Rutledge, Georgia, a reputable foam and equipment supplier, also held foam and concrete lifting training classes. Hall knew their highly skilled support and training technicians would help guide him through the business.
Richard and his wife Megan headed to Georgia, bought their rig, and received some intensive training. “My wife and even our five-year-old son Wyatt, have both suited up and tried the gun. It really is a family business,” beams Richard, “There is lots of concrete here in Florida and we are built on a swamp so eventually things settle so there are lots of opportunities here for lifting.”
Fast forward several months and here we are with Richard Hall and his crew. The first thing the SFMT noticed was his awesome rig with an eye-catching wrap. Peeking inside the rig, it was immaculate. “Was this for our benefit,” we joked? Richard laughed “Nope, I like things to be tidy and organized.” Throughout the day, we soon discovered this was the case. Everything had its place, and all the crew knew how it should be set.
Richard introduced us to his crew: Gabriel Young (aka Gabe), a 19 year old working his way up through the ranks, and Michael Foster (aka Mike), who has 13 years of spray foam experience under his belt. Also joining the crew today is Profoam Corp’s Norman Laylon, a regional account manager who has a wealth of spray and concrete lifting knowledge.
It’s 8 am as we arrive in one of Jupiter’s exclusive communities, Jonathan’s Landing. As we drive to the first project of a sunken sidewalk, we admire the scenery from an array of houses and world-class amenities like pristine golf courses, marinas, and more. We assured both the General Manager, Sandy Matteson, and the Operations Manager, Lucas Jones, that we would be respectful to the residents and not block off any sidewalks or walkways.
After the crew had checked their PMC PX-7 mechanical purge gun (ideal for concrete lifting), and their PH-2 PMC proportioner, Norman Laylon fired up his own magic offering his wealth of expertise in concrete lifting. There is a mature tree right next to the sunken concrete slab and as the tree roots continuously look for water and nutrients, over time the surrounding soil is unable to support the concrete slab and thus the sinking occurred. Previously, the neighborhood had tried grinding the sidewalk to level it out but it looked substandard and exposes the aggregate, not to mention the noise and disruption it causes to the residents. Some tree roots in the neighborhood had also been cut back to help prevent slabs from lifting. The crew inspected the slab, measured it, and noted it had sunk two inches.
Assessing the surrounding slabs, the crew drilled a number of holes into the concrete around the slab using a concrete rotary hammer drill. It was then time to double-check the proportioner. With geotechnical foam, not as much heat is required compared to SPF closed-cell foam, where it would typically set at 120-130°F compared to geotechnical foam at an average of 100-110°F. “The foam needs to be processed a little slower as you don’t want the reactivity to be fast. Speeding up that exothermic reaction makes the foam expand quicker, so instead this foam needs to flow a little bit before it starts to lift,” confirms Norman.
Inserting a 2.5 lbs NCFI geotechnical foam (24-010), Richard pumped the gun for three seconds at a time, with short intervals to let the foam expand. Richard and Mike took turns to dart around the holes, with only enough time to replace the gun's rubber cover tip and quick enough so he would not have to stop and clean the gun each time.
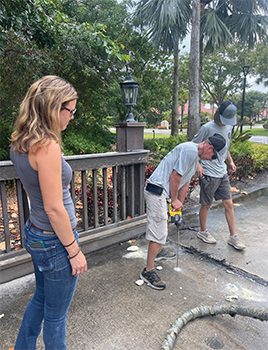
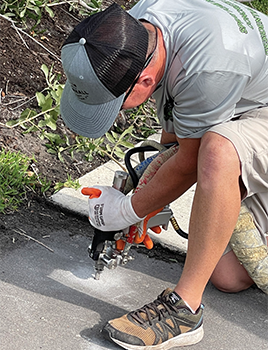
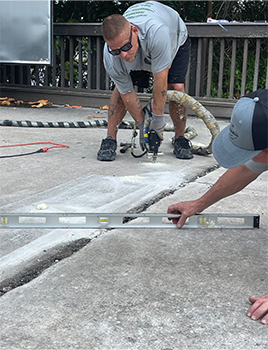
The result was impressive, and the crew was happy with the job. They cleaned up and moved on to the next project: a walkway.
This walkway was more problematic. The crew managed to lift a large slab that had originally been ground down to try and level it. However, after some time on the gun, the crew soon realized there was a massive void under the rest of the walkway which was swallowing up a large amount of their material and after some time there was no life. Chatting with the community management, both parties decided it was best to replace this area of walkway.
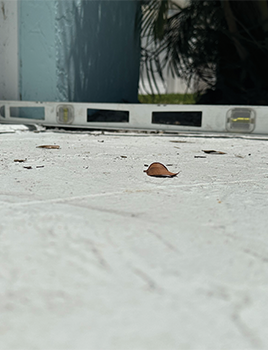
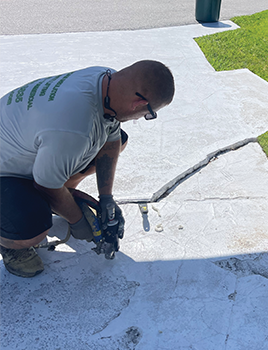
As the midday temperature increased, the crew kept their cool dealing with any unexpected issues that came their way. It was time to move to the other side of the neighborhood where a bridge had sunk two inches from the adjoining road. Norman noted that it looked like there had been an attempt to previously fix the bridge, which had sunk due to years of rain runoff. Richard drilled ten inches down every three feet into the concrete, and then started to insert the foam. Beginning at one end, then on to the next and then repeating until the concrete started to lift. It was an amazing sight to see that amount and weight of concrete leveling out to meet with the road. The crew celebrated the success of the lift and moved on to the next bridge. After eight hours of continuous work in the blistering heat, the Spray Foam Magazine team (SFMT) was overheating, and we were not even doing any of the manual work.
We waved goodbye to the crew, only to meet up with Richard and Mike the next day. Gabe had the day off and Norman had flown out to his next project. This next project was to help level a famous Palm Beach County DJ’s sunken driveway. On weekday mornings from 6:00 am to 10:00 am, Virginia Sinicki, the vivacious DJ from the KVJ Morning Show on WRMF 97.9, along with her crew Kevin, and Jason, entertain listeners as they get ready for school, work, or are on their morning drive.
Virginia and her family have lived in their beautiful Tequesta, FL home for nine years, a neighboring town to Jupiter. Tucked away in an oasis of palms, and tropical flowers, the neighborhood, which has a golf club and a swimming pool, also backs onto the Loxahatchee River Preserve. “The home was built in the early 90s so now it’s time for repairs. We got a quote for an entire driveway replacement, and it came in at $25k, so when we heard about a possible alternative, we knew we had to investigate. We are not the only ones in our neighborhood with this issue. There’s a shifting of whatever material is under this driveway. It just washes away. If you look at the drain to the side of the driveway you can see all this sand,” confirms Virginia.
An early riser, Virginia leaves her house at 4:30 am and returns at 11:30 am. She wanted to see how the crew was going to lift the driveway, so they made sure to work around her schedule. Following a previous job of lifting sunken concrete around a client’s pool, Richard and Mike arrived at Virginia’s at 2 pm. They quickly got to work on the first part of the project, a pathway leading from the house to the driveway which had sunk 3/4”. Using the NCFI TerraThane dual component system, Richard and Mike managed to lift the concrete a 1/2” in height.
Happy with these results, Richard and Mike moved on to where Virginia’s driveway meets the garage and had sunk 3/4”. After drilling into the concrete, they began the lift and in a short time managed to lift the area to within an impressive 1/16 of an inch. The project had been going well, but it was now time to try and lift the corner of the driveway, which had settled an immense 2.5”. As Richard and Mike drilled close to the area, their 24” concrete drill bit was quickly swallowed up. They soon realized there was a massive void under this part of the slab.
After drilling a few more holes in selected areas, they were able to determine how big the void was. They knew they had to attempt to fill it, even if it meant using a lot of their materials. A void like this, if left for a long period, could cause a plethora of issues, and could even result in a dangerous situation. Watching Richard and Mike dart around the drilled holes, filling them with foam, was like watching bumble bees fly from one flower to the next in a well-orchestrated dance.
Virginia was fascinated to see the crew at work, and some of her neighbors even came out to see what was going on. Asking questions about the technical aspects of the lift, Virginia took an interest in the entire process. As the afternoon’s heat intensified, they kept on pumping in the foam. “When there’s a void like this, we take it slowly. Pumping in the foam, leaving it to expand and set, and then we begin to add layers of foam. Think of it like a stack of pancakes,” explains Richard.
As we all held our breath, suddenly we started to see the concrete lift. Virginia was ecstatic, that the process had worked, and her driveway had a new lease of life. Richard and Mike didn’t stop there and continued lifting another settled area on the opposite side of the void which had also started to settle. After completing several areas of the driveway, they made sure the holes they had drilled were filled in with any cracks also being fixed. “We take the shavings from where we drilled the holes and mix it with some patch materials. That way when we fill the holes it’s the same color as the client’s driveway. Every driveway is a slightly different color, so this helps finish things off nicely,” said Richard.
As the crew packed up their equipment, Virginia happily reviewed her improved driveway. The Spray Foam Magazine team (SFMT), walked away with a sense of pride that they work in an industry capable of such an achievement. After spending a mere 1.5 days with Richard and his crew, it made us appreciate the hard work contractors do day after day. We would like to thank and acknowledge the All In OverHall crew for letting us spend time with them on the job. They work tirelessly to achieve what many clients may have seen as unachievable. All this hard work delivered with a smile on their faces, no sunken attitudes and always performing at a high level!
For use by SprayFoamMagazine.com & Spray Foam Magazine
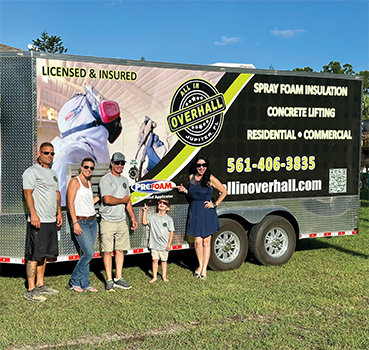
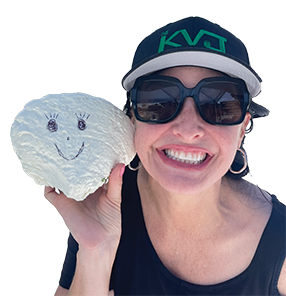
Disqus website name not provided.