Perfecting Execution
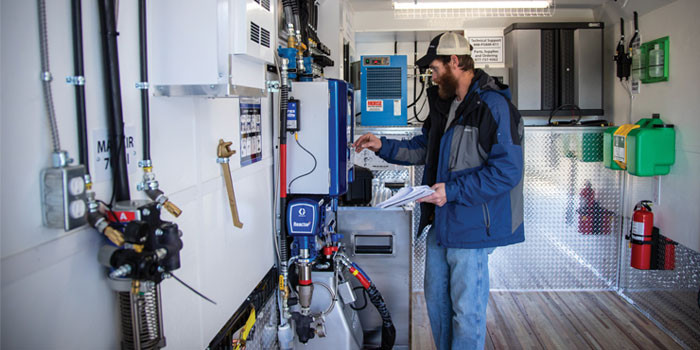
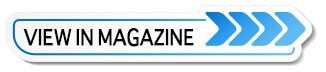
Spring 2020 – Spray Foam Magazine – Plural-component spray equipment can be used for applying spray polyurethane foam (SPF) and polyurea. If you offer spray foam insulation or polyurea services, it is important to do everything you can to keep your equipment and sprayers in good condition at all times to reduce downtime and maintenance costs. Follow these five guidelines to get the most out of your equipment with every passing year. The following guidelines are recommended off a ProPAK series including SFS Nitrosys and Graco equipment setups.
1. Check Your Power Supply Daily
Each day check the voltage on your machine(s). Be sure to check coolant and oil levels as well. Starting the engine up and letting it run for about five minutes will help you identify any other issues you may not notice once you leave the generator.
When starting the engine, turn on the main circuit breaker and inspect the radiator and compressor cooler for debris. If there is debris, use compressed air to clean the components. Inspect the engine, compressor, and radiator for leaks, as well as the fuel and coolant hoses.
Be sure to check the hour meter for any upcoming service(s) that may be due. You can find the service schedule for oil, fuel, and air filter changes in your equipment manuals. This will ensure everything is working as efficiently as possible, and it minimizes the risk of damage and downtime down the line.
A few simple checks every day can save you a lot of money on repair work in the future, and it nearly guarantees less stress from financial losses due to being down on the job.
2. Care for Your Hoses
Hoses are responsible for transporting plural-component materials to where they need to go. Therefore, keeping them in top-notch condition is vital. To prevent your plural-component chemicals from freezing in cold weather, always bring your hoses into the rig and hang them correctly on a hose rack. Be sure to keep them maintained and replace scuff jackets as needed. An alternative to standard scuff is utilizing insulated or non-insulated products. These form-fitting products are made with a thick nylon that make them resistant to tearing and other environmental factors, while using Velcro to keep them in place and form to the hose.
When switching between open and closed-cell materials, make sure you flush your B side with water so you don’t contaminate and lock up your whole system and the hoses, which can be costly to repair. During the time you are not spraying, or if you are putting your rig away for long-term storage, be sure to flush both the A and B sides with an approved solvent. Not doing so can force you to waste a lot of time on the next job trying to get everything prepped and ready to go. If you have any questions, check with your chemical manufacturer or an equipment technician on flushing processes, and, as always, be sure to follow proper safety protocol when handling the materials.
3. Invest in Yearly Motor Maintenance
If a motor is not in good working condition, your equipment cannot do much. Having it serviced at least once per year will make a huge impact on your operations. An expert in the field can take a thorough look at your system and determine whether or not new parts or repair work is necessary. Be sure to use an equipment technician who is qualified to work on your brand of machine in order to ensure proper maintenance.
For power sources, be sure to take your unit to a qualified service center of the manufacturer to ensure that all warranties are upheld. You can visit the website for the manufacturer to find service centers, and your original paperwork may list the terms of your warranty. This is a much better option than waiting until your spray equipment fails.
4. Keep Spare Parts on Hand
The best option to prevent longer downtimes, in case a component of your spray machine is not working, is to keep spare parts on hand. This is an easy and affordable step to take, and it is a much better option than buying what you believe to be the problem at the time of failure.
Your spray gun is the component in your spray system which is most likely to have issues. Its internal components wear out from use more quickly than any other component of the spray system.
Taking care of your spray gun is somewhat more tedious, but it will benefit your jobs and business. After every job, it’s important to remove any excess chemical from within the gun to prevent buildup and clogging. It’s a good idea to break down the gun every now and then and soak all the pieces in a cleaning solvent, thereby removing any debris and cleaning the parts. When reassembling the gun, make sure to grease all the O-rings to prevent them from breaking down faster.
If you are not maintaining your spray gun daily after spraying, you can end up with a lot of issues that can cause you downtime and financial loss, so you want to be sure to keep common spare parts on your spray rig in case of gun failure. Investing in a backup gun in case the parts needed are not on hand is also an ideal way to shorten downtime on a job and reduce problems — especially if you are not already replacing the parts as needed when they are failing. Transfer pump parts are other good spare parts to keep on your spray rig to ensure your system is always running.
5. Follow Service and Maintenance Schedules
Most coating contractors can agree that, due to the nature of their business, regular maintenance on their spray rig is often neglected. Long workdays and demanding schedules can leave contractors having little to no time to perform regular and preventive maintenance on their equipment. Preventive and scheduled maintenance on all equipment is key to keeping the components of your spray system running longer and without failure.
Refer to each equipment manufacturer’s guidelines for maintenance schedules. Equipment suppliers and technicians can also provide you with preventive maintenance to help keep your system up and running. You should always refer to the manufacturers’ schedules for maintenance, but the following sample schedule will give you an idea of what to expect:
- Compressor
– Daily: Check oil levels, clean air/oil external radiator, clean cooler filter, and clean air filter.
– 1,000 hours: See manual. - Air Dryer
– Daily: Check that auto drain is discharging.
– Monthly: Clean debris from ambient air filter, clean with soap and water, and allow it to dry before reinstalling.
– Yearly: Replace separator filter element. - Spray Foam Machine
– Daily: Check pump lubrication level. Refill as needed with throat seal liquid.
– Weekly: Grease circulation valves with appropriate grease. Clean debris out of electrical cabinet vent holes. - Spray Gun
– Daily: Grease gun with appropriate grease, drill mixing chamber, and check valve screens.
– As needed: Clean mixing chamber nozzle by engaging piston safety lock, use correct size drill to clean nozzle, use stiff bristle brush to clean air cap, and clean fluid manifold, impingement parts, and/or passages. - Fresh Air System
– 500 hours: Replace inline outlet filter and inlet filter. - Desiccant
– Daily: Check for color change from blue to pink and replace as necessary.
Conclusion
If you are performing daily checks, following manufacturers’ schedules for servicing your power source component and compressor, properly caring for your hoses, and keeping spare parts on hand, you’ll be able to maintain your plural-component spray equipment at its optimal performance. If you have questions about the maintenance to be performed weekly and annually, reach out to Spray Foam Systems, who can give you guidelines for your equipment setup.
Disqus website name not provided.