Quality Starts At The Top
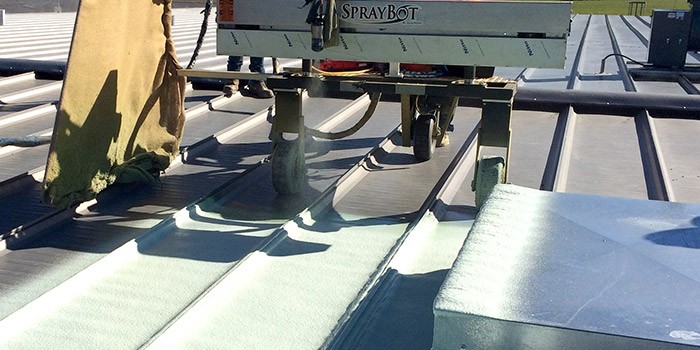
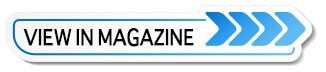
CAZENOVIA, NY – May 3, 2018 – To create a high-quality product, few could argue the notion that conditions surrounding the environment in which said product is crafted, and subsequently housed, need to be optimal. From the workers point of view, if the space inside a factory or building provides comfort, that alone can be conducive to greater function and performance, which is why it behooves the operator to create said comfort, although he or she would like to oblige without suffering great expense on energy bills to balance overhead costs. This is where insulation is vital. But not just any type of insulation will do as it turns out. Take the case of the Marquardt Switches North American headquarters in Cazenovia, NY, which is just south of Lake Ontario and right in the “snow belt” of New York State; an area that receives an average of 140 inches of snow per year.
Marquardt is the leading manufacturer in the field of electro-mechanical and electronic power tool switches and switching systems. Their products are used by many automobile manufacturers and their systems are also found in numerous household appliances and other industrial applications. Their North American headquarters has a robust manufacturing environment that is responsible for the business operation, as well as the design and assembly of electro-mechanical switches and control systems. This location operates 24/7 and employs 500 diverse staff members that cover all aspects of the business’ functions. Unlike many manufacturing facilities, they are required to keep precise temperatures to ensure manufacturing standards for the product they are producing.
The application of foam with the Spraybot was smooth and even against the high metal flute roof.
So, needless to say, insulation there has always been crucial. When the building was being constructed, it received a metal roof that had fiberglass batts installed to its underside. That was the beginning of the problem. Over time, the fiberglass insulation proved to be ineffective as energy bills continued to be increasingly high and ice damming had formed on the roof. It got to the point where Marquardt employees had to go on the roof with snowblowers to remove the snow in the winter, which was downright perilous.
And so, Marquardt researched several ways to provide greater insulation to reduce energy costs and to better control the temperatures inside the building. They determined that it would be impossible to add additional insulation to the underside of the roof deck due to manufacturing equipment already in place, not to mention it would entail a halt in production. Their roof was a three-inch-high metal standing seam roof, limiting the options available to them on the exterior of the building. Traditional roofing methods would have required a board insulation to be mechanically fastened, which would mean that over 35,000 fasteners would penetrate the metal roofing. This was unacceptable by their standards. That’s when a spray polyurethane foam roofing system became the best solution to their problem since it can be spray-applied to the metal without creating penetrations. To tackle the roofing system installation to the 77,500-square-foot roof, Marquardt contracted United Thermal Systems (UTS), a spray foam roofing and insulation specialist based out of Niagara Falls, NY.
The silicone protective coating consisted of a dark grey base coat and a light grey topcoat.
“Spray foam was the only material that could provide a seamless insulation and the R-value they needed,” says UTS’ Vice President Lawrence Ash. “Other roofing systems would require fasteners to penetrate the metal roof and would have created ‘thermal shorts’.”
“Spray foam was the only material that could provide a seamless insulation and the R-value they needed.”
The application consisted of applying two-and-a-half inches of GacoRoofFoam F2733, a 3 lb. roofing foam formulated by Gaco Western. The application, which was carried out by five crewmembers from the UTS team, would provide an R-16.25 value and a robust air and vapor barrier that would eradicate the ice dams on the roof.
“With this system, they don’t have to risk employees getting hurt because the additional insulation eliminates the ice hazards at the roof eaves and, once in place, prevents the ice from forming,” notes Ash.
There were two challenges that made this project distinguishable. The first one was that good old—or not so good in this case—mountain dew. The Marquardt building is located in a valley and every single morning the roof was covered with a layer of dew that had to be blown off by the UTS crew by way of backpack and leaf blowers to make sure the surface was dry enough to spray and coat.
The second challenge consisted of figuring out how to spray a smooth surface to the high metal flute. The UTS crew determined that spray-applying by hand would have produced uneven results, so they turned to innovation and acquired SprayWorks’ Spraybot, an automated spray machine.
“Metal roofs are inherently challenging, which is not your everyday roof for spray foam,” explains SprayWorks’ John Davidson. “When working on commercial roofs at a slope less than 9.5 degrees or 2:12 - the Spraybot provides an ideal consistent spray. UTS was able to more accurately estimate their job, given that the yield typically increases by 10 percent or more and material application becomes even and consistent with the Spraybot - essentially laser printing spray foam to the metal.”
The completed spray foam roof system will have a significant impact on the building’s energy usage and cost.
The crew hooked the Spraybot to their Graco Reactor H-40 proportioner and Graco Probler P2 spray gun and set it to spray the 65,000 pounds of foam to the flat surface at two-and-a-half inches. According to Ash, the robotic machine sprayed the foam in a perfect horizontal pattern, which prevented rollover of the foam at the top of the flute, and he added that the Spraybot’s attached stabilized windscreen provided significant overspray damage protection.
“Since there were over 300 vehicles parked at the facility, this was a major concern that the robot’s windscreen relieved,” says Ash. “The Spraybot allowed for a smooth and consistently even spray surface, maintaining an aesthetic and uniform look. Hand spraying the foam would have
been difficult to seal the top inch high-standing seam rib.”
Additional foam windscreens were held by the crewmembers to prevent overspray migration to the surrounding parking lots. The UTS team applied foam by hand to the roof edging, skylights, HVAC units, and existing penetrations to provide crickets for any water that got on the roof to disperse properly.
Then, using a Graco Xtreme 45:1 airless spray pump and a Titan coating gun with a .031 tip, the crew installed 24 mils of Gaco Western’s GacoRoof silicone coating in two coats – a grey dark base and a light grey topcoat. Finally, the UTS crew finished off the roofing system by embedding 3M Classic dense, non-porous, and UV-resistant ceramic granules in the wet topcoat with a Clemco Granule Pot.
During the application, the crewmembers wore PPE that included respirators, safety glasses, spray suits, and protective gloves during the foam and coating application. The crew set up perimeter flagging around the edges of the roof and wore safety harnesses tied to anchors for fall protection when working around the edges, both during the roofing system installation and when raising and lowering equipment/supplies to the roof. Toolbox talks that pertained to the project were held every morning prior to the start of work. UTS also had a safety consultant, an ex OSHA inspector, inspected the site on several occasions to ensure that OSHA standards and all safety rules were being adhered to. A copy of the report (as well as pictures documenting safety precautions) was provided to Marquardt for assurance that safety was paramount to a successful roofing operation. Upon completion, the roof received an inspection by Gaco Western and slit samples, as well as core samples, were taken to ensure thickness compliance required for warranty issuance.
According to Ash, when a portion of the roof was completed over one of the production areas, the owner received notification from the employees that the HVAC system was now making their working environment too cold. The facility’s manager had to adjust the cooling to raise the temperature. This reflects a major reduction of their HVAC system costs to cooling the plant in the summer and heating in the winters.
“The owner determined that they were saving over 30 kilowatts of energy per HVAC unit due to the new foam roofing installed which translates into major energy cost savings,” notes Ash.
The crew completed the roofing application within 48 working days. The energy costs are down and come winter, there will be no ice dams forming on this roof. Due to the energy cost savings being enjoyed at the facility, the owners are considering the same application for their Massachusetts and Mexico plants. All in all, spray foam continues to demonstrate that its sustainable properties can improve the performance of buildings and even better yet, the performance of those who work inside of them.
For more information, visit www.unitedthermalsystems.com, www.sprayworksequipment.com, and www.gacowestern.com.
Disqus website name not provided.