Redesigning To Improve the Customer’s Bottom Line
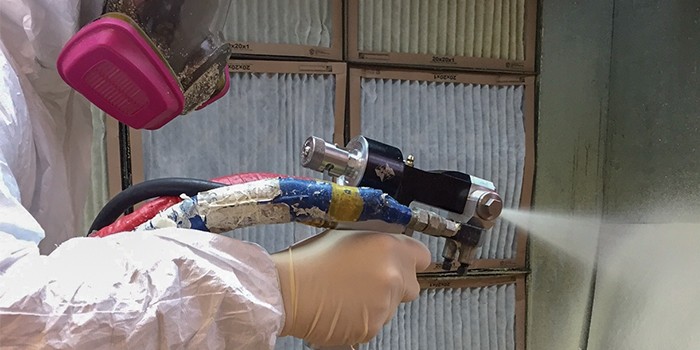
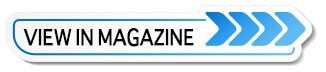
LAKEWOOD, NJ – May 3, 2018 – The spray foam and polyurea coatings industries both rely on highly reactive chemistry that is demanding on the equipment. The two-component materials need to be correctly metered, pressurized and heated when they arrive at the spray gun where they are impingement mixed and dispensed on the substrate. At temperatures of up to 190°F/88°C and pressures up to 3,500 psi/242 BAR, the parts in the spray gun are put to an extreme test with each pull of the trigger.
Equipment has been refined and improved over time, but the same concept of impingement mix, air purge spray gun technology that was introduced in 1974 is still being used. Why? Because impingement mixing with air purge works and is reliable. The spray guns facilitate training, and typically cost less to maintain than a mechanical purge gun, the only other option for these materials.
When designing the next generation of air-purge spray gun, PMC communicated with their customers and distributors, receiving input for over a year before the prototypes were commissioned. The result achieved is a collaboration between PMC, their distributors and end users, focusing on two key elements: Designing to improve the customer’s bottom line and ease of maintenance. It was important to use the already proven technology of the AP-2, and improve it where possible. PMC’s equipment is made in the United States and maintains a high level of quality as a specialist in plural-component spray equipment. The high-quality standards of PMC were challenged to go to the next level in this design. The key design requests and considerations culminating in the new AP-3 spray gun design are noted below.
Same Heart, New Coating: The AP-3 uses the same mixing chamber, pattern control tip, and side-screen seal assemblies as the proven AP-2. PMC has added a new proprietary coating that resists material bonding to the spray tip and mixing chamber better than ever before. The side seal screens still filter from the outside, allowing fast cleaning and replacing. This small design point makes a difference when compared with competitive spray guns that filter from the inside of a screen basket, resulting in material buildup that can’t be cleaned effectively and drastically increases parts consumption and operating cost. Customers with multiple AP-2 guns are able to use their existing parts inventory in the new AP-3 guns, making the transition cost-effective.
The AP-3 is equipped with a new proprietary coating that resists material bonding to the spray tip and mixing chamber, a responsive trigger with a lightning fast piston that provides control over detail work, and a new trigger cartridge design for quickness and reliability
Operator Ergonomics: Material hoses can be routed out of the back or down the front of the gun depending on the job requirements. The air hose can also be plumbed out of the back of the gun or through the handle base.
Responsive Trigger and New Trigger Cartridge Design: The lightning fast piston gives control over detail work and develops a spray pattern immediately while reducing operator fatigue. The new trigger cartridge is quick and reliable.
Fewer Parts: The AP-3 has a streamlined bridge and new trigger cartridge design that results in 20 percent fewer gun parts. The bridge allows better trigger clearance when the hoses are routed downward. The simple trigger cartridge valve is quick to change when needed and lowers the spare parts cost.
As a specialist in equipment design and manufacture for the polyurethane foam and polyurea/polyurethane fast-set coatings industry, PMC focuses on the customers’ requirements to envision and bring to life products that will improve their bottom line by being the best combination of high quality and low cost achievable. The Engineering, R&D, and Sales teams all brought distributor and customer input to the design table and this input resulted in the new AP-3 spray gun. Many customers have already cut their spare parts cost in half with the current AP-2 spray gun. The continued focus on fewer, high-quality parts at an affordable price for the AP-3 spray gun will be evidenced by further savings for operators and end users through effectively decreasing their operating costs and increasing the bottom line.
Disqus website name not provided.