Restoring History
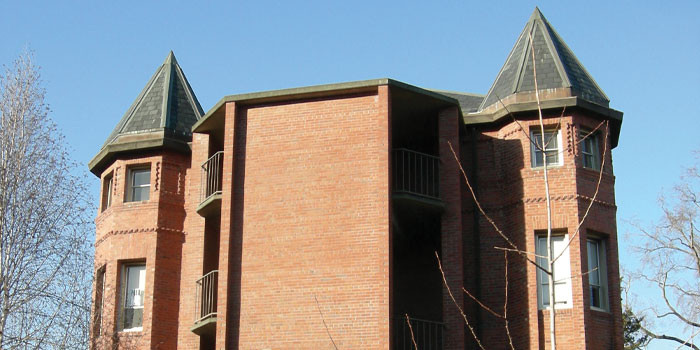
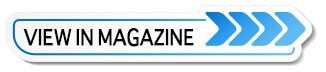
Summer 2020 – Spray Foam Magazine – Seattle Pacific University needed to bring their Alexander Hall building up to today’s seismic standards, but after analyzing the building’s original unreinforced masonry construction and the wear and tear of 121 years, the engineers concluded that Alexander Hall represented a potential safety risk. The faculty and staff were immediately relocated to another facility and planning began for a major seismic retrofit and interior renovation.
The president of NGS, Inc. (National Grouting Systems), Dave Morell, is based in Seattle, and specializes in pressure grouting (injecting a grout material into an otherwise inaccessible but interconnected pore or void space). Morell received a call from Absher construction who were contracted to upgrade the Alexander Hall. This hall was the first building on the SPU campus and it originally held the entire school, thought to be one the oldest brick structures in Seattle.1
When the structure was being assessed, they found the three-story high building was heated by coal in the 1800s. There were 12 coal ovens in the basement, which ran 12 chimneys up through the building, venting through the roof. The mortar on the outside of the building was a good grade, but once the interior furring was stripped off, the construction team found the chimney’s mortar was crumbling and many joints were missing.
This is when Morell was contacted by the construction team. They wanted him to grout the chimneys to make sure the integrity of the mortar holding the brick together stayed intact. Due to the voids between the bricks where the mortar had crumbled, this project was going to be a challenge. Morell recalls, “I met on site with both Absher and an engineer from Pacific Engineering Technologies Incorporated. I looked at the project and realized there was just no way the grout was going to work, due to the logistics. It was on a college campus with very little exterior access and there were no elevators. It would have to be pumped, and in small lifts.”
The 12 chimneys were roughly 60 feet tall, and it would take a long time to complete the restoration with the grouting method. The construction and engineering teams asked Morell how else they could solve the issue. “Fortunately, we had done a previous job for Pacific Engineering on a shoreline restoration project, and we had injected foam underneath the asphalt to consolidate the voids. It worked very well, and we basically exchanged the grout for the foam. After recalling that project, we decided to use foam for the chimneys.”
The architect however, wanted testing to convince him the foam would be a great alternative. Morell emphasized, “One of the challenges you have with the architects is they try to compare cementitious psi, to foam psi. You have a grout that’s 4,000 psi and then a foam that’s 300-400 psi. They throw up their arms and think there is just no way that will work. A testing protocol was put together comparing the differences of materials and the benefits of foam. Pacific Engineering liked the idea of foam and knew it was the only way to do the project.
Morell emphasized that a lot of testing was carried out at SPI to see how high they could go on lifts. They had just come out with a new system of blowing foam long distances before it expanded, which also helped with the application. All of these positive effects and the result of testing convinced the architect to approve the use of foam.
Morell and one more crew member were enthusiastic to take on the challenge of stabilizing the 12 unused brick chimneys, which would help convert the space into offices for the university. The bricks were removed at 8-foot-high intervals to install metal rods and plates as part of the retrofit upgrade. Holes were drilled in the bricks of the chimneys to allow for SPI’s Synergy Series Envelo-Pour Polyurethane 4.5-pound Rigid Pour Foam to be injected into the three-foot lifts, with the crew working on the interior one floor at a time. This foam’s density is a two component, rigid polyurethane system for pour foam applications with a low viscosity specifically designed for pour operations. It helped fill the voids in the chimneys on this project, in addition to filling the coal oven in the basement.
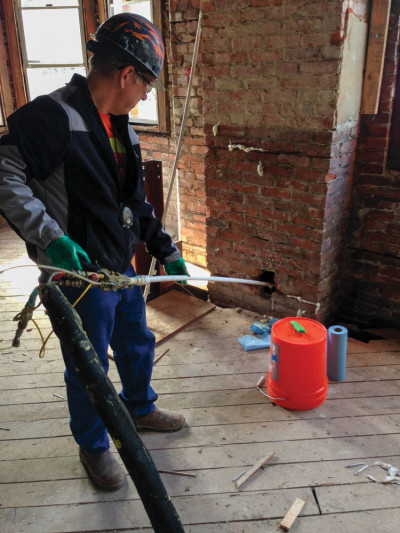
SPI’s Envelo-Pour Foam was injected into the chimney using the innovative SPI LPG™ Proportioner System filling the cavity with 540 gallons of foam.
The crew used a LPGTM proportioner to inject the foam, which Morell noted “We had to carry all of the equipment up scaffolding so the mobility of this portable, lightweight (~50 pounds), low pressure proportioner was ideal for this job.” Once cured, the rigid foam strengthened and stabilized the unused chimney, while still preserving its historic authenticity. The project took a total of five days, using 540 gallons of foam.
The architect, engineers and Morell’s crew were impressed and very happy with the result. The advantages of the foam being lightweight and flexible also helped stabilize the chimneys in the event of an earthquake/seismic activity. In 2001, Seattle had suffered from a 6.8 magnitude earthquake and that was one of the engineer’s concerns, leading to the specifications on this particular part of the restoration. If the chimneys had been filled with grout, it wouldn’t have allowed for any lateral movement. The building had previously been left empty for roughly two decades and with the help of foam, it has a new lease on life while keeping its historical features.
1 Known only as the “Red Brick Building” in its early years, Alexander Hall was constructed on a rugged five-acre plot of land on the northern side of Queen Anne Hill. Designed in the Romanesque Revival style by prominent Seattle architect John Parkinson, the building had four narrow towers, a slate roof, gutters and finials of galvanized iron, a large central Romanesque entry archway, and an interior made of native woods. In October 1940, the building was officially named Alexander Hall, after SPU’s first president, Alexander Beers.
Disqus website name not provided.