SPF VS. Fiberglass & Cellulose
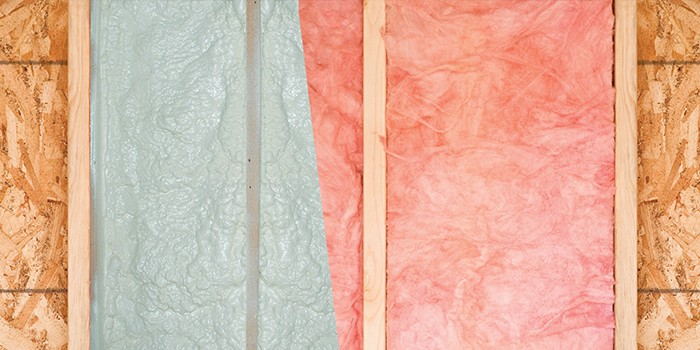
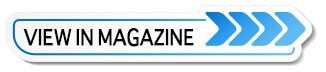
JUPITER, FL – May 3, 2018 – With various insulation options available to your customers, it can often be difficult for them to make a buying decision. To help that process, let’s run through the facts and fallacies of insulation.
FALLACY #1: R-value is all that matters, so all insulations, at the same R-value, have the same performance.
FACT: All insulations do not perform the same, because R-value is only one component of overall thermal performance.
R-value alone does not tell the whole story.
The problem is that R-value only measures one form of thermal transmission, conduction; these values do not address convection (heat transfer by air movement) or radiation (heat waves).
You see, there are three forms of heat transfer—convection, conduction, and radiation.
Convection is how heat travels in moving currents through liquids or gases, such as how heat moves in air or in boiling water.
Conduction is how heat travels through solids. For example, if we place a metal spoon in a cup of coffee, the spoon will heat up. Likewise, heat moves through studs from the hot side of the wall to the cooler side of the wall via conduction.
Radiation is how heat transfers through empty space by electromagnetic waves. This is how the heat from the sun travels to the earth and is why you feel heat “radiating” off of your car windshield.
Also, while there are three forms of heat transfer, R-value of an insulation can be derated based on poor application. Insulation is designed to be installed so that it is in contact with an air barrier. So, if fiberglass or cellulose insulation is not installed properly—is not uniform and has gaps and voids—it can be derated.
FALLACY #2: I “need” R-13 in the walls and R-38 in the attic in Climate Zone 3 to meet energy code (this applies to the prescribed R-values in your climate zone too).
FACT: The energy code offers multiple methods for compliance: The prescriptive path, the performance path, and the energy rating index.
While the energy code in Climate Zone 3 might prescribe R-13 for the walls and R-38 for the attic, that is not the only way to meet energy code compliance, especially when using a high-performance material like spray foam insulation.
The second compliance method, the performance path, requires the proposed building design to be shown to have an annual energy cost that is less than or equal to the annual energy cost of the standard reference design, which is generally a building that meets the minimum prescriptive code requirements. So, how is this calculated?
This type of energy performance calculation is typically conducted using energy modeling software, such as REScheck™ or EnergyPro. These software systems must produce a compliance report showing the proposed design outperforms the standard reference design. Think about it this way – when the proposed design, let’s call it Building A, is analyzed for annual energy consumption, the compliance software must show that it will use less energy than Building B, the reference design, built to the minimum prescriptive code requirements.
And the third compliance method for residential projects is the Energy Rating Index, or ERI. It is a calculated number on a linear index scale constructed with the ERI reference design, which shall meet the minimum requirements of the 2006 IECC prescriptive requirements. A one percent change in the total energy use of the rated design relative to the total energy use of the ERI reference design shall be represented by a change of 1 on the index scale. So, an ERI of 55 means that the proposed design outperforms the ERI reference design by 45 percent. To qualify for ERI compliance, the maximum energy rating index, allowable by climate zone, is identified in IRC Table 1106.4:
For example, in Climate Zone 3, like Dallas, TX, to qualify for ERI compliance, the building would have an energy rating index of 51. This means that the building would use 49 percent less energy than the 2006 IECC code minimum for the same building.
Finally, a report that shows the proposed design meets the requirements of the ERI is required using energy calculations from an energy modeling software tool.
The ERI compliance method is new to the 2015 code and offers another way to provide compliance when building high-performance systems.
So, how do these performance-based, energy code-compliance methods benefit you?
Well, you know that spray foam works exceptionally well, so you may have wondered why the traditional code does not give you “credit” for the benefits of spray foam. Well, the performance-based and ERI code compliance paths will. Using energy code compliance software, you can get credit for air-tightness of the building envelope, moving ductwork into conditioned space, having zero duct losses to the exterior, and other benefits. All of this adds up to improved performance that can be documented and proven for code compliance.
FALLACY #3: Spray foam is too expensive
FACT: Spray foam insulation is the only upgrade that will not only pay for itself but will also pay for other upgrades in the building.
Now, like me, you probably know that this is a super short-sighted point of view, right?
It would be like saying an automobile is more expensive than a horse. In the early days of cars, I am sure many people thought this as they continued to rely on horses, but you never hear that argument today. Why? They both provide transportation, but cars are more effective, more efficient, and have lower operating cost than horses.
So, let’s look at the big picture.
Insulation is designed to be in contact with an air barrier, so if it is applied improperly, the R-value of the insulation can be derated.
Spray foam, fiberglass, and cellulose all provide thermal insulation, but spray foam is both more effective and more efficient. Yes, spray foam is going to cost more than traditional insulation upfront, but high-performance machines always do! Because spray foam building envelopes are more effective and more efficient, the standard payback period for both open-cell and closed-cell foam in all climate zones is less than five years. That’s more than a 20 percent ROI. Where else are you making 20 percent on your money?
Finally, when mechanical systems are properly sized and designed, based on the building envelope package, using spray foam insulation can reduce the size of the mechanical system. This means the mechanical system will typically cost less upfront, resulting in an initial cost offset. Add this up and you will quickly realize that spray foam is the only upgrade that will not only pay for itself, but it can also buy you granite countertops.
With these concepts in mind, like relying on a horse for transportation, traditional insulation will cost you more in the long run. So, if you ask me, it is too expensive not to use spray foam. Separating the facts from the fallacies is where the rubber meets the road for your customers. It will help them make more informed decisions and help you close more sales, so share this information with your team and your customers.
Disqus website name not provided.