Spray Foam Insulation Saving Lives & Billions of Dollars in Iraq & Afghanistan
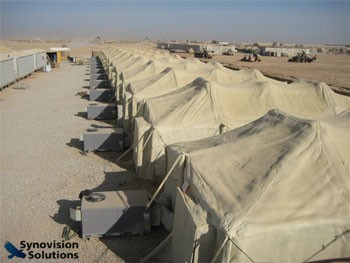
In early 2007, a major problem became increasingly more evident to US military officials in Iraq: Fuel trucks were being targeted by Iraqi insurgents and, as a result, the soldiers and contractors driving these trucks were being killed at alarming rates. At the time, there were about 1,000 US military trucks delivering critical supplies from Kuwait, Jordan and Turkey into Iraq every day, with about 250 of those being fuel trucks. Steven M. Anderson, retired Brigadier General in the US Army and current COO of Synovision Solutions LLC, who was serving under General David Petraeus, says that the question arose, “What can be done to reduce the number of trucks on the road?”
Anderson created a task force to investigate the problem and determine a solution. The expert transportation team, led by Army COL Mary Whitworth and Navy Captain Mike Zabel, discovered that about 80% of those fuel trucks were carrying fuel specifically for generators powering air conditioning units at non-insulated structures such as tents, trailers and buildings built with sheet metal and plywood. The Army’s Rapid Equipping Force (REF) was brought in to analyze the situation. The REF came up with an assortment of alternative energy sources such as solar, wind and geothermal as possible solutions in order to reduce the fuel requirement at these locations. However, most of the proposed solutions would have taken at least two years to implement. BG Anderson then instructed the task force to find a more immediate solution.
Joe Amadee, VP of Operations at Synovision Solutions, was the first to come up with the idea of applying closed cell spray polyurethane foam to the exterior of Army tents for insulation. Amadee had read about spray foam’s proven effectiveness as an insulator and was convinced it would be a viable solution to the problem at hand. He convinced the Army to let him conduct a test on a tent at Fort Benning in Georgia using Gaco Western 193 foam. Exceeding even Amadee’s expectations, the test demonstrated a stunning 92% reduction in the electrical energy needed to cool the structure in the hot Georgia sun.
To determine the effectiveness of this solution in a combat zone such as Iraq, Anderson asked Amadee and Synovision Solutions, a provider of “project leadership and strategic technology development services,” to conduct an initial test at Camp Victory in Baghdad, Iraq. They applied closed cell spray foam insulation to one of the many inefficient buildings at the base, a large gymnasium. Prior to the spray foam application, officials at the base had never been able to reduce the temperature in the gym any lower than 92 degrees Fahrenheit with eight air conditioners running at full power. After spraying the facility with spray foam, the temperature was decreased to 70 degrees with only two air conditioning units. “Our troops were finally able to use the gym in comfort and we only had to use a fraction of the energy to keep it at that temperature. One walk through the facility and we knew Joe had brought us a real winner,” says Anderson.
Since the test, the US Army has funded numerous contracts through three main applicators: Synovision, Honeywell and Critical Mission Support Services (CMSS). Over the past three years, over 12 million square feet of spray foam has been used to insulate military structures in Iraq and Afghanistan, and the effort has been tremendously successful everywhere it has been applied. In fact, one of Honeywell’s subcontractors, West Roofing Systems Inc. of LaGrange, OH, was recently presented an award from the Spray Polyurethane Foam Alliance for their work on the project.
In the summer of 2009, the US Army Materiel Systems Analysis Activity (AMSAA) was commissioned by the Army Deputy Chief of Staff for Logistics to conduct a study with the goal of quantifying the overall benefit of the project. “This study confirmed what those familiar with the project knew intuitively to be true – and could now prove.” It was concluded that almost $1 billion is being saved annually due to the increased energy efficiency from the spray foam. More importantly, the study concluded that thousands of fuel trucks are being taken off the most dangerous roads in the world. This, in turn, has saved countless lives. “Synovision CEO Dr. Bruce Jette is fond of saying that the best way to beat an IED,” says Anderson, “is to not be there in the first place. Spray foam removes targets from our enemy’s crosshairs.”
The AMSAA study also determined that based on these cost savings, spray foam insulation applied on a typical structure in Iraq pays for itself within 75 days. Additionally, AMSAA found that the spray foam insulation improves the air quality in these buildings, especially the tents, by cutting down on the dust that gets through the walls and thus makes the buildings healthier for their occupants. It also provides a moisture barrier impervious to mold. Another benefit provided by the spray foam is that it creates a sound barrier. This is a tremendous benefit in Iraq where it is very difficult for soldiers to sleep due to the loud environment. The spray foam also provides a fire barrier, which has reduced the spread of fires through the camps.
Despite the increased use of spray foam overseas in support of our military efforts, the AMSAA study showed that a far more comprehensive spray foam program is required. As the US involvement in Iraq winds down and our military efforts are shifted to Afghanistan, Anderson explains that there are multiple reasons why it is even more important to utilize spray foam to insulate the structures in that country. First, Afghanistan is a very poorly developed area without adequate trucking routes, making it extremely difficult to deliver fuel to our bases there. Certain areas are so isolated that fuel must be flown in by helicopter. Although, on average, fuel costs the US military about $2.15 a gallon, the “true” cost of fuel is determined by factoring all associated costs including transportation. In Iraq, this cost is about $13.80 per gallon, but in Afghanistan it is at least double that price. That means that spray foam insulation would pay for itself in half the time that it does in Iraq. In areas where fuel must be delivered by helicopter, the true cost of fuel can be upwards of $400 per gallon. In these areas, spray foam would pay for itself in a couple weeks.
Anderson points out, “As spray foam reduces our fuel requirements in Iraq and Afghanistan, the possibility of renewable energy sources such as solar, wind and geothermal are empowered; they can finally make a significant impact. The more self sufficient we can be over there and the fewer fuel trucks on the road, the better. Spray foam is a true ‘no-brainer’ and a win-win for both our soldiers and US taxpayers.”
Disqus website name not provided.