Spray Foam Insulation Used on a Modular Home Project
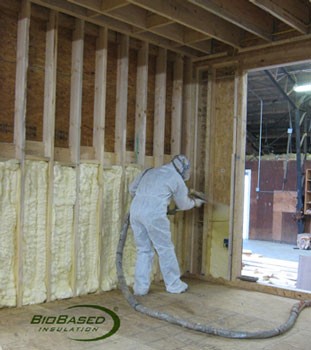
FAYETTEVILLE, Arkansas (May 21, 2010) – When Natural State Insulation was approached by a local architecture professor about a project he was working on with his PreFab Landscapes class, they knew they wanted to be part of it.
The project involved 15 fourth and fifth year architecture students designing then constructing in a Fayetteville warehouse the modules to make a modular home. Then they had to transport the four modules 200 miles to Little Rock where they were assembled on site in a neighborhood ripe for redevelopment.
A local family was able to purchase the energy-efficient home well-below market value, and the students received a grade for their work on the year-long project.
“A project like this doesn’t come around often,” said Cam Shafer, general manager of Natural State Insulation, a BioBased Insulation® Certified Dealer. “We were most excited about this, because it was an opportunity to demonstrate the energy-efficient benefits of spray foam insulation and to introduce a new generation of architects to the product. The chance to help a family and a community just made it better.”
The brain child of Michael Hughes, associate professor at the University of Arkansas’ Fay Jones School of Architecture, the project is the result of a partnership with the Downtown Little Rock Community Development Corporation.
The non-profit is focused on community revitalization, so they identified a neighborhood and a qualifying family and secured the lot for the home. The Pettaway Park neighborhood in central Little Rock was chosen because it was hit hard by a tornado in 1999 and is still recovering. This is the first of several homes planned as part of the partnership and neighborhood redevelopment efforts.
Students spent the 2009 fall semester working with their clients, the future homeowners, and meeting with community groups and mentors to design a home that would meet the couple’s needs and also serve as a model for sustainable and affordable housing.
In their design, the students had planned and budgeted to use traditional insulation for the project. But Shafer agreed to discount BioBased 501® insulation, a .5 lb open cell spray foam insulation, so they could use it in the project.
When it was being installed, most of the students donned respirators so they could watch the process. In order to help the students understand spray foam, Shafer took the time to stop and explain the installation process, give tours of the spray rig and answer questions.
“Giving the family an energy-efficient home and allowing these students to design using spray foam insulation was worth it,” Shafer said. “These are some of the architects who will be designing projects in the future.
“It’s important for them to understand the benefits of spray foam insulation and how the different systems in the house work together and impact each other. We know from experience that if people see spray foam installed and understand the building science behind it, then they are sold on it.”
Spray foam insulation seals and insulates in one step, which helps to reduce air infiltration. That means that homeowners can typically uses less energy for heating and cooling, giving them a smaller carbon footprint and reducing their utility bills. Sealing a building with spray foam insulation also helps maintain uniform temperatures throughout so that the building is more comfortable.
BioBased Insulation®, a product of Arkansas-based BioBased Technologies®, is applied using water as the blowing agent instead of a chemical blowing agent, and it integrates renewable ingredients to replace a portion of the petroleum that’s used in the product.
The spray foam insulation fit in with other energy-efficient features the students had planned for the home including a large recessed front porch that offers plenty of shade, energy-efficient appliances, a tankless water heater, and concrete kitchen and bathroom counters. Attention also was paid to the solar orientation, providing daylight and opportunities for cross ventilation.
Because of companies like Natural State Insulation who discounted their services and the students who donated their design and construction work, the 1,200-square-foot, two-bedroom, one-bath home was made available at a deep discount for the homeowners. A similar home might cost $180,000, but this one was sold for $109,500.
Hughes believes that this type of full-scale experience is an important component to design education, because it forces the students to think about things not typically addressed in a traditional design studio that is focused on conceptual development and disciplinary skills.
“Very often, students build these models, and they look at them like they’re flying over them from a bird’s eye view,” Hughes said. “So they’re making all these shapes or changes to the overall volume without ever conceiving of what it feels like to be inside those spaces. By focusing all the way down to the details, the students saw how all the systems work together and are interrelated.”
Hughes said the students’ knowledge from this project would flow back into how they design in the future. Now that they have seen their design realized and made it happen with their own hands, they’ll never design the same way again.
“It would be hard to imagine them just starting back from the 20,000-feet-above-sea-level kind of view without thinking about these kinds of detailed conditions and what the building feels like, to be in it, in a tactile way,” Hughes said.
About BioBased Insulation®
BioBased Insulation® and the Agrol® family of bio-based polyols are manufactured by BioBased Technologies®. The company is focused on developing and bringing to market safe products that strive to reduce the use of non-renewable resources by integrating renewable ingredients or by improving energy efficiency.
Disqus website name not provided.