Spray Guns Galore!
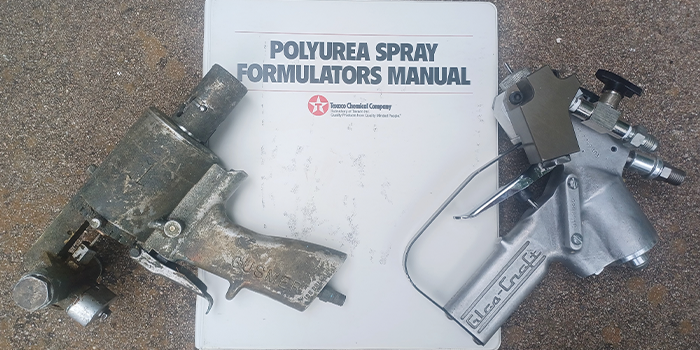
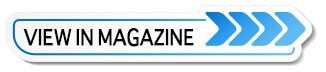
Spray Foam Magazine – Picking up from the last article in Spray Foam Magazine, there is always some “Method to One’s Madness” if you will. Usually after discussing in general all the parts to a set-up, one would logically start from the beginning of the process. However, for this article, we will start with the end of the process. Why you might ask? Well, that’s simple. Based upon a recent posting on a prominent social media site, it is appropriate that we start with the spray guns for this segment.
Recently, there was a post about using a particular spray gun setup for application of a rigid spray foam system, and it was having some issues. It was noted that they were using an air purge gun, configured with a “7070” mix chamber, and having trouble keeping the heats up and good spray. When asked about the proportioner, they were using an electric version, suited only for about one and a half gallons/min (~12 lbs/min) output. So that “7070” chamber is designed for quality output of four gallon/min (~35 lbs/min), such that they were exceeding considerably the output capacity of the spray unit. When noted to use a smaller chamber, they did not want to reduce their production rate; what??? Well using a larger chamber is not going to make your proportioner provide more output that it is designed to produce. Good thing they were not trying that with a quality polyurea system. That would have been a complete mess.
So the one million dollar question here is: which is the best spray gun for polyurea spray application work? Unfortunately, there is no simple answer, as it can depend upon many factors related to the specific application and the quality of the polyurea coating produced. As noted in the previous article, downsizing to the end is very important. Again, meaning having more flow output capability at the start (material supply and proportioner), thus controlling output (reducing) at the end – spray gun.
Polyurea Spray Gun History
To put things in perspective here, we need to go back a little more than 35 years ago when the polyurea spray technology was first developed and demonstrated. For all of the development work prior to introduction of the technology to the world, a common mechanical purge spray gun was used. The use of the mechanical purge was akin to the RIM (Reaction Injection Molding) heads used for polyurea RIM work in the automotive industry. This setup proved to provide the best mixing and processing of this fast set technology. Shortly after the development work, a new type spray gun was introduced, the air purge spray gun.
This particular air purge gun used did in fact “spray” material. While the material processed did setup and cure, the resulting properties were significantly different than the same material processed using the mechanical purge gun. This is explained in the following “Elastomer Physical Properties” table.
Interesting results were found here for the same system. While all three sprays did make a polyurea that set and “got hard,” the significant difference in properties would have resulted in significant differences in overall performance. Because of these continued results and experiences, the primary gun used in all the development was a mechanical purge spray gun.
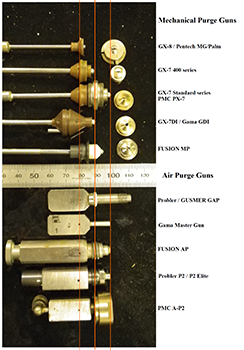
One important factor that was noted early on in the development with polyurea system processing is the mix chamber with multiple ports for ISO and Resin Side, which provided a more turbulent mix than the one with only one port for the ISO and Resin side. This has been demonstrated many times and is shown in the resulting physical property comparisons.
Spray Guns
For polyurea spray work, this is a very fast setting, plural component technology. The mixing of the two-components must occur inside the confines of the small mix chamber within the spray gun, and exit out as quickly as possible. Unlike plural component, airless spray systems, where the two parts are mixed via a mix manifold with static mixers before flowing to the spray gun, the mix in the chamber is very short, but very important. For fast set polyurea systems, the reaction starts immediately when the two components come together, thus forming a polymer and building viscosity. This must be overcome with the proper spray gun setup, as well as proper processing pressure and heat.
There are a vast variety of spray guns now used in polyurea spray work, which includes both mechanical and air purge operations. There are way too many setups to note here, so we will just stick with the nomenclature of mechanical purge versus air purge. Both types do work, but each must be setup properly for the type of system being used. We are not spraying polyurethane foam here, so the reaction profile is completely different.
An earlier notation relating to processing and the spray gun setup, discussed the concept of the material entering the mix chamber, mixing and then exiting as quickly as possible. The longer the material stays in the mix chamber, the more the reaction has progressed, building viscosity due to polymer formation. This can in fact affect the overall mix as well as the resulting spray pattern.
To illustrate this, take a look at the picture above. This picture has been used many times. Some may understand what it is, but some think it is just showing the various mix chambers. What is important to note here is the length of the mix chamber from material entry port to when material exits the end.
There have been many studies related to Reynolds Number and flow / mixing with polyurea systems, but the basic idea here is to have the entry ports properly sized related to the volume of the mix chamber, taking into account the chamber length. This is why only certain mix chambers work properly with polyurea systems and provide the optimum mix, NOT just spraying, thus achieving the reported physical properties, appearance and performance.
In the automotive RIM industry, polyurea systems are “injected” using a mix technique very similar to the impingement mix, free flow guns. However, an “after-mixer” is incorporated in the mold just after the impingement mix head to complete the mix of the system before introduction into the mold. Otherwise, poor mixing is noted and you have bad part production.
It is sometimes noted that the air purge guns may have less overspray than the more conventional mechanical purge spray guns. This is only true when using the chambers that are designed to give a round pattern that have no additional controlling tip on the front of the tube. However, lack of this controlling tip does not allow for the required back pressure in the mixing chamber and can result in incomplete mix of the fast setting polyurea spray elastomer systems. This “free-flow” of material does not break-up and atomize the system completely, thus possibly resulting in poor mix / off-ratio problems. As noted though, in the previous article, there are some air purge guns that simulate the mechanical purge / tip combination with the special “insert.”
Did this just state that mechanical purge guns are better than air purge guns??? NO!!!
All of these types of spray guns will work, provided they are properly set up and maintained. You just need to confirm the setup is appropriate for the system being processed. If you are one that does quite a bit of triggering and using an air purge gun, you will be cleaning the bore of the mix chamber more often than one that minimizes triggering.
Confirmation of Proper Mix
The best way to tell if one has achieved proper mix with the spray gun setup being used, is to test the physical properties of the produced elastomer system. And unlike many spray foam application projects, typical specifications on polyurea work call for preparing spray retain samples on the project and sending those back to either the system supplier or third party testing lab for confirmation. This is why it is important to follow the guidance of the polyurea system supplier for the spray gun setup for their system, and not really on what equipment manufacturers may say, or what one might hear on social media posts.
While physical testing equipment is usually not part of a spray equipment setup, there are some simple tests and observations that can be done in the field to help confirm that one is achieving proper mix. These would include:
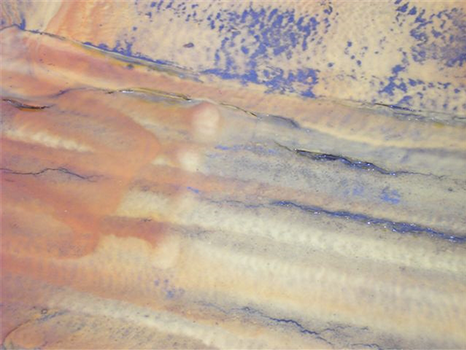
Four streams spray pattern.
Observation of spray pressures during processing
– Use of flow meters can be beneficial for insuring ratio; however, they have no indication of proper mix in the spray gun
Visual observance of a full, atomized spray pattern (NO fingers / streams)
– Many posts on social media spraying with “fingered” spray pattern and may think all is good
Achieving the noted Gel / Tack Free times on the product TDS
– Should be with parameters listed on product TDS
Field measurement of Shore Hardness of produced material (ASTM D 22240)
– After about 1 hours of application, should be with 10% of that noted on product TDS
– Tested area shall be min of 60 mils (1.5 mm) DFT
The above points are discussed as part of industry standards on polyurea work.
As noted earlier, there is no “one best spray gun for polyurea,” and use usually comes via preference by the user or the equipment supplier. However, the gun should not be chosen just because it feels comfortable in the hand, but what setup is going to provide the best mix for the system and the application work. Remember, the person holding the spray gun is the one actually making the “polyurea,” not the material supplier. It is not just about spraying something coming out the end of the gun, but what provides the required mix for the resulting properties of the project and expected performance.
But most importantly with the spray gun, the output capacity of the spray gun should NOT exceed the output capacity of the proportioning unit. The gun needs to be sized to the capability of the proportioner. It’s all about flow… This is what should be restricting the material flow, not any of the previous parts of the processing system. For example, if the maximum output for your proportioner is two gals/min as published, don’t use a “5252” chamber for example. In this case, max should be a “4242.”
While the question of “which is the best” may not have been directly answered here, enough information has been provided for a proper choice for the application work. Many large contractors may in fact have more than one type of spray gun, and its use is dictated by the specific system and type of application project. I personally have my preference, which is based upon proper mix, properties achieved and aesthetics.
For use by SprayFoamMagazine.com & Spray Foam Magazine
Disqus website name not provided.