Spray Polyurethane Foam Insulation Alleviates Commercial Factory's Condensation Issues
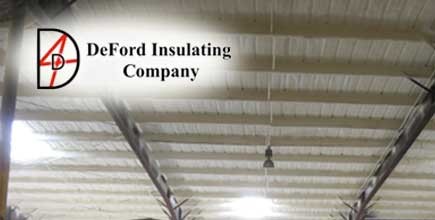
WEBSTER CITY, IA – August 13, 2013 – Condensation can be a significant burden when operating a pallet-making business. Because freshly cut lumber is known to release 30 to 50 percent of its moisture, roof systems that accumulate condensation can cause water to drip down into a building. This was a daily problem at the headquarters of Tasler Inc, a wood pallet manufacturing company. The 400 foot square steel building with 20 foot walls had recurring condensation issues on its existing fiberglass ceiling insulation, which caused moisture to permeate through the insulation and into the factory. Not only could moisture hasten the eventual rotting of the roof system, but water droplets would turn into piles of ice during the Iowa winter, which would make life hard on workers driving forklifts and manufacturing the pallets. Since their facility housed all of Tasler's pallet production, the owners became concerned that if they didn't fix their condensation problem, they could be facing severe downtime while their pallets sustained potential molding damage. The owners decided to remove their fiberglass system and install spray polyurethane foam in order to seal their building from any condensation.
Doug Jacobsen, manager of Tasler Inc, pointed out that keeping the lumber dry was of the utmost importance to be able to manufacture their trademark shipping pallets.
"The fresh cut lumber increases the humidity of the building by 90 percent," said Jacobsen. "We have to keep the wood dry in order to avoid further issues like molding, so we needed a system that would seal our roof and an area of the building inside a heated room to be able to produce our pallets properly."
DeFord Insulating Company was brought in for the job, which entailed applying spray foam to the underside of the 57,000 sq. ft. roof and to a small area inside a heated room where the Tasler workers store their fresh lumber and produce their pallets (a critical area in which to prevent condensation). The area consisted of four feet coming down from one of the exterior walls of the building.
By the time the crew from DeFord Insulating came on site, the Tasler crew had removed all the inundated fiberglass from both the roof and the small area of the heated roof. The DeFord crew wore PPE and fresh air respirators. The doors of the facility were kept open at all times for ventilation. The crew used 3M masking film to protect some of the roof's three-foot by five-foot skylight panels, and they also masked off the doors of the facility for overspray protection. The crew was using a man lift that lifted the crew approximately 20 feet off the ground to the underside of the roof. Caleb DeFord, owner of DeFord Insulating, mentioned that the floor of the facility was not prepped because, since the crew was 20 feet off the ground on the lifts, the foam was cured by the time it landed on the floor. Because the foam didn't adhere to the floor, it was easily swept.
The crew utilized Foamsulate 210, a 2 lb. closed-cell SPF made by Premium Spray Products, for the duration of the project. They applied one inch of foam on the underside of the roof and two inches on the heated room wall area for a total spray area of 72,000 square feet.
With one rig on site, equipped with a Graco Reactor E-20 proportioner and a Graco Fusion air-purge spray gun, the three-man crew completed the job in four weeks, pulling 10-hour shifts daily. DeFord mentioned that the Tasler workmen stored their equipment inside the building and constantly had to move it from the spray area to prevent damage to it as the project progressed. He said that even though it was a challenge to work around the Tasler staff and their equipment and pallets, the project went smoothly and the crew was able to work at a fast pace.
"We had to coordinate with the staff when we wanted to spray certain areas that might have not been available to work in on a given day," said DeFord. "It must have been a hassle having another outfit there while they tried to work, so we worked fast and got the project done ahead of schedule, which made them really happy."
DeFord noted that the SPF insulation application has sealed the building from condensation, which is going to create a unencumbering workplace environment for the workers.
"The forklift drivers are not going to have to dodge the ice piles coming down during the winter and deal with the water dripping down during the summer," said DeFord. "The pallets will not get dripped on so there will be no risk of molding, so that the pallets that they ship out to their customers will have the best quality all the time."
According to DeFord, SPF insulation will greatly benefit the heated room during the winter. Since the room is used to keep fresh lumber dry for pallet production, significant energy was required to heat the room. With SPF insulation, DeFord claimed their energy costs will be reduced because the room will not need as much energy to retain warmth.
"Insulating that room with a a system that doesn't become soaking wet and, in turn, gets everything inside that room soaking wet is going to give the Tasler workers the ability to increase their production capacity because they'll be able to dry out their lumber with ease," said DeFord.
Jacobsen was very satisfied with DeFord's work, and even though Tasler hasn't gone through the winter yet, he said that the facility has had consistent production with no condensation issues.
"I honestly think all our problems with condensation our over," said Jacobsen.
About DeFord Insulating Company: Servicing the state of Iowa and surrounding areas, DeFord Insulating Company provides professional, personal service in both commercial and residential applications. Their customers are large-scale agricultural co-ops, small-town homeowners, commercial contractors, and business owners. DeFord Insulating focuses on providing outstanding service to their customers by finding the most cost effective and professional way to meet their unique needs. For more information on DeFord Insulating Company, please refer to the links and information provided below.
Disqus website name not provided.