Surfs Up, Toxins Down
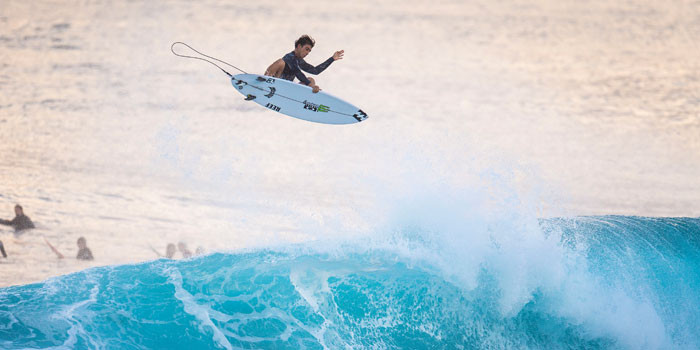
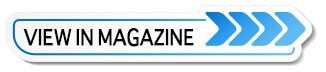
Spray Foam Magazine – Spring 2021 – On first glance the spray foam industry and surfboard manufacturing appear to have little in common. However, their environmental vision is remarkably similar: incorporating sustainable and recycled materials into their foam while looking for alternative eco-friendlier bio-oils.
Surfers spend a lot of time in the water, and they see the effects of pollutants from plastics, trash and even old remnants of wetsuits, which were traditionally made from neoprene, a non-renewable fossil fuel-based material. Surfboards were originally made from wood and in the late fifties/early sixties, the introduction of the polyurethane and fiberglass board became popular.
Many surfers still struggle between having a great board that performs well versus knowing that these materials are not fully biodegradable. The surfboard blank is the foam core of a surfboard that is usually wrapped in fiberglass and resin. The most common surfboard blanks are made of polyurethane foam, although EPS foam (expanded polystyrene, fiberglass cloth, and epoxy resin) is becoming increasingly popular.
The use of polyurethane continued to be the “normal” in the surf industry for the next 50 years until California-based surfboard blank manufacturer Clark Foam, unexpectedly closed its doors in 2005. Clark Foam highlighted problems with government regulations with the chemicals used to manufacture their blanks to be the reason for the closure.
At least 90 percent of the American surfboard shaping industry once used Clark’s polyurethane blanks for shaping their boards and the industry could have gone into some kind of panic when they closed their doors. Luckily, there was a silver lining, a serendipity. Could this have been the next step in revamping the industry? The leverage needed to help create the ultimate eco board that many surfers had dreamed of?
The EPS boards have been around since the seventies, but since the closure of Clark they have become increasingly popular due to the density of the foam and also being lightweight, which makes them easier to maneuver in the water. Are these EPS boards better for the environment? The epoxy resin has less volatile organic compounds (VOC). According to Sustainable Surf, a California-based non-profit founded in 2011, there is an impact associated with the recycling process of EPS and polyurethane foam. The impact of collecting, transporting, and reprocessing waste from EPS foam is however lesser compared to the impact of extracting oil and refining it to produce virgin petroleum-based foam.
One of the most exciting discoveries was back in 2015, when students headed by their professor, Stephen Mayfield at the University of California, San Diego California Center for Algae Biotechnology (Cal-CAB) and surfboard manufacturer Arctic Foam, created the world’s first algae-based, sustainable surfboard.
Arctic Foam started business in 2006, just after Clark Foam closed its doors, with Marty Gilchrist as the CEO, Andrew Jakubowski the President and Secretary James Mullen. These surfers are part of the California surf movement to make surfboards sustainable and eco-friendly. They applied their knowledge of surf manufacturing to help the professor and his students produce the world’s first algae-based poly surfboard. The chemistry students managed to alter the oil obtained from the laboratory algae into different kinds of “polyols” and it’s these polyols that expand into a foam that hardens into a polyurethane. Petroleum is, in fact, algae oil which has been fossilized for 300 to 400 million years and buried deep underground. The foam was then formed into a surfboard’s core and this core, even though made from algae, was white and looked the same as petroleum-based surfboards, due to the algae oil being clear.
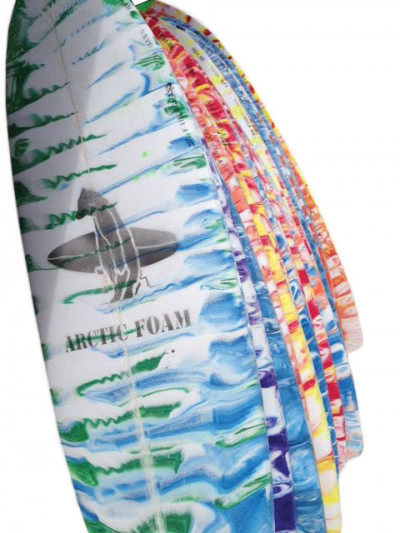
The nutshell foam boards can be shaped like traditional polyurethane boards and glassed with polyester, epoxy, or bio-epoxy resins.
Gilchrist said at the time, “We’re proud to announce our collaboration with the University of California, San Diego in producing the first poly blanks made out of 100 percent sustainable algae oil. Almost from the first blank out of the mold, we were seeing the kinds of density, cell structure, flex, torsion and “shapeability” we demand from our top-of-the-line P/U blanks. On top of that, we were able to keep to the aesthetics of our current line-up…avoiding blanks that look like something made out of lawn clippings. Our next step is to fine tune the formula and test the foam under the feet of the best surfers in the world.”
The non-profit, Sustainable Surf, is currently working on the analysis of the impact of recycled foam and will publish formal results soon. Its co-founder Kevin Whilden said, “Polyurethane foam derived from algae feedstocks will make a more ‘ocean-friendly’ surfboard blank with a reduced carbon footprint. This is a dramatic advance for polyurethane foam and will accelerate the sustainable transformation of the surfboard industry. We are in the process of testing the Arctic Algae blanks for possible inclusion in the ECOBOARD Project Benchmark.”
The team at Arctic Foam want to do their part to help save the oceans and make sustainable products surfers want to use for the eco-factor, without negotiating on performance, Jakubowski emphasizes, “No one has ever made a sustainable surfboard blank before the Arctic Bio Formula! Working with the biochemists from the University of California, San Diego for three years building polyols from Algae and not oil was a very long and expensive process. We had pretty good results and we thought we had mastered it.” These algae foam boards can be shaped like traditional polyurethane boards and glassed with polyester, epoxy, or bio-epoxy resins.
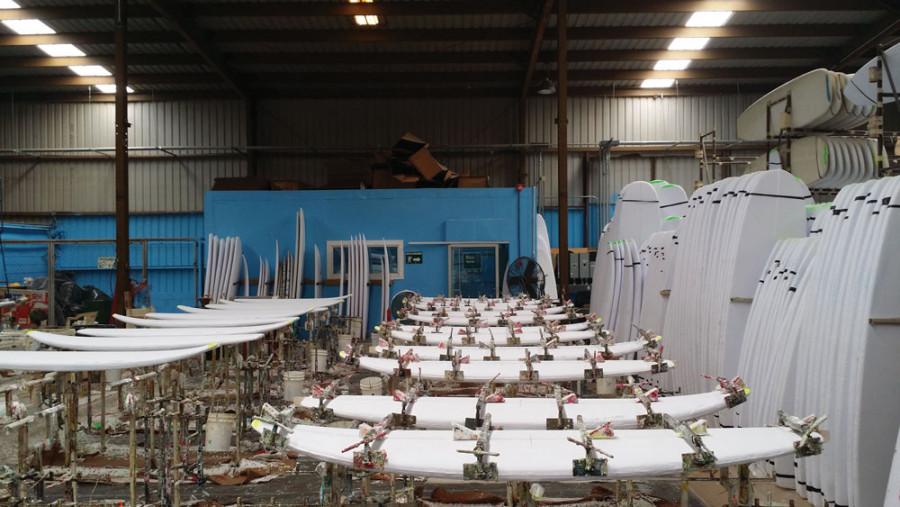
In 2015, a group at the University of California, San Diego teamed up with surfboard manufacturer, Arctic Foam, to create the world’s first algae-based, sustainable surfboard—seen being prepared here in the Arctic Foam factory.
Fast forward a few years and the Arctic Foam team noted a few complications with the foam, finding that for every 10 algae blanks, roughly two would be soft, which according to Arctic Foam, “It was unacceptable and second rate.” Finding the foam to be inconsistent along with some strength issues, they started to research the formula once again. Getting any PU formula perfect takes time and lots of research because the PU can be affected by changes in humidity levels and environmental influences. It looks like the Arctic Foam crew has cracked this problem.
During the COVID-19 lockdown, the Arctic Foam team decided to double down on another bio polyol in the hope of improving the algae-based foam. They found by taking out the Algae polyol and adding in more of the nutshell bio polyol, they drastically improved the foam. Gilchrist explains further, “Wouldn't you know it, the foam was perfect! The new bio polyol foam cell structure became tighter and more consistent also the foam was much firmer with no sift areas. Flex and impact strength also improved. All of which matched our standard for our current PU Foam. The new bio foam is available and in production and it’s the first Bio PU surfboard foam in history.”
According to Arctic Foam, almost all the Pro Surfers in the world ride Arctic Foam including the current Men’s and Women’s World Champs. “The Pipeline Masters, held this last December on the North Shore of Oahu, Hawaii, had everyone in both the men’s and women’s finals riding Arctic,” said Gilchrist.
Spray polyurethane foam (SPF) is made of a blend of petroleum-based chemicals that are mixed as they are being sprayed and many of these chemicals are regulated by the EPA. How is the spray foam industry making similar strides to that of the surf industry? Incorporating more sustainable bio polyol into the SPF? Many plant-based bio-oils are non-toxic, renewable, and recyclable and by using the oils from natural materials like nut shells or soybean plants, these oils can help replace the isocyanates and MDI. The foam however would still be petroleum-based. How can the industry lower the percentage of certain chemicals while still ensuring a great product?
Many manufacturers already use soy-based foam, like Huntsman Building Solutions Heatlok products. Huntsman’s Global Director of Product Management, Jean-Francois Lupien clarified, “Our technology allows us to use a variety of bio-oils like soybean oils. We can use coconut oil, cashew oils and bio-oils, but HBS has chosen soybean oil for its bioavailability and the fact that it is mass-produced in industrial grade. Our usage does not include food-grade soybean oil typically used as cooking oil. Our Heatlok HFO Pro and Heatlok HFO High-lift use ultra-low-global warming potential blowing agents and offer bio-sourced content and recycled PET plastics at an equivalent rate of 3,000 water bottles per drum, making it a sensible GreenGuard Gold certified insulation material.”
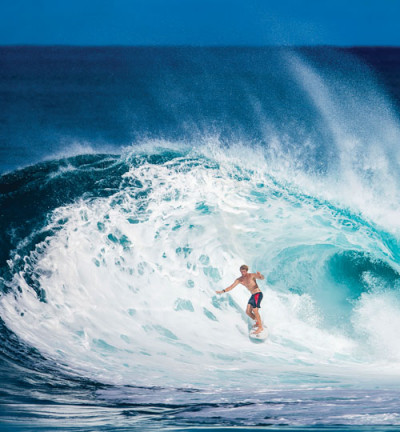
Soy is also a renewable resource and buying soy supports the 600,000 soybean farmers in the United States while reducing dependence on foreign oil, helping to cut down on transportation fuels and emissions.
Vice President of Global Product Development at Rhino Linings Joe Jibrail explains one of their company efforts in helping the environment, “Rhino Linings uses a proprietary polyester polyol technology, based on recycled PET from sources such as recycled plastic bottles and other polyols from biodiesel processes.”
Not only is Arctic Foam focusing on making their boards increasingly eco-friendly, but they have also partnered with Waste Management and Solar Turbines to reuse the hefty quantities of bubble wrap used in the shipment of large turbine equipment to protect fragile surfboards during shipping. This has resulted in cutting Arctic Foam’s bubble wrap expenses and waste. They feel so passionately about this, they have also distributed the bubble wrap to other like-minded surfboard brands for reuse.
Arctic Foam are visionaries in science, the environment and the development of eco foams, and they have plans to take their Bio Formula to the construction industry. “COVID has caused a few setbacks, but since June 1, 2020, we have received permission to run our factory full time and have been working double and triple shifts shipping containers of our surf blanks worldwide.”
Three surfers who believe in transforming polyurethane foam into a more sustainable and eco friendly material are causing a swell in the ocean. By listening to their market, using the earth’s natural materials and working with polyurethanes, they are helping transform a reliable surfboard material into something greener. Could these surfers help accelerate advancements in the foam industry and are there any lessons the SPF industry can learn by riding these waves with them?
Disqus website name not provided.