The Recreation of a Library
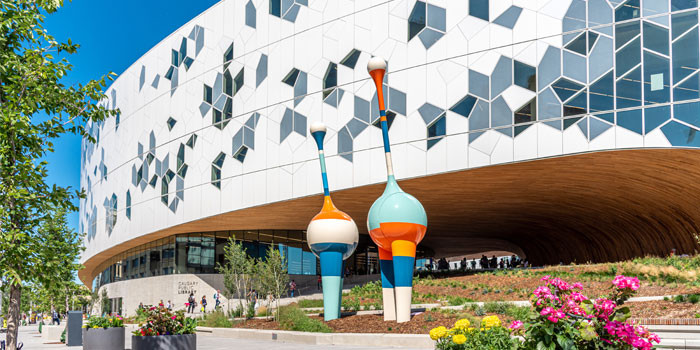
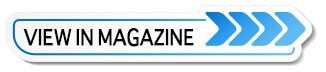
Summer 2020 – Spray Foam Magazine – Situated in the southwestern part of Canada, next to the Bow River and just under 50 miles from the Canadian Rocky Mountains, the charming city of Calgary required a brand new library. We interviewed Beyond Foam Insulation Ltd, who were hired to spray the Calgary New Central Library (NCL), in order to prevent any unwelcome moisture penetrating through the envelope’s structure in addition to keeping the building warm. Spray foam was an obvious choice for the architects and builders when specifying insulation for an area which has such a high-water table and cold weather temperatures.
The new library opened on November 1, 2018, replacing the existing central branch in downtown Calgary. Costing $245 million to construct, it was designed by American-Norwegian architecture firm Snøhetta and Canadian firm DIALOG.
The aesthetic design is an oval shape with the interior encapsulating a large central atrium with a skylight. The building has an elevated floor above street level with a light rail trackway below as well as a public plaza with the lower floors containing the library’s meeting spaces and activity centers. The upper floors feature book stacks with space for 450,000 titles and a reading room. At street level, one floor below the main lobby, is a 340-seat theatre, conference rooms, and a café. The design of the library was to have a number of environmentally friendly features like triple-pane windows to save energy on climate control, spray foam insulation to minimize heat loss and finishing materials made of low volatile organic compound.
Beyond Foam Insulation, co-owned by Curt Janzen and Kevin Boschee, is a family-owned-and-operated business serving Calgary and the surrounding areas since 2006 providing services in spray foam insulation and fire and thermal coatings, in addition to spray foam roofing and roof repair.
They were hired to spray the underside of the cantilever with the area of the job being 38,230 square ft. They used a Dual H40 spray foam rig, Graco Tough Tek F680E, a 150-foot stick lift, an 85-foot lift, and a 65-foot lift.
Curt Janzen managed this particular project and said, “We had the privilege to assist in the construction of the NCL (Calgary New Central Library), ensuring the building was both aesthetically pleasing and energy efficient. In order to achieve both the visual and green goals, it was necessary to insulate over 38,000 square feet of exposed floors from the underside. The sole solution for this area was spray foam insulation.”
Spray foam was essential for this scope of work because it required both insulation and an air barrier under the floor. The alternative to using 2 pound closed-cell foam would have been to install a composite membrane adhered to the underside of the 3-inch Q deck and then mechanically fasten insulation to the underside.
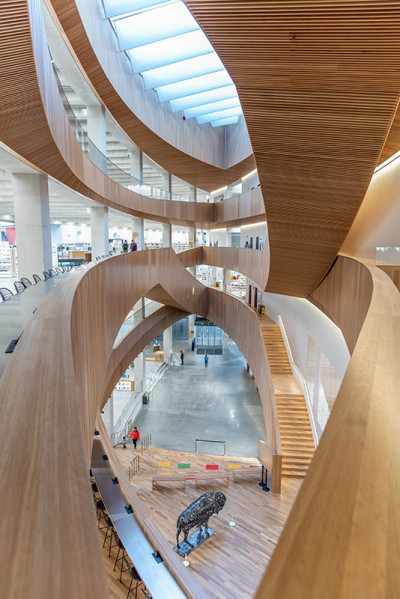
In order to achieve both the visual and green goals, it was necessary to insulate over 38,000 square feet of exposed floors from the underside.
Photo by Jeff Whyte - stock.adobe.comThe savings in foam over the labor to membrane and mineral fiber insulation was substantial. Foam outperformed the alternative in both cost and heat loss calculations. “Nothing else would perform the way foam did,” stated Janzen.
The job had to be modeled to ensure a satisfactory amount of insulation was installed. The builder, Stuart Olsen, hired Dialog Architecture out of Calgary to design and ensure it was installed correctly. Dialog made unscheduled trips to the site with the spray foam crew taking them up on the lift to ensure the foam was being installed to the manufacturer’s specifications and depths. The crews would send pictures of the pull tests for adhesion and cohesion on a daily basis, as well as density and work record documents. This information was kept in a shared file with Dialog and the builder.
The building was modeled to have an average performance of R40 2lb foam, which created both an air barrier and insulation. The foam applied was BASF’s Walltite Eco v.3 2lb closed-cell foam. The use of Walltite Eco was also an advantage on the project due to its LTTR (long term thermal rating) per inch being higher than that of the competition. The high volume of recycled material and renewable resources in the product also made it the right choice for this particular job. BASF has a plant within 30 miles of the install site, making it a locally produced and installed material.
In an effort to protect the foam and floor above the thermal barrier, Grace Monokote Z-3306 was applied. This product is a cementitious fire protective coating purposely formulated for application over rigid, urethane and polystyrene foam plastics. It can be applied to interior foam surfaces on walls and ceilings forming a hard, durable, monolithic thermal barrier against heat and fire.
The project was logistically challenging, with the crew having to work off boom lifts for the entire project, with the height of the working area varying from 30 feet to 60 feet in the air. Additionally, the work site was small and very busy with seven to eight other lifts and hundreds of trade workers. A portion of the crew’s range of work was to protect all the glazing and finished concrete panels from overspray of foam and mud. The crew, with the help of the general contractor, created a custom channel which attached to the top side of the glass in order to terminate the spray foam and ensure they had satisfactory coverage to meet the specifications of the drawings on the curtain walls.
An extra challenge was Calgary Transit’s C-Train, which traveled straight through the middle of the NCL. Janzen recalls, “At the north tip, the train is above ground and by the time it gets to the south side, it is completely underground. Consequently, we were not able to get close to the building with the lifts, as we could not drive over the top of the ramp. To spray this region, we needed to use a 150-foot lift, and for the closer areas the crew worked off of 65-foot lifts.”
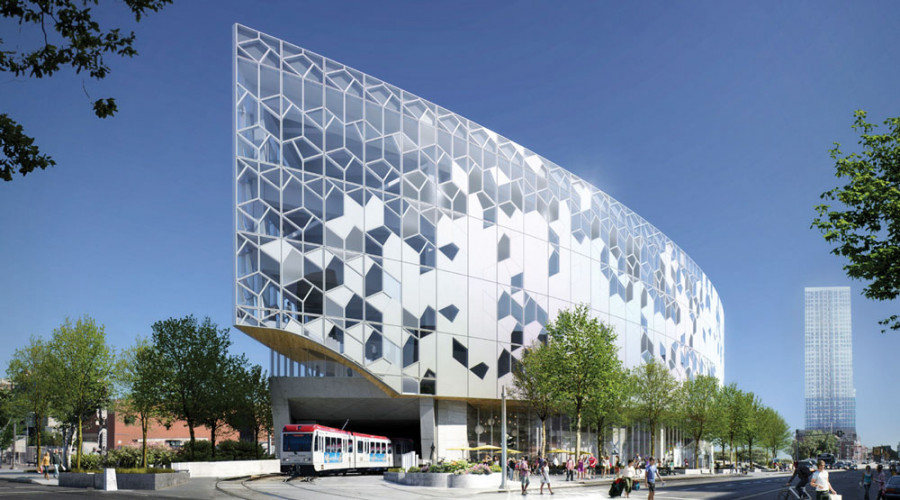
Because the Calgary Transit's C-Train travels straight through the middle of the NCL, the team from Beyond Foam Insulation could not get close to portions of the building with their lifts. So to spray the specific region, they needed to use a 150-foot lift and 65-foot lifts for closer areas.
Render of the Calgary Central Library, source: www.evexperience.comTo be able to complete this job in a timely manner, Beyond Foam used their dual reactor spray foam rig which has two H-40 Graco pumps. They also used a Hyflex HZ-30E to install the thermal barrier over the foam. The application was partially completed from inside a five-ton truck, and partially on a ramp where they left equipment and mixed mud.
Stuart Olson’s Superintendent Mike Scheck said, “We at Stuart Olson had the pleasure of working with Beyond Foam for the application of the spray foam insulation and thermal barrier above the Western Red Cedar soffit. Due to cedar being installed in the panels, which were fabricated off-site, and the complex layout and anchoring system that had to be installed prior to the panels going in, the spray foam allowed us to get all of the layout completed and the anchors installed ahead of time. This was all achieved while still maintaining the vapor barrier and R-value required afterwards. We worked closely with Beyond Foam to facilitate their scope of work.”
Each staff member was required to go through a site orientation which was more in depth than typical commercial sites. Because of the exposed concrete features, there were site-specific rules for many things, including the type of tape and water bottles the crew could have on site. Additionally, adjacent to the job site was a homeless shelter, which resulted in the crew becoming knowledgeable about what to do when they found used needles.
Every crew member was re-certified in their fall arrest and lift training prior to working on the site. These certifications were documented and filed with the safety codes officer for Stuart Olson. Beyond Foam uses an in-house training program, which includes sprayer and helper levels of achievement. Their program starts with level 1 – 3 helper and goes up to level 1 – 3 sprayer with no installers employed on this project with less than a level 2 sprayer, as they needed to ensure accuracy in depths as well as quality of workmanship. The installers were also trained under BASF and have third party inspections by structural engineering company Morrison Hershfield.
Each day the crew had toolbox meetings discussing and recording site specific and general safety concerns. These meetings were also documented and shared with Stuart Olson as part of their best practices program. The highest priority for the owners of Beyond Foam was the safety of their crew and the numerous trades workers around them with each person on site trained with tickets in fall arrest, scissor lift and aerial lift.
The crew was in constant communication with the general contractor’s employees on the ground and other trade workers around them. Maneuvering lifts would, at times, take hours and before spraying they would have to red-tape off large areas to protect other trade workers from overspray or damage to their equipment and materials. While spraying, the crew was supplied with fresh air to their masks and all their own safety gear, including harnesses, high visibility vests, hard hats, gloves, and Tyvek suits.
Due to the large cantilevers on the building, the concrete slab that was poured above the work area, had to be staged to balance the building. The crew; therefore, had to be mobile and move under areas where the concrete was complete.
Janzen emphasizes, “Moving on this site was not an easy task because there were only two access points from either side of the building. Moving lifts and men was laborious. It was hours of hard work before we could get parking and re-deploy our hose to continue our application. The coordination between the exterior superintendent of the project, yard foreman, and our crews was a constant juggling act. Because of our willingness to be flexible with start times and partial days, this job was a success. Many days our crews would start at 3pm and work until 10pm while the site was empty of most workers with over 50 percent of this project being done after normal working hours on evenings and weekends.”
The site conditions with other trades coupled with weather conditions, protection from overspray, and tight deadlines required an efficient application. There were three passes needed to ensure proper depth of insulation, as well as a complete crew change to install the Monokote Z-3306 thermal barrier. The crew was frequently waiting for fire proofing and concrete pours to be completed in front of them while being pushed by the soffit install crew.
When the crew had access to an area, the install crews worked as efficiently as possible. Spraying up to two sets of foam a day does not seem difficult in an open space, however, the various site conditions, trades workers, and limited areas available to spray made this particular job challenging. Eli Mathison, the Senior Superintendent on site, said it was his opinion that the crew supplied and installed the spray foam insulation more than 3 times faster than a membrane and wool fiber insulation could have been. Because of this, it gave the soffit crew sufficient time to do their install before weather slowed them for the winter.
Imagine a world without libraries; pretty easy to do, especially for Generation X who may have never even stepped foot in one. Now picture a world where the internet stopped working; impossible, or is it? In these current times we have learned nothing is impossible, so we need to have libraries available for a source of knowledge, entertainment, and most importantly to learn from historical events. Using eco friendly materials, cutting edge design, and Beyond Foam Insulation’s company mantra, “Creating Warm Spaces and Happy People,” the future face of this library is a shining example of innovation, human connection, and progression in what was deemed a dying concept.
Disqus website name not provided.