The Rise of ThermoBlock
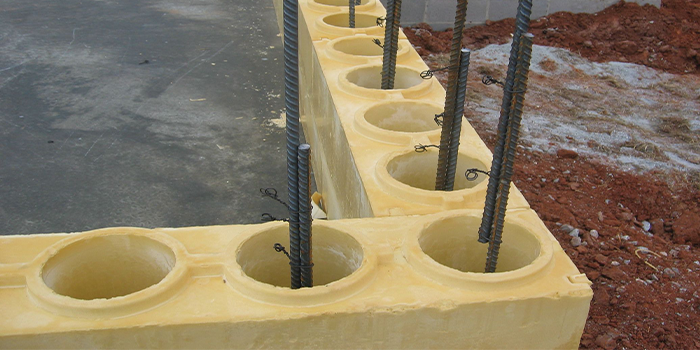
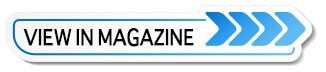
SPRAY FOAM MAGAZINE – In recent years, North America and Europe have witnessed exponential growth of insulated concrete forms or ICFs as a preferred green technology throughout the construction industry. In 2021, North America had the largest market share for insulated concrete forms (ICFs)in the world, at around 36%. This is due to the growing demand for energy-efficient buildings in the US and Canada.
But not all insulated concrete forms are created equal. For example, some ICFs can be difficult and costly to transport over long distances and require experienced contractors to ensure proper assembly. Two main challenges for most ICFs are keeping the walls straight before pouring and attaching internal and external cladding or finishing. ThermoBlock®,does not have these problems and enjoys many additional competitive advantages as well. ThermoBlock is an innovative cast in place, insulated concrete form that is inexpensive to deploy, easy to use, fast to construct and features state-of-the-art strength and energy efficiency unrivaled in the construction industry worldwide.
The ThermoBlock ICF system utilizes steel reinforced post and beam concrete construction. Resembling large scale Lego type blocks, the system uses a combination of interlocking, lightweight, stackable, polyurethane blocks, which can be fabricated onsite and in remote locations, together with concrete, steel reinforcing rebar, and a patented light gauge steel internal bracing system. Because the system utilizes high density closed cell polyurethane foam, it offers superior insulation value, is Class 1 fire rated - the bestrating possible, satisfies all seismic and hurricane code requirements, is not a food source, and thus is fully resistant to insects and other animals, eliminates mold and mildew and is exceptionally quiet.
The ThermoBlock ICF construction system creates a strong, stable concrete structure. It all begins with the ThermoBlock form.ThermoBlock ICF can work with a variety of footings or foundations.Rebar is stubbed in at 16-inch or 40centimeter centers. The ThermoBlock forms easily glide down the rebar and lock into place without mortar. To add stability and a nailing surface, metal studs are added on 16-inch or 40 centimeter centers. Wiring and piping are easily integrated into the ThermoBlock system using the existing ThermoBlock channels. Rebar is also added horizontally throughout the structure, forming a steel reinforced concrete grid to further enhance its overall structural integrity.The concrete is then poured into theThermoBlock from the top, creating an incredibly strong, insulated energy efficient structure. The ThermoBlockICF stays in place helping to insulate this steel reinforced concrete structure.
What's more, the system is easily transportable. A ThermoBlock ICF mobile manufacturing facility fits inside a single 40-foot shipping container, making it easy to bring in-country and onsite. This is ideal for remote locations and emergency situations, ensuring a steady supply chain, maximizing the use of local labor and eliminating costly and sometimes dangerous disruptions and delays.
In all, ThermoBlock provides a superior quality and secure living environment that can be deployed under budgets that make other technologies unattractive. Cost-effective, strong, and energy efficient, fast, in-country manufacturing with a minimal learning curve and easily transported to any location, it's all part of what makes ThermoBlockICF the best way to rapidly and cost-effectively provide superior quality vertical infrastructure, improve living quality standards for users of homes and public infrastructure, build localc apacity, and create permanent jobs in any location worldwide.
For use by SprayFoamMagazine.com & Spray Foam Magazine
Disqus website name not provided.