The Whole Package
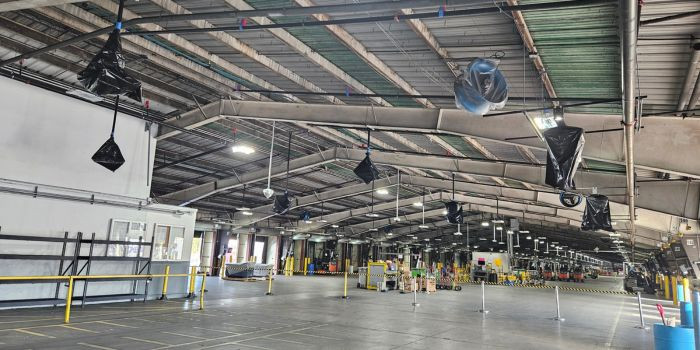
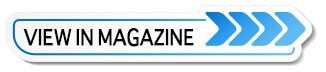
Spray Foam Magazine – Show Issue 2025 – Wintertime means the nights get longer and the weather gets colder, but with holidays around the corner, most businesses start heating up. In no industry is this more apparent than in the shipping and logistics sector, whose delivery fleets and massive warehouses route millions of packages around the globe. In the fall of 2024, TCS Insulation & Coatings spent a month on-site at one such sprawling shipping warehouse owned by a global courier transportation corporation. TCS foamed the 80,000-square foot facility’s roof deck and walls with UPC’s High Lift HFO Winter closed-cell spray foam, finishing it off with an application of No-Burn coating, just in time for the busy winter season.
Based out of Brainerd, Minnesota, and owned and operated by Freddy Lewis, TCS Insulation & Coatings is accustomed to trekking around the Midwest. This time, they’d only have to make a two-hour drive south to a city in MN’s Twin Cities area. Being close to their local stomping grounds made commuting easier, but the job required all hands– and machines– on deck. They brought with them all six employees, including Lewis himself, plus their rig containing two Gusmer GH-2s, and five scissor lifts instead of their usual three. On any given day, they haul around about 10 sets of foam– for this job, they ended up using 85 sets of foam and 900 gallons of No-Burn total.
Lewis got wind of the project through the industry grapevine. A colleague told him that an Alaska-based general contractor who specialized in shipping facilities was in Minnesota seeking bids from insulation companies for a huge job. Lewis knew the TCS team would be a great fit for the project, being both materially prepared and highly skilled in their trade. Not to mention, it was close to home.
“We bid, and actually had to submit the bid twice because the timeline changed– but we ended up winning,” said Lewis.
The company and general contractors chose to insulate with closed-cell foam for several reasons, primarily the ease and speed of installation. The goal was to minimize disruptions to the warehouse’s daily operations while completing the job quickly, making SPF a clear winner over other options.
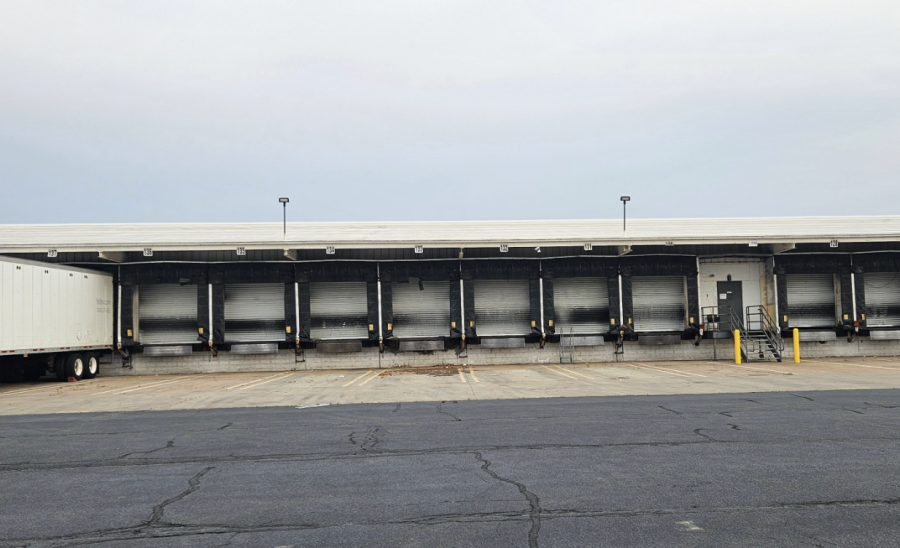
The bay doors lining the facility made insulating the building difficult, but not impossible.
“Originally they thought about doing fiberglass, but that would have been impossible with everything they had mounted to the warehouse’s ceiling,” Lewis recalled, “All we had to do was cover everything up and spray around it.”
Adding insulation and heating to the facility was long overdue. The warehouse building had never been heated, which is an impressive feat for a building in Central Minnesota where temperatures are known to drop below freezing on a regular basis.
“Their biggest problem was that the concrete floor would freeze and that would make the inside of the building 10 to 15 degrees colder than outside,” Lewis explained. He also stated that the facility intended to install radiant tube heaters and insulated bay doors throughout the facility to work in tandem with the new foam insulation.
While excited about winning the bid, Lewis and his team knew going in that the site came with a host of challenges to navigate. TCS began working at the job site in late October 2024, just as the warehouse began shifting into its peak season. It was critical that the warehouse always remain operational, which meant they could only foam small sections of the warehouse at a time. Every morning, they’d arrive and set up in a new part of the warehouse, and every night they’d clean up, leaving behind only the newly installed foam.
To minimize disruptions to themselves and to the warehouse, TCS worked at the facility during the day since most of the freight is shipped at night between the hours of 5pm and 5am. Although the day shift was less bustling than the night shift, more than 50 forklifts would whizz by the TCS team on any given day, no matter which part of the warehouse they were working in. Occasionally, those days would stretch into nights.
“A lot of times we wouldn’t get out until 7:30 or 8pm.” said Lewis, remembering how hectic the warehouse would get past 5pm.
In addition to the busy work environment and the staggering amount of material needed for the installation, TCS would also have to do intensive preparation to get the metal roof deck clean enough for good adherence. Given the size of the job and its busy location, the TCS team had expected to encounter some quirks in their daily routine and weren’t phased by having to remove decades-worth of dust if it meant the best adherence for the UPC foam.
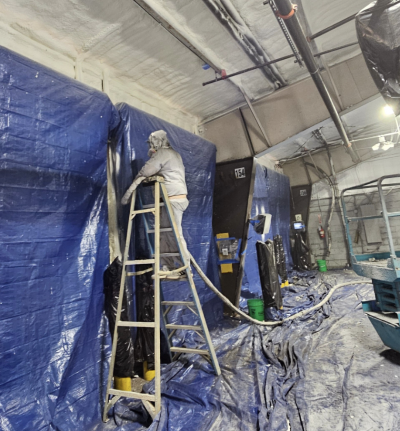
A TCS sprayer foams the small section of wall between the ceiling and bay door
“It was an older building, and there was dust everywhere, covering every purlin,” Lewis recalled. “So everyday we’d come in, section off, lay the tarps, and clean the surfaces. Then we’d spray it, coat it, and take it all back down, every single day. Must have cleaned that entire building.”
After making sure the substrate’s surface was as clean as possible, they hung giant tarps on the walls and bay doors and used the scissor lifts to cover any ceiling fixtures with plastic to guard against overspray.
From plastic tarps to equipment, they came well-prepared for anything the job might throw at them. The TCS arsenal is a point of pride for Lewis, who is quick to fire off its features:
“It’s a 44-foot double pumper rig with two Gusmer GH-2s, a 60 kW generator, 10 horse, variable speed, rotary screw air compressor… and the new Graco Fusion FX guns.”
For personal protection while both spraying and coating, they suited up with protective coveralls, gloves, and 3M 6000 Series Full Face respirators.
The warehouse’s entire metal roof deck received a layer of UPC High Lift HFO Winter closed-cell spray foam with a value of R-28. The small section of metal walls between the roof and the top of the bay doors also received a layer of foam with a value of R-24. Afterward, they finished off with a coating of No-Burn.
The No-Burn coating was added to comply with the facility’s commercial specifications requiring any exposed foam not covered up by additional materials (such as drywall), to have a coating applied. In this case, the No-Burn’s brilliant white color brightened up the facility’s interior while adding fire retardant properties– a plus for any building, but a must for one filled to the brim with boxes of freight. When all was said and done, they used approximately 85 sets of foam and about 900 gallons of No-Burn—a massive haul, even by Lewis’ standards.
After a month of work, Lewis and the TCS Insulation & Coatings team finished foaming the entire warehouse on November 21st, just in time for the facility to process hundreds of thousands of packages over the holiday season. The entire building now has a continuous vapor barrier to help achieve and maintain peak thermal efficiency through the coldest and darkest months.
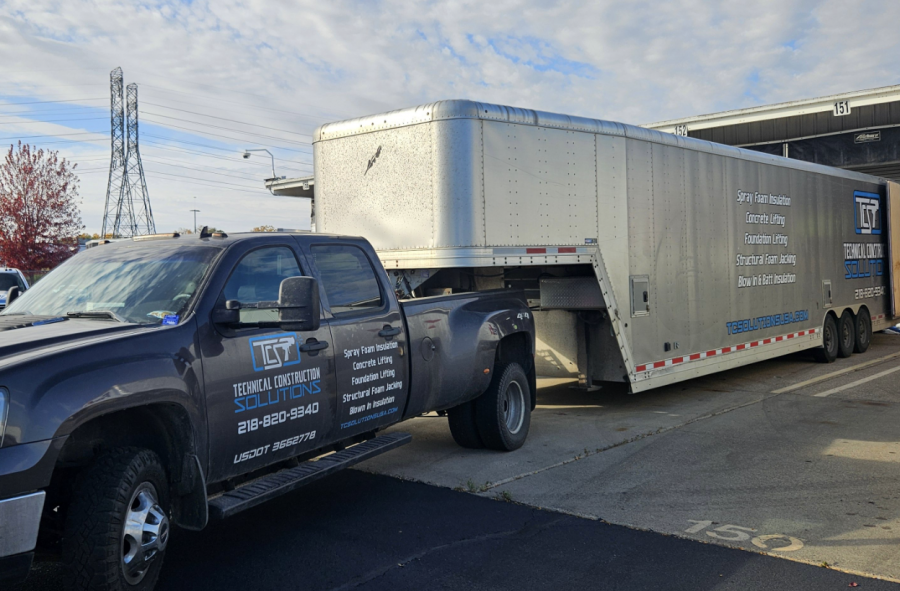
TCS Insulation & Coatings truck and rig parked outside the shipping facility.
Disqus website name not provided.