Understanding Code & Emerging NFPA-275 Spray Foam Technologies
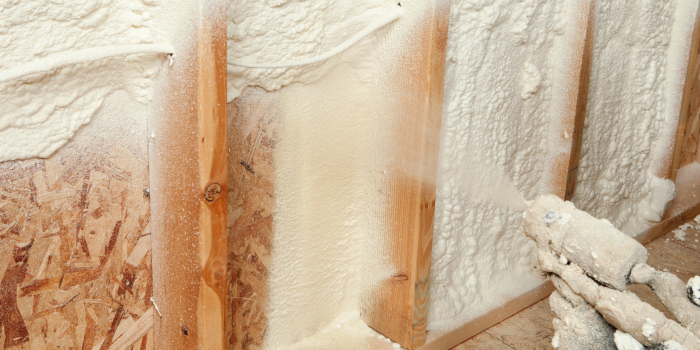
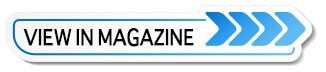
SPRAY FOAM MAGAZINE – To run a successful spray foam insulation business with a competitive edge, spray foam installers must stay abreast of the ongoing changes in technological advances.
Plastics require significant fire and smoke approvals to be utilized within the building envelope. Ongoing learning and awareness are necessary and an important risk management consideration. One complex area around plastics (and foamed-in-place insulation) is satisfying International Building Code (IBC) and International Residential Code® (IRC) requirements.
Emerging fire barrier, single-step foamed-in-place technologies have overcome major fire barrier challenges, especially around thermal barrier compliance. However, before truly understanding the benefits, it is critical to understand basic fire and smoke requirements and address the existing confusion.
the world of IbC Chapter 26 and thermal Barriers
According to the code, all plastics installed in the building envelope require an additional thermal barrier. IBC Section 2603.4 defines thermal barrier and four various deviations, derivatives or direct compliance approaches to allow the safe application of plastics.
Figure 1 illustrates three of the four methods.
The fourth ‘equivalent compliance’ method identifies a multi-test test protocol (National Fire Protection Association – NFPA 275) for achieving an equivalent rating to gypsum (Figure 2). Any product that strives to be equivalent to half-inch gypsum must meet this protocol.
Historically, spray polyurethane foam (SPF) met code by being applied behind gypsum or covered with approved, add-on thermal barriers, i.e., cellulosic and cementitious materials. SPF could also comply with code through “exception” methods using the lower-level ignition barrier approval (method two) or special approval testing (method three).
When choosing one of these methods, the questions are…
Which test(s) should be used?
Which combination of coatings, cellulose or cementitious materials should be used?
Over which foams?
At which thickness?
In which densities?
Addressing all combinations of SPF/coating/cellulose/cementitious solutions and the appropriate paperwork required by building officials is a separate topic in itself.
My 15 Minutes aren’t Your 15 Minutes:
Companies often claim fire approvals to IBC 2303.4 - 2603.9 (usually as a function of time). The test behind the measure can be inaccurately communicated, creating confusion and potential safety violations. A clear example is the pass/fail identical time requirements of exception tests versus the gypsum approval versus the verified thermal barriers. (Figure 3)
Prescriptive method one (gypsum) follows historical performance results and ratings of 15 minutes based on ASTM E119 “temperature transmission testing.” Also known as the compartmentalization of fire test, it tracks the time it takes for extreme heat to pass through a wall or ceiling, creating a fire risk adjacent to the space compromised by the fire.
Exception method three (special approval) defines
a 15-minute period where flame spread and smoke from a known fire source in an eight-foot by 12-foot room cannot exceed safety levels of flame and smoke –15 minutes estimates a safe time to evacuate.
Method three allows an exception, but “code-allowed” solution, to life safety but does comply with temperature transmission risk. Although both tests have 15-minute durations, they certify two very different life-safety criteria that are not interchangeable.
Direct compliance, method four (NFPA 275 – the equivalent thermal barrier), is a test protocol that requires both tests – the temperature transmission test and the flame/smoke test, both being 15 minutes. Method four passes the prescriptive and special approval solution and defines an equivalent thermal barrier to the gypsum prescriptive method.
Monolithic Fire Performance
Current post-applied “exception-based” thermal barrier solutions become daunting when trying to ensure correct, safe application; they need to be properly applied, require third-party inspection, and are utilized only in “conditioned spaces.” Also, as soon as the thermal barrier is breached, the fire protection of the flammable substrate is lost.
NFPA-275 SPF products achieve fire performance monolithically. The foam fire barrier is built into the composite and is protective throughout the complete volume of the insulation – against fires from the outside in, and inside out.
Even with thermal barrier technologies in NFPA 275 foam, the benefits of continuous insulation, air and moisture barrier, mold defense, structural rigidity and high-insulation value are maintained. Monolithic fire protection means safer solutions, fewer added steps and materials, less cost and risk, versus a post-applied thermal barrier coating, cellulose, etc.
Reducing risk Window
NFPA-275 foam becomes an effective fire barrier as soon as the chemical reaction finishes. What benefit does this provide? Fire safety is “built-in” as soon as the foam reaction is complete, providing a “zero risk window” and is very different from traditional methods where flammable plastic insulation materials, both panels and continuous, require an additional thermal barrier post installation. That gap in time waiting for the post-applied thermal barrier poses a life-safety risk and liability.
Paradigm Shift – SPF enters the Fireproofing Realm
An often-overlooked paradigm credited to monolithic NFPA-275 SPFs is the ability to increase rated fire resistance. Historically, this has been reserved for non-combustible building elements like brick, stucco and concrete. By passing ASTM E119, NFPA-275 SPF reduces temperature transmission through walls and ceilings. As the thickness of the monolithic fire barrier SPF increases, so does its ability to delay the transmission of heat and poisonous fumes, increasing the overall wall system’s hour rating.
This extends the thermal barrier SPF into the realm of fireproofing; something previously unachievable and opens many new and creative avenues.
Embracing the benefits
Architects, builders, contractors and even end-users care about better value. NFPA-275 thermal barrier high-R insulation liquids cost slightly more initially. However, the total costs, including speed of installation, overall quality and end-user impact generate significant value across the complete construction hierarchy, resulting in significant cost savings, with costs decreasing as market penetration increases.
These new technologies are improving total costs and margins in major areas of construction, such as commercial, government, union and prevailing wage projects. These benefits translate into other large
fringe areas, such as agriculture, commercial cold storage facilities, grow houses, outbuildings, military and aviation hangars.
The elimination of steps translates into lower costs, more efficient installations, and most importantly, a lower risk for the loss of life and property…a true trifecta of value.
*Spray Foam Magazine does not take editorial positions on particular issues; individual contributions to the magazine express the opinions of discrete authors unless explicitly labeled or otherwise stated. The inclusion of a particular piece in the magazine does not mean that individual staff members or editors concur with the editorial positions represented therein.
For use by SprayFoamMagazine.com & Spray Foam Magazine
Disqus website name not provided.