Up & Running
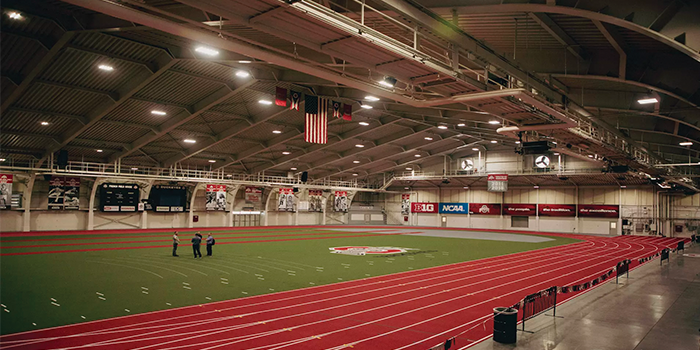
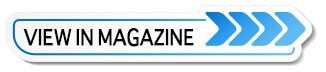
SPRAY FOAM MAGAZINE – Ohio State University (OSU), home of the Buckeyes, is heralded as a national champion in athletics like baseball, football, and basketball. OSU’s culture takes sports and athletics seriously, so when school administrators noticed the indoor track at Ohio State University’s French Field House was experiencing problems caused by subsurface erosion, they knew it was time to call in professionals to solve the problem once and for all.
OSU’s French Field House features a 200 meter (just over 2000 square feet) indoor track that was built in 1956 and sees regular use to this day. Subsurface erosion is a relatively common problem for running tracks, and OSUs had been previously resurfaced a number of times in an attempt to stave off the track’s worsening erosion. Unfortunately, the track’s issues were compounded by the fact it had been originally built atop un-compacted dirt. Coupled with its overall age and rigorous use, the track’s problems would only compound unless the problems lurking beneath the surface were addressed once and for all.
One potential option was to completely excavate the old track and replace it with a brand new one, but a quote of over $1 million gave the school pause. OSU hosted a Lunch and Learn event to connect with local engineers, and there they met Joe Work, the owner of Cleveland-based concrete-lifting company Mr. Level. Work explained his company's approach to concrete leveling using a chemical grout made from polyurethane, also known as polyjacking or deep-soil injection. Mr. Level’s polyjacking process also included a lifetime guarantee backed by insurance, a unique benefit that piqued the school’s attention. Rather than excavating the track and replacing it outright, the school realized they could save hundreds of thousands of dollars by recruiting Joe Work and his crew at Mr. Level to use polyjacking to repair the track permanently without running up a steep bill.
In their consultations with OSU, Work enlisted the help of their material supplier, NCFI Geotechnical’s Polyurethane Division. Mr. Level and NCFI have a long collaborative history, and Work trusts the NCFI team’s judgment on the best polyjacking systems to use based on the needs of each individual job. They had to ensure that the track’s final result met the high standards of the National Collegiate Athletic Association’s (NCAA) in order to be safe for athletes to use, which meant they had to ensure a perfectly level and stable track surface. The teams at Mr. Level and NCFI Geotechnical determined that the best approach would be to use two advanced polymer polyjacking systems called Terrathane 24-010 and Strata-Fill 24-039, and they would use laser levels to monitor the process and keep the surface even.
Polyjacking is not the only method of concrete lifting available on the market; mudjacking is commonly used, though Work explains why polyjacking is a better deal for a more permanent solution, especially for a project as lucrative as the OSU track. The team at Mr. Level refers to mudjacking as the Flintstones approach, while polyjacking is known as the Jetsons approach. Mudjacking can be a quick and relatively inexpensive fix but it is not the best method for long-term results as it requires continuous maintenance as its subsurface continues to shift and erode over time. Polyjacking, on the other hand, provides a permanent leveling solution that does not require repeated applications thanks to the highly durable polyurethane compounds it's made from.
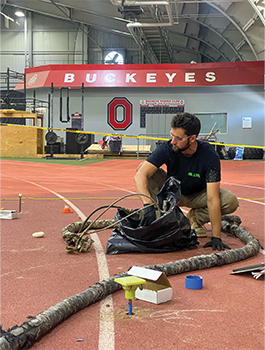
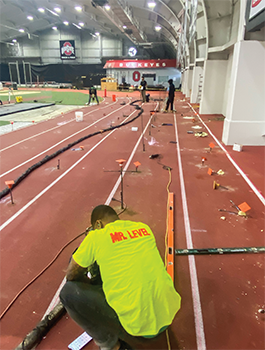
After working out the details with the school and assessing the job site, Work and his team began the deep-soil injection process in early May of 2023. A crew of five, comprised of staff from both Mr. Level and NCFI, including pumpers, helpers, and a supervisor. This small yet efficient crew completed the track’s polyjacking work over the course of just five days. NCFI Geotechnical provided the polyjacking systems (Terrathane and Strata-Fill), and a supervisor remained on site to facilitate and troubleshoot as Work’s team implemented the concrete lifting process. Work describes that many parties were invested in the project’s success: “There were a lot of hands on deck for this, because it was a very high-profile job.”
To stabilize the track without the need to excavate, the team completed the deep-soil injection leveling process in several steps. The running track’s topmost layer is soft and spongy to absorb shock, but the asphalt layer beneath it is prone to erosion and sinkage. Using five-foot grid patterns to map the area, the Mr. Level team bored two-inch holes into the soil’s subsurface at varying depths of three, six, and nine feet.
After drilling the holes to the appropriate depths, they placed three hollow ⅝ inch rods into the holes. Each of these rods corresponds to the correct depth needed to be filled with the polyurethane system. Using a GX-7 spray gun they injected each three-foot deep hole in the ground with up to 50 lbs. of Terrathane 24-010 to provide initial surface lift. After allowing the Terrathane time to expand, they injected Strata-Fill 24-039 at both six foot and nine foot depths, which permanently fills subsurface voids and compacts the soil deep underground. Though it is a relatively straightforward process it requires a great deal of precision to be effective: “Over-lifting can cause the asphalt to rise up slightly, known as turtlebacking. We had to make sure we pumped the appropriate amount.”
To prevent over-lifting issues, the team utilized laser levels to monitor the track’s lift and ensure only a specific amount of polyurethane volume filled each level. Because the process involves injecting layers of polyurethane beneath the ground's surface, common spray foam PPE like respirators and Tyvek suits were not necessary, though the team wore gloves, boots, and eye protection. They completed the job efficiently, and the track was ready for use less than a week later.
OSU was thrilled with Mr. Level and NCFI’s work; they completed the job quickly, adhered to the NCAA’s standards, and saved the school an estimated $900,000 by circumventing full excavation.
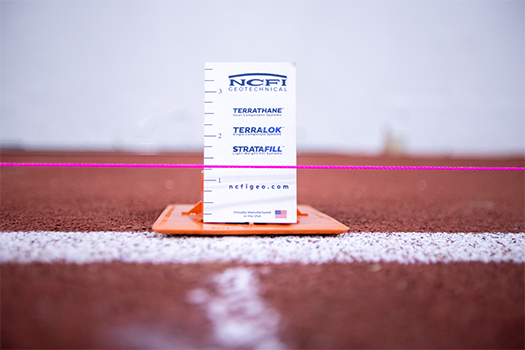
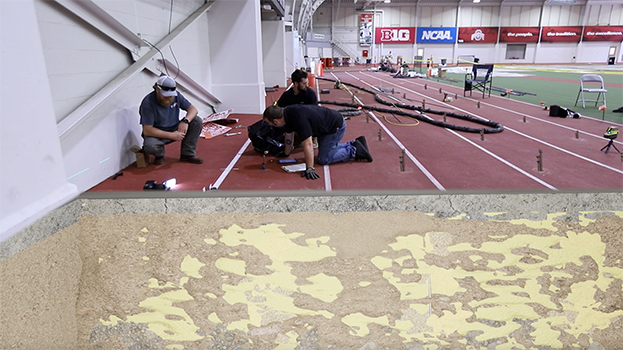
And what’s more, Mr. Level’s polyjacking services come with a lifetime guarantee on all their work, which further assures high-quality results. Work explains that they are the only concrete-lifting company in the nation whose lifetime warranty services are backed by insurance. If Mr. Level has to go back and fix a job for any reason, the company receives payment from their insurance rather than the client, hence the lifetime guarantees on all their work. Work and NCFI are working toward informing other contractors about the benefits of this method: “It’s really popular in the automotive industry, but now it’s starting to take place in other industries too.” Work himself is so dedicated to quality assurance and customer satisfaction, he wants to see the rest of the industry adopt these practices and solve customer’s leveling problems for life.
For use by SprayFoamMagazine.com & Spray Foam Magazine
Disqus website name not provided.